パナソニックといえば冷蔵庫や炊飯器など、生活家電メーカーのイメージがあります。ですが、実はどの家庭にも絶対ある「分電盤」の国内シェアNo.1メーカーでもあることをご存知でしょうか?
分電盤とは家の外から送られてきた電気を、各階や各部屋などに分けるための装置。とはいえ、実は分電盤とはどんなものかわからない人も多いと思います。そこで、今回は国内の分電盤シェアNo.1のパナソニック スイッチギアシステムズでイマドキの分電盤の凄さを取材。さらに、実際に分電盤が作られている工場の見学にいってきました。
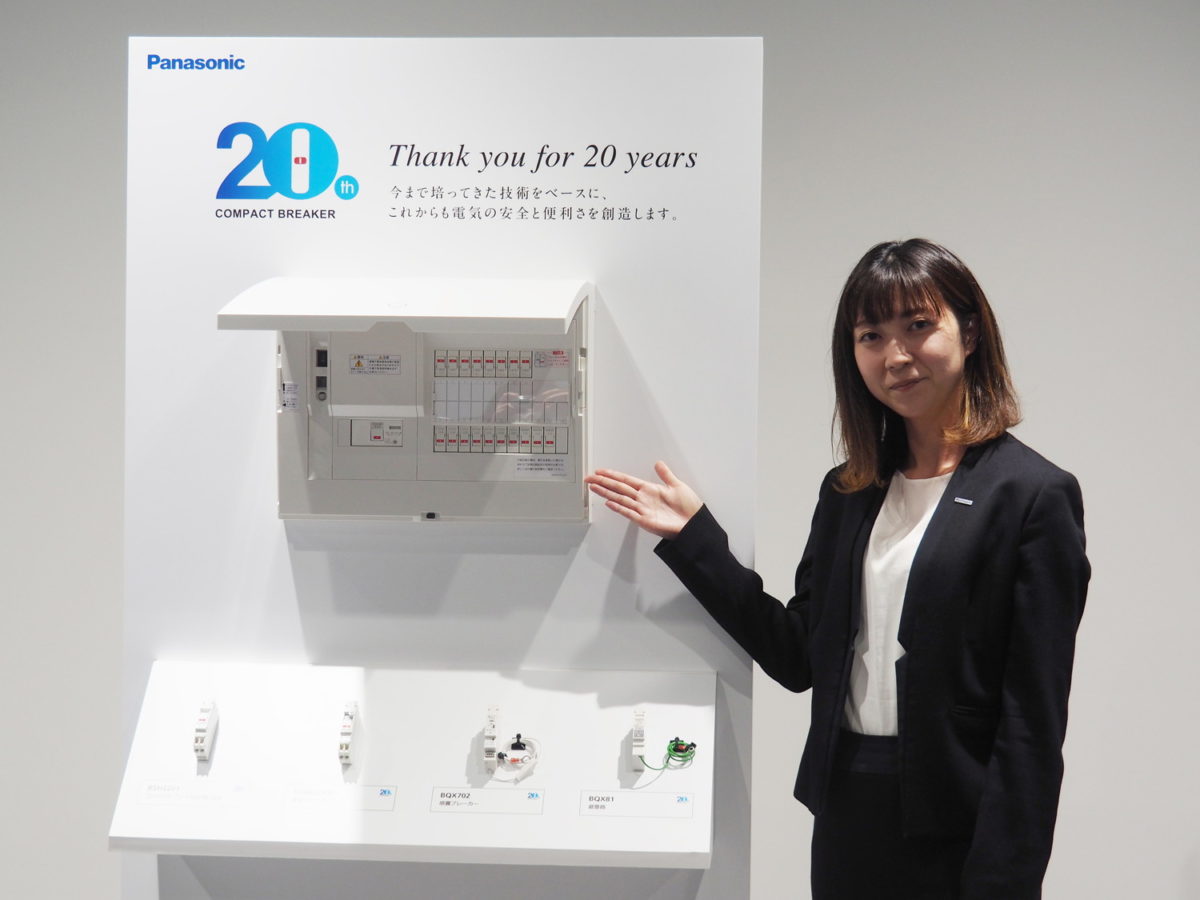
防災・節電に力を発揮する分電盤がコンパクト化
冒頭で分電盤のことを「家庭に入ってきた電気を分配する装置」と説明しましたが、分電盤はそれ以外にも、家庭の電気の安全を守るためのさまざまな機能を搭載しています。たとえば、たくさんの家電を同時に利用すると電気が切れることがありますが、これは「規定以上の電気が流れると電気を切る」という機能を持つブレーカーが分電盤に配置されているから。落ちたブレーカーを戻すため、脱衣所などにある分電盤に触れたことがある人も多いのではないでしょうか。このほか分電盤には、漏電や感電の危険性がある場合に電気を遮断する「漏電ブレーカー」として安全を守る機能もあります。
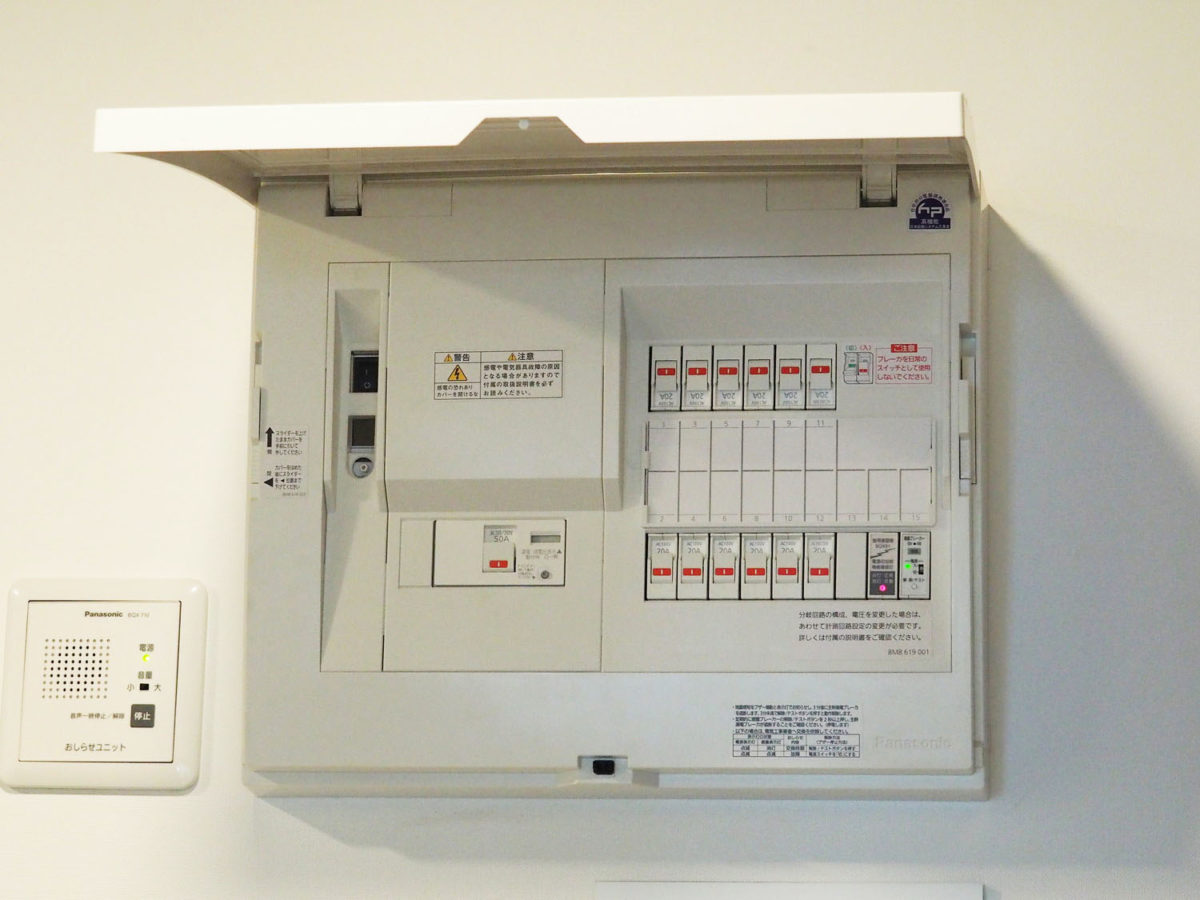
通常はなにかあったときしか目にしない分電盤ですが、実は時代とともに大きく進化しています。なかでも、一番わかりやすいのは「大きさ」。分電盤はそもそも目立たない場所の壁に設置されることが多いため、1990年代まではあまり大きさを問題にすることがなかったのですが、住宅の電化が進むとともに搭載されるブレーカーの数がどんどん増え、分電盤も巨大になりました。そこでパナソニックはブレーカー一個一個のサイズを従来の半分ほどに抑えた「コンパクトブレーカSH型」を開発しました。
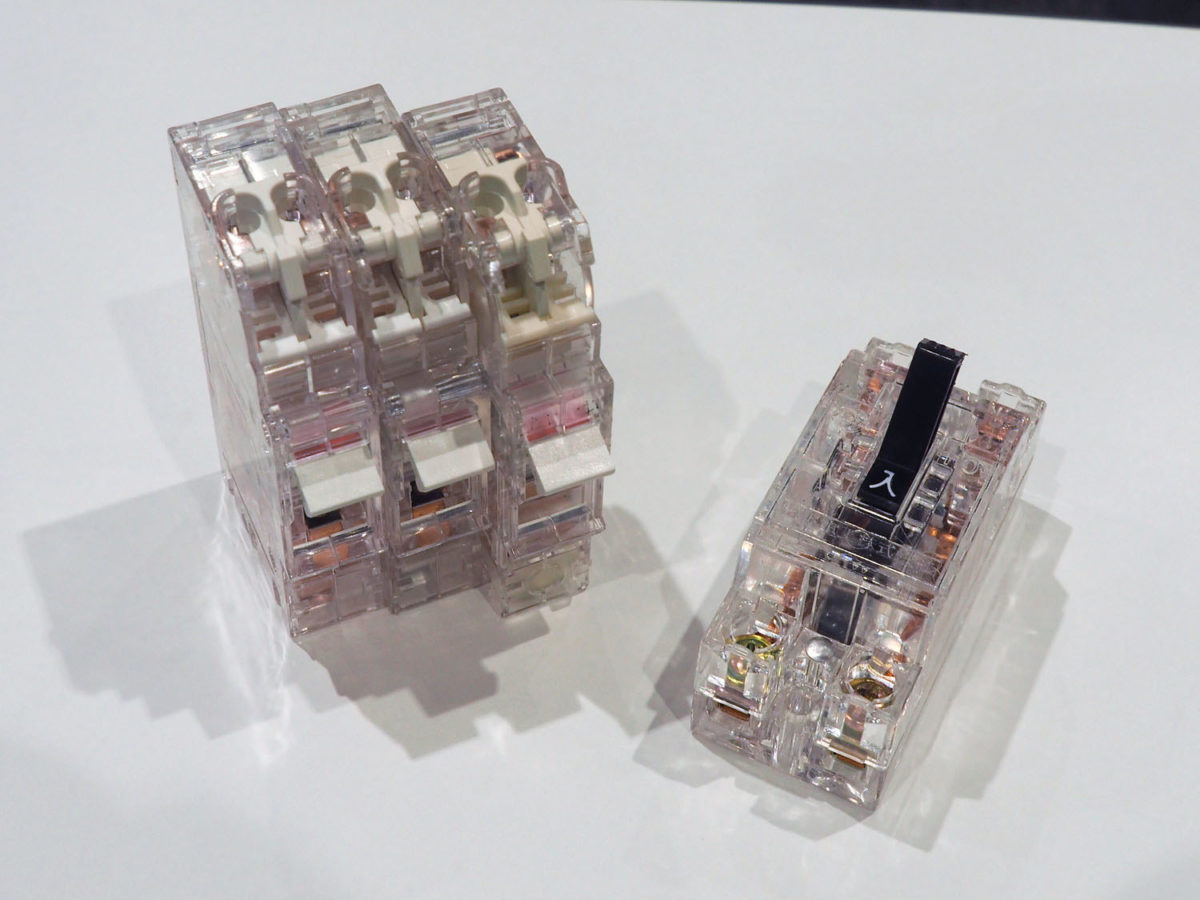
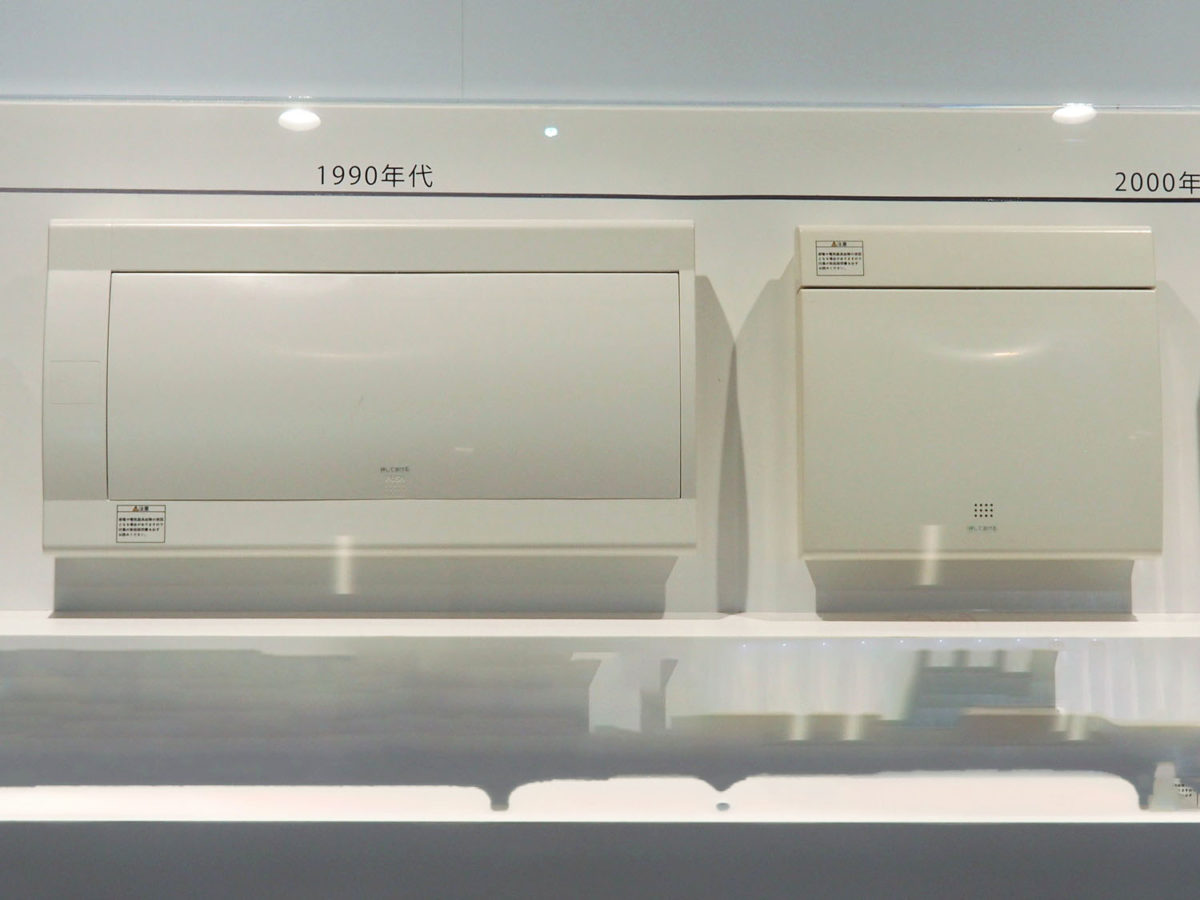
地震を感知すると電気を止めて火災を防ぐ「感震ブレーカー」
さらに、分電盤は時代とともに機能も追加されます。なかでも注目したいのが「感震ブレーカー」の存在。これは震度5以上の地震を感知すると電気をストップする機能です。大きな地震がくると保安のために一時的に地域全域が停電することがありますが、実は怖いのは電気の復旧後。地震時に倒れた電化製品などが原因で、電気復旧後の住民が避難している間に火災がおきることがあるのです。
このため、本来は避難前に住民がブレーカーを手動で切る必要があるのですが、いざというときにそのような余裕があるかどうかはわかりません。避難所で「ブレーカー落としたっけ? 家は大丈夫かな……」と不安にならないためにも、感震ブレーカーはかなり心強い味方です。しかも、パナソニックの感震ブレーカーは震度5の地震が発生してから3分後に電気が遮断される仕組み。このため、夜中の災害時でも電気の明かりのもと安全に逃げることができます。
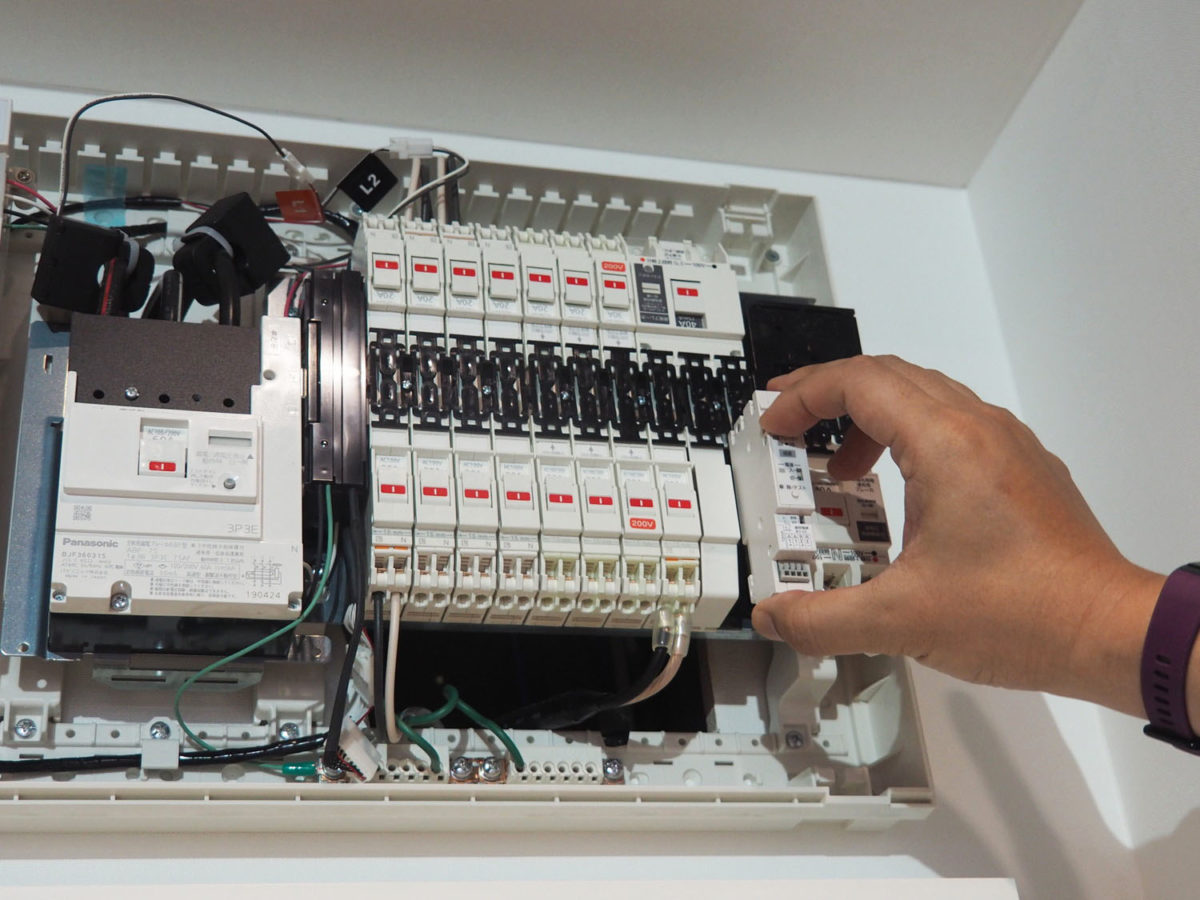
また、最新の分電盤はHEMS対応製品も増えています。HEMSとは「Home Energy Management System」のことで、家庭で使う電気などを管理するためのシステム。分電盤にHEMS対応製品を選ぶことで、回路ごとに使用する電気の「見える化」が可能。節電にも役立つほか、HEMS機器とつなげることで対応家電の自動制御なども可能です。
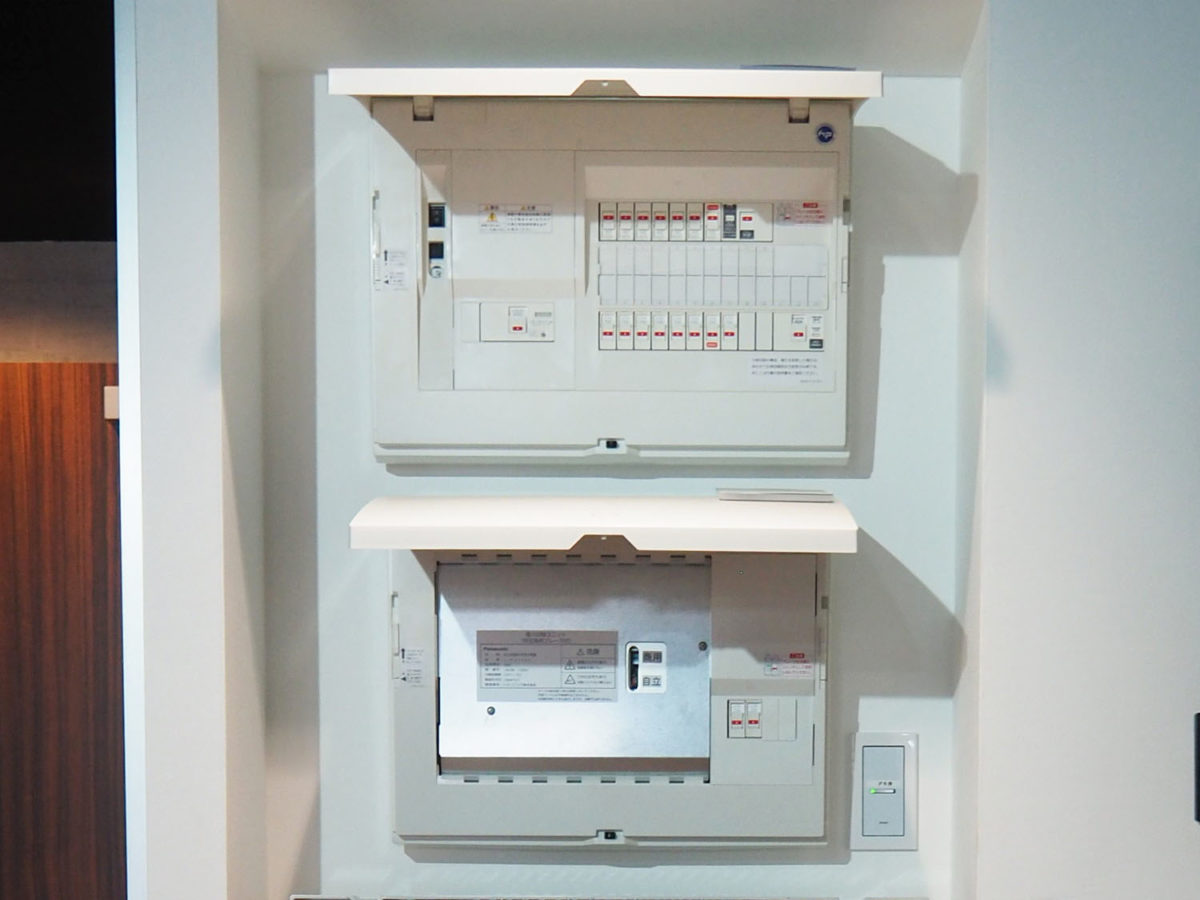
大量生産できるパーツは機械で完全自動生産
ひとくちに分電盤といっても、住宅によって必要とする機能は異なります。このため、パナソニック スイッチギアシステムズではなんと現在3万6000種類の分電盤を生産しているそう。これだけ種類があると一種類につき多くの在庫は抱えられません。そこで、同社がとっているのが「需要連動生産」という方式。これはあえて少量ずつの在庫を確保し、在庫が出荷された分だけ随時生産するという方式です。しかも、生産オーダーが入ってから完成品となり、在庫が補充されるまでの時間はなんと120分。分電盤という複雑な製品が、これだけ短時間でできるのは驚きです。
短時間で3万6000種類の分電盤を作り分ける秘密は、一貫自動化生産と人の手による組み立てを使い分けているところにあります。分電盤は住宅によってカスタマイズする必要がありますが、分電盤に配置されるブレーカーなどは仕様がほぼ統一されています。そこで、大量に生産できるパーツは機械による完全自動生産が行われているのです。機械による完全自動化によって、主力であるコンパクトブレーカーの生産スピードは一個につきわずか1.1秒!
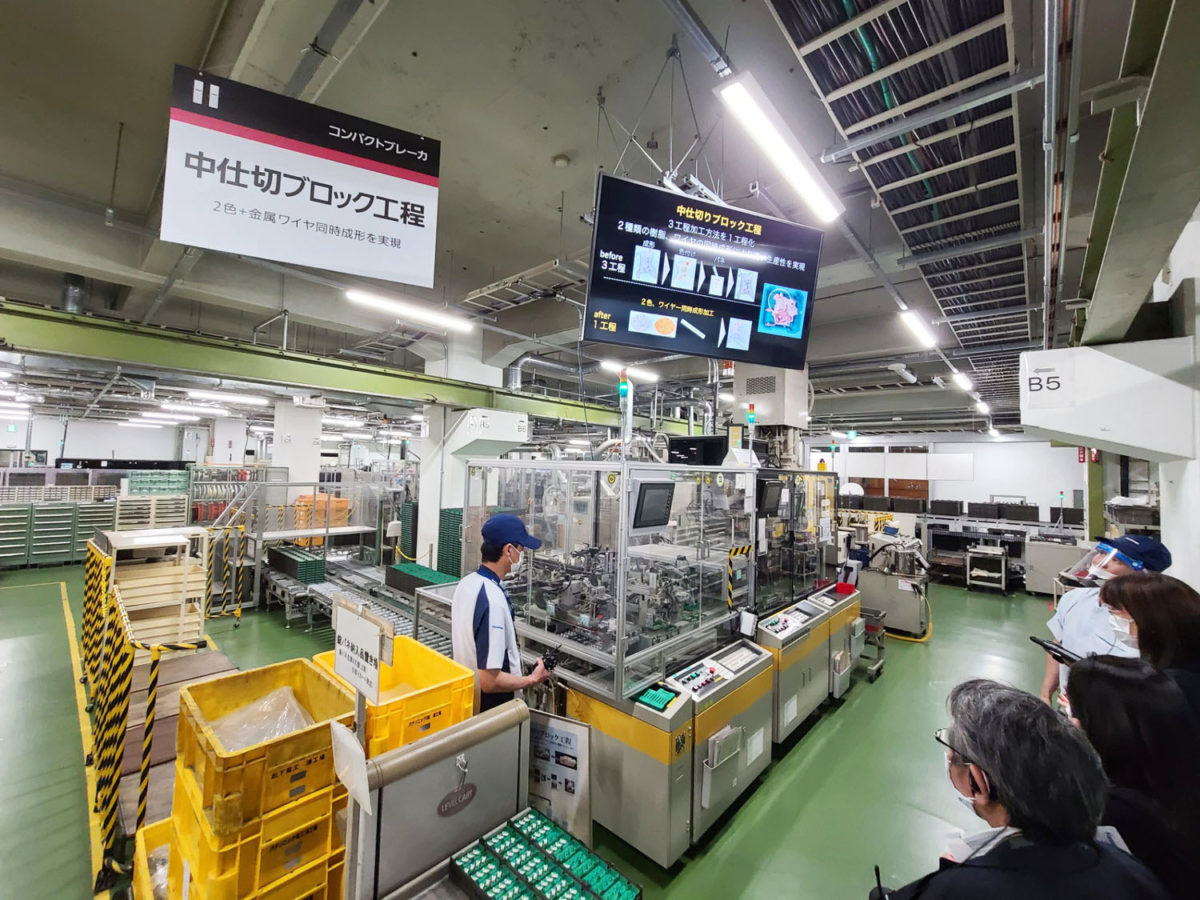
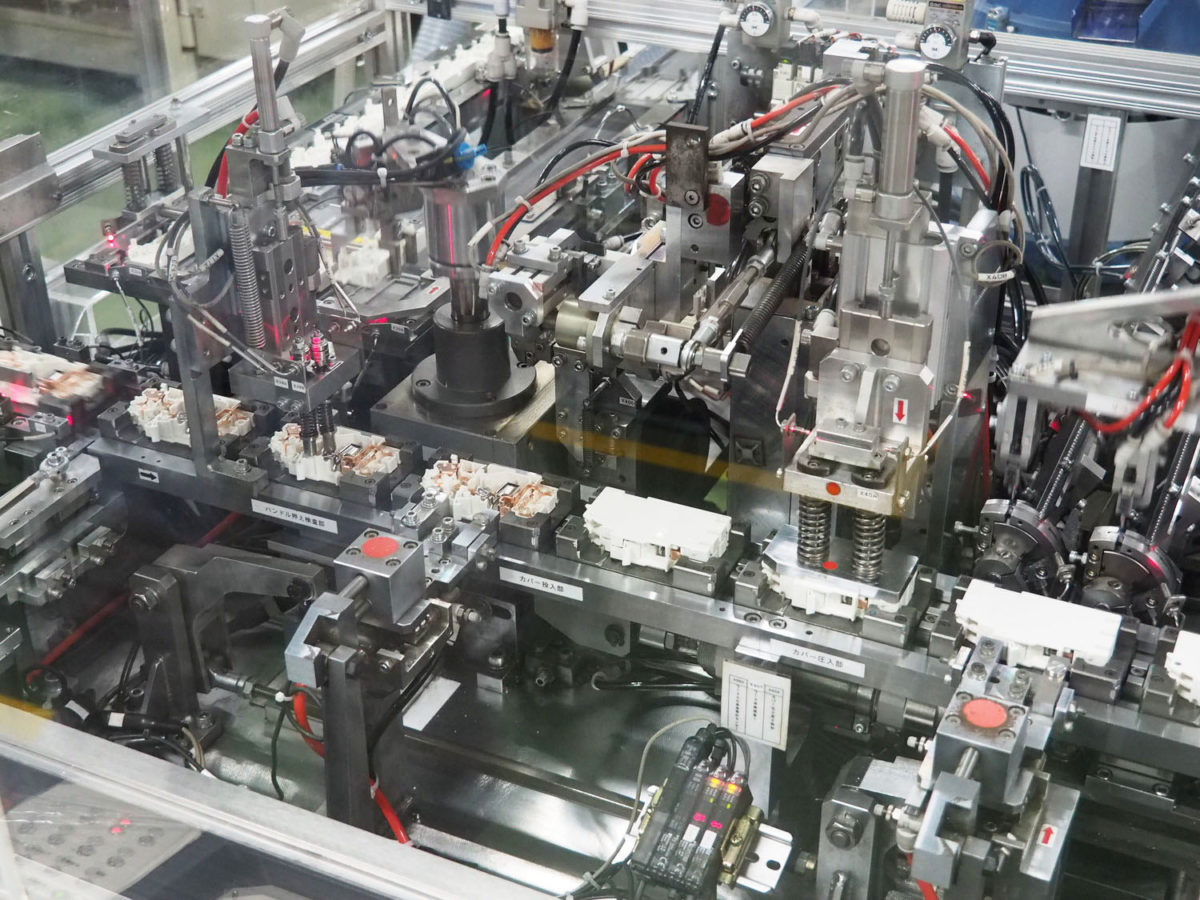
ブレーカー完成品はすべて「過電流に即時反応できるか」「規定範囲の絶縁耐力があるか」といったテストを受けます。この試験機もすべて自動化。人の手によるうっかりミスがないため、なんと歩留まり(素材の投入量に対し、実際に得られた生産数量の割合)は99.7%! つまり1000個の製品を作って不良品は3個しなか出ない計算です。
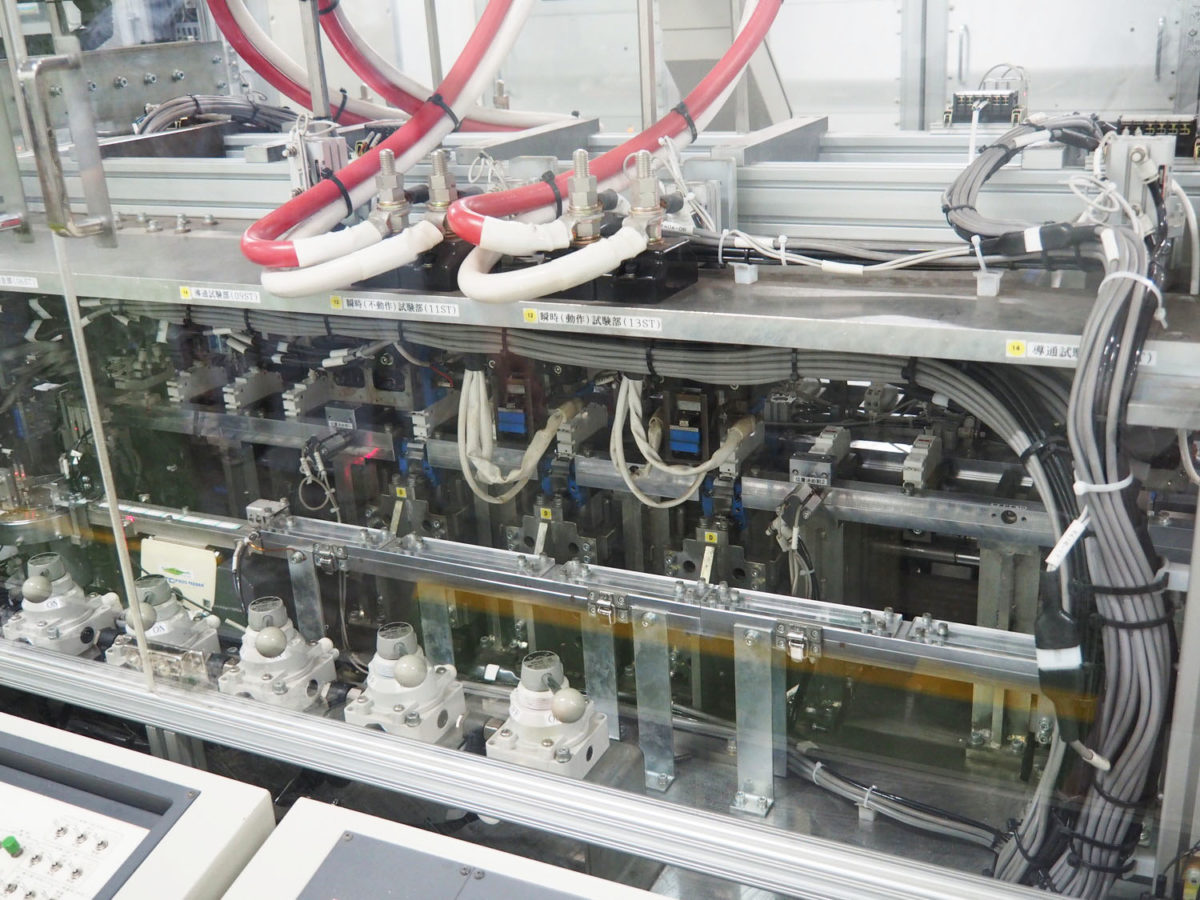
組み立てではヒューマンエラーを防ぐ仕組みを採用
さて、完成したブレーカーなどの部品は在庫としてストア(備蓄)されます。工場でストアされる部品は約2000種類。これらの部品の組み合わせにより、3万6000種類の分電盤が作り出される仕組みです。もちろん、これだけの種類があると部品のピック間違いや、組み立て手順の間違いなどのヒューマンエラーも発生しかねません。そこで、パナソニック スイッチギアシステムズでは組み立てる分電盤のデータをコンピュータで管理。作業員はタブレットで指示された部品をピックアップし、バーコードリーダーに通すことで部品のピック間違いを阻止。さらに、組み立て手順などの指示も製品ごとにタブレットでチェックできるようになっています。
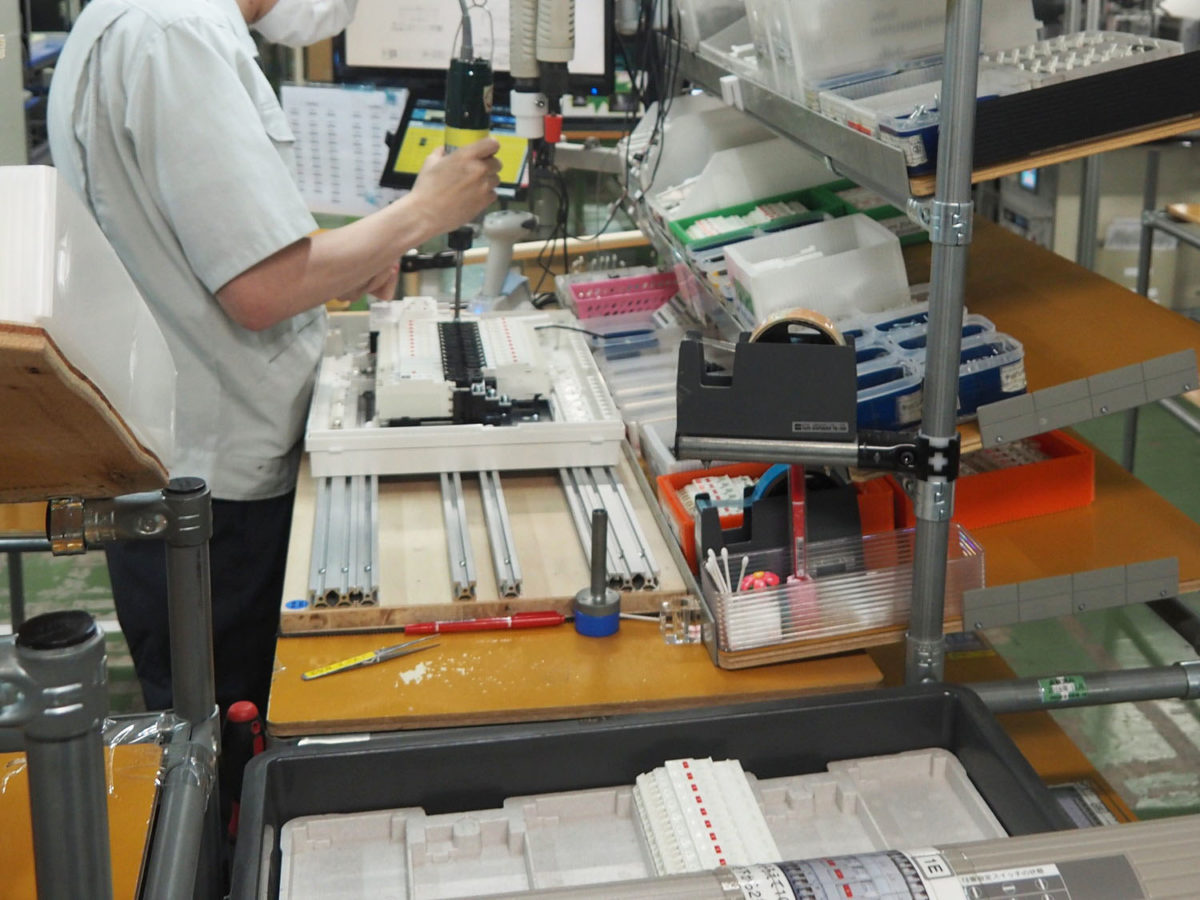
分電盤は家庭の安全を守る製品でもあるため、完成後のチェックにも抜かりはありません。組み立てた分電盤はひとつひとつカメラで撮影し、注文した通りの内容で組み立てられているかを機械が自動的に判断してくれます。さらに、ここで撮影したデータは一定期間保存されるので、万が一分電盤を設置したあとに問題が起きた場合はすぐに「組み立てた製品」の写真データを工場側がチェックできるようになっています。
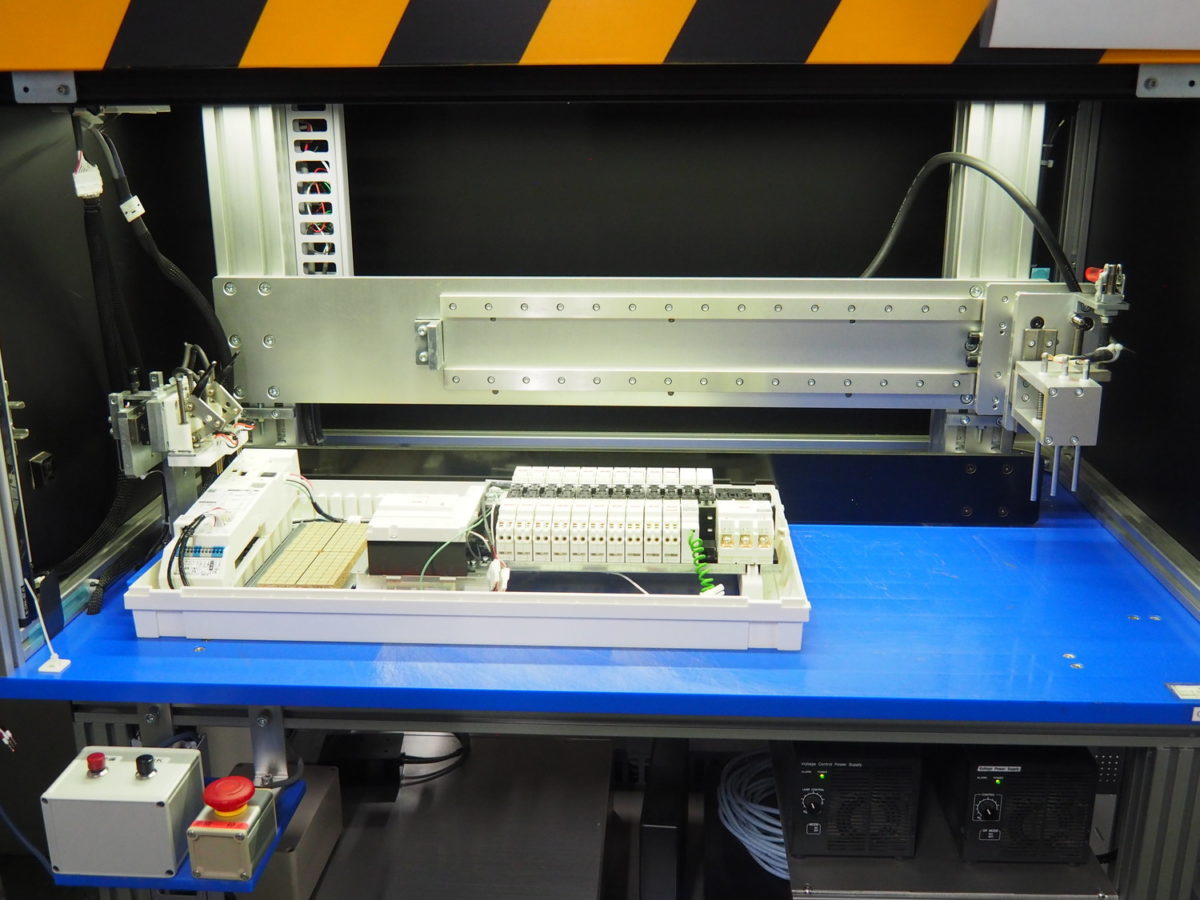
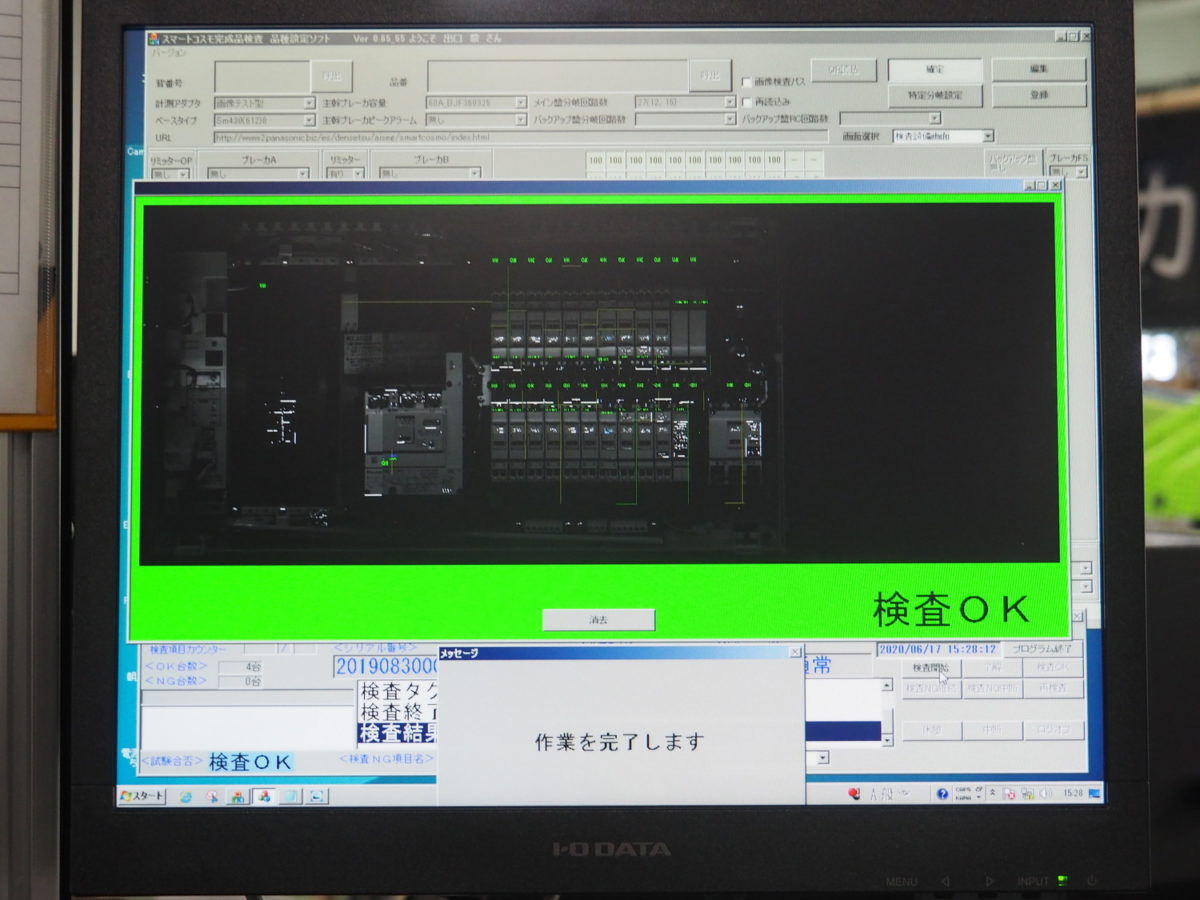
今回の工場見学で、普段あまり気にしたことのない分電盤の重要性がわかりました。しかし、社団法人 日本電機工業会(JEMA)の調査によると、実はこの家庭の安全に不可欠な分電盤の寿命はなんと13年ほどなのだそう。もちろん13年たったからといって、すぐに交換が必要という意味ではありませんが、15年以上大きなリフォームなどをしていない家なら一度チェックしてみるのも良いかもしれません。
【フォトギャラリー(画像をタップすると閲覧できます)】