新潟県新潟市に本社を持つ「ダイニチ工業」。その名前になじみの少ない方もいるかもしれませんが、実は石油ファンヒーターでは10年連続シェアNo.1、加湿器の分野でも4年連続シェアNo.1と、季節家電の分野では驚くべき実績を持つ会社なのです。前回は、同社のものづくりへのこだわりに迫っていきましたが、今回はその工場に潜入。同社がトップを走り続ける理由を、ものづくりの現場から探っていきましょう。
石油ファンヒーターの心臓部の製造ラインから見学スタート
ダイニチ工業北部工場は、本社と同じ敷地内に存在。同工場では石油ファンヒーターをはじめとする金属加工製品の製造が行われています。同社では、石油ファンヒーターの部品のうち、制御関係の基板や燃焼室、業務用ストーブのガード部の製造、メッキ作業などは協力工場に依頼。それらとボルト・ナット以外は、すべて自社工場で作っています。ちなみに、各パーツの「金型」も自社で製造。パーツを製造中に金型が欠損した場合、すぐに対応ができるよう、自社で金型を持つようにしているそうです。
まずは、同社の石油ファンヒーターの心臓部である「気化器」の製造・組み立てを行うエリアから見学。
同社の石油ファンヒーターは、「ブンゼン気化式」という燃焼方式を採用しています。これは、気化器に取り付けたセラミックヒーターで灯油を加熱・気化し、その後ノズルから気化ガスを噴射して燃焼させる方式で、火力の大小に関わらず安定した自立燃焼を行える点と、着火速度が速いのが特徴です。また、消火時にはノズルが閉じて素早く炎が消えるため、ニオイがしにくいというメリットもあります。
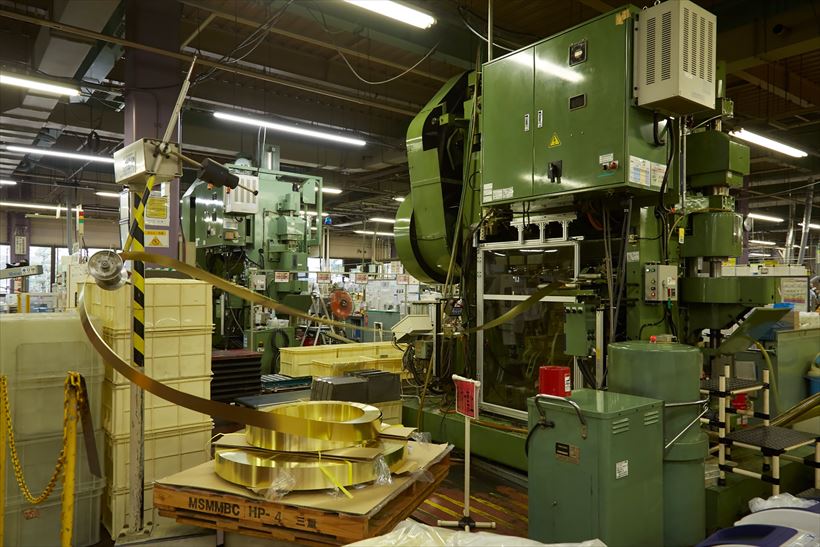
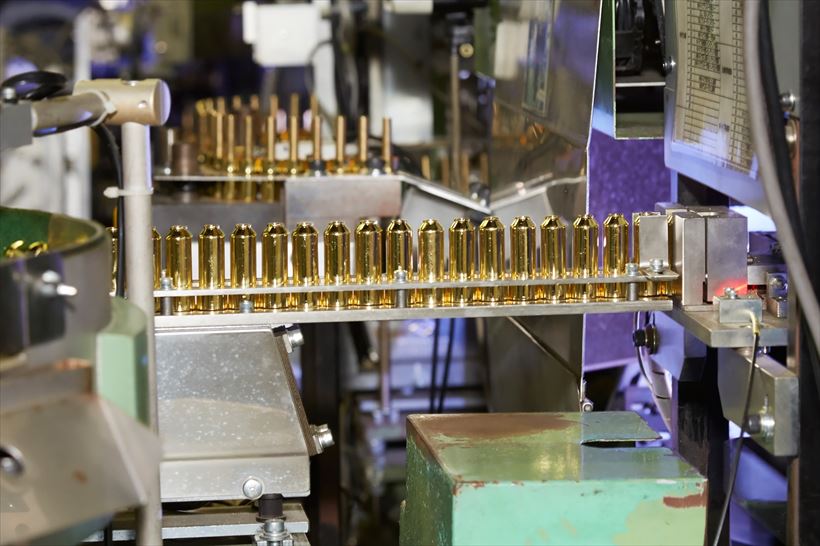
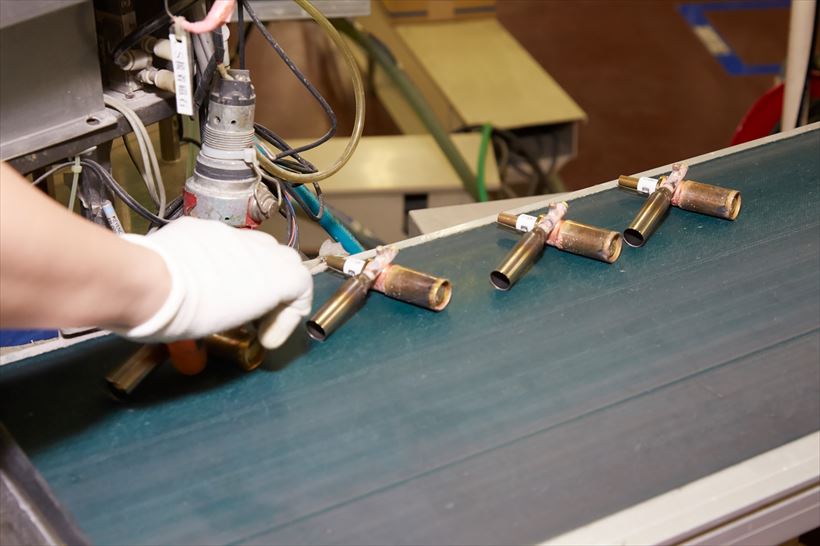
気化器の中には電気配線のパーツや温度センサー、プランジャー弁など様々な部品が入っています。これにより、素早い着火ときめ細かな運転制御が可能になります。
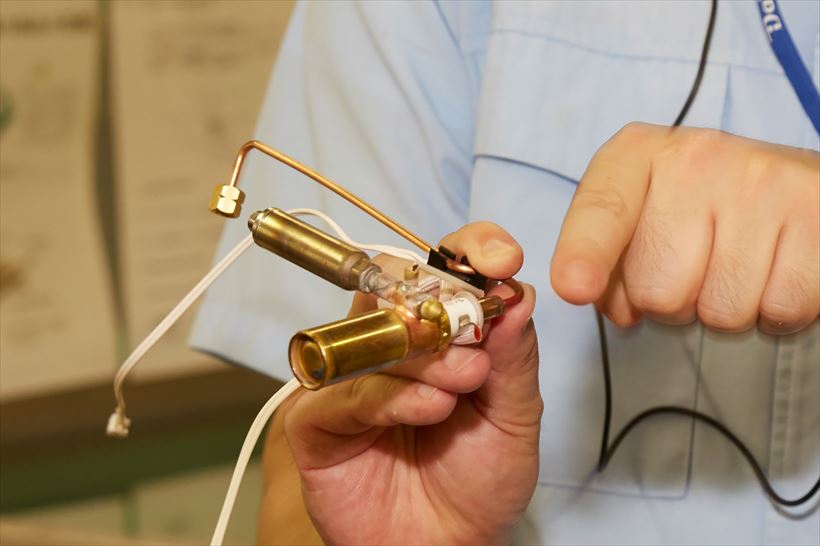
給油タンクや本体ボディはプレス機で一発成型
次に訪れたのは、給油タンクの加工が行われているエリア。鉄板を一気にプレスすると、給油タンクの形に成型。別のエリアではプロペラファンや天板、ボディもプレス成型します。
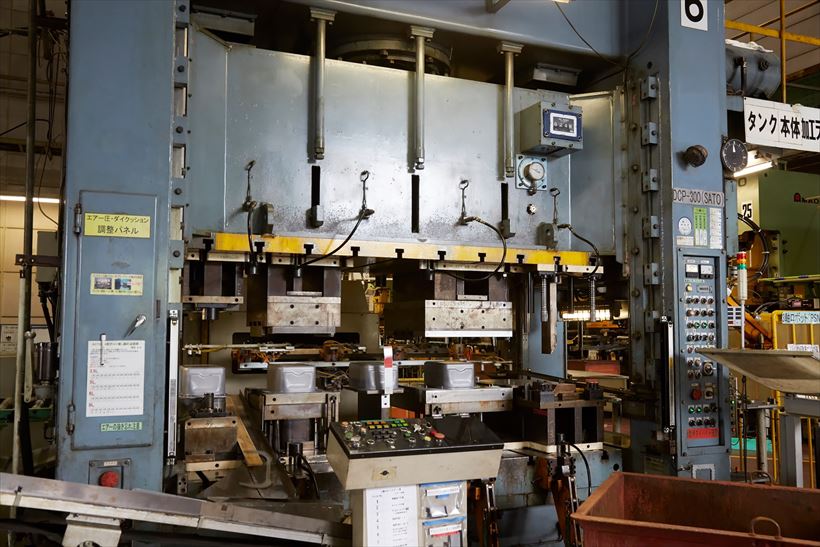
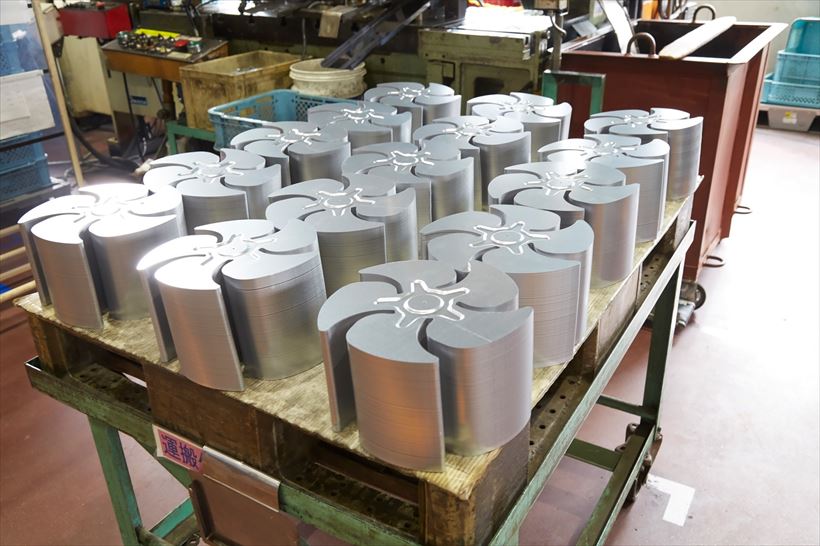
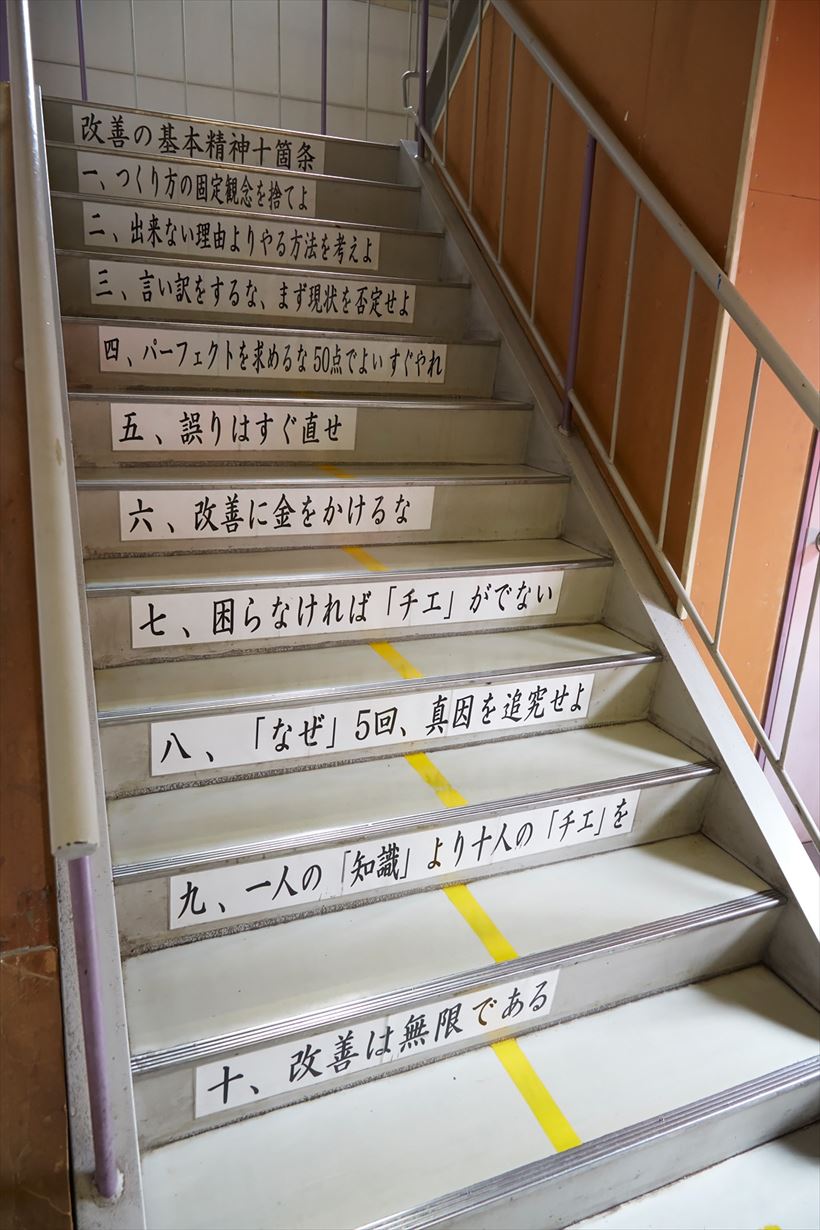
すべての製品を細かく検査しながら組み立て
階段を昇った2階では、ファンヒーター組み立てが行われます。入り口には、1階で成型され、その後オートメーションで塗装された本体ボディや天板などのパーツがラインに吊り下げられて運ばれてきます。
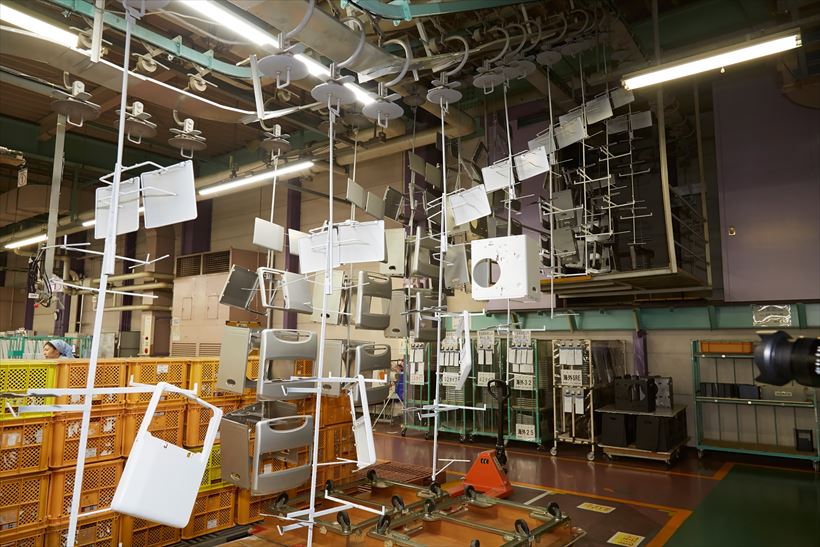
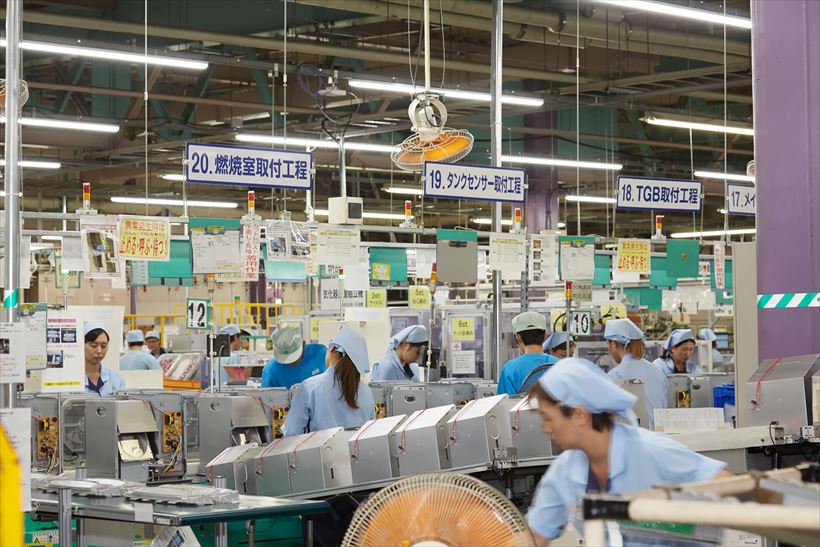
工場の要所要所で、工作用ロボットが活躍。ロボット導入は生産効率を上げるというより、働き手の身体への負担が大きい仕事を肩代わりさせる目的が大きいのだそうです。
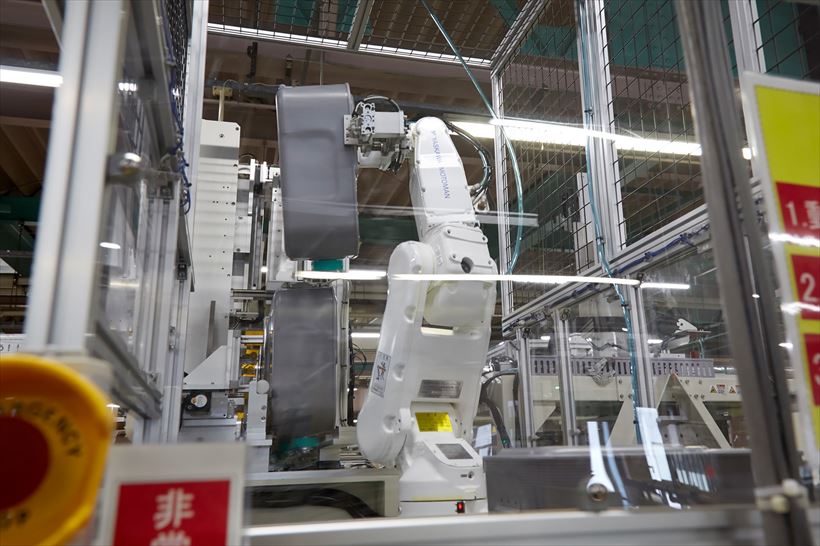
なお、石油ファンヒーターの品質検査は「抜き取り」でなく、100%の「全数検査」を行っていて、各検査に合格したものだけが次の工程に進みます。組み立て工程の途中には、100項目以上の検査が行われます。例えば、組み立てたタンクの検査では、油が漏れないか、穴が空いてないかをチェック。髪の毛1本挟まっているだけで、検査に通らないそうです。燃焼試験は、青い炎で燃えているか目で確認し、安全装置がきちんと作動しているかチェックします。
実際の住宅から-20℃の環境まで様々な状況で製品をチェック
続いて、開発棟にあるいくつかの試験室も見学させていただきました。
ここは「恒温恒湿装置」の入った試験室で、室内を-25℃~60℃に設定できます。ここでは、低温環境でモーターが正常に動くか、製品がちゃんと着火して使えるかをチェックします。またこの部屋は、温度と湿度を一定に保ちながら、換気を行えるのも特徴。室内での燃焼試験にはこの機能が不可欠です。
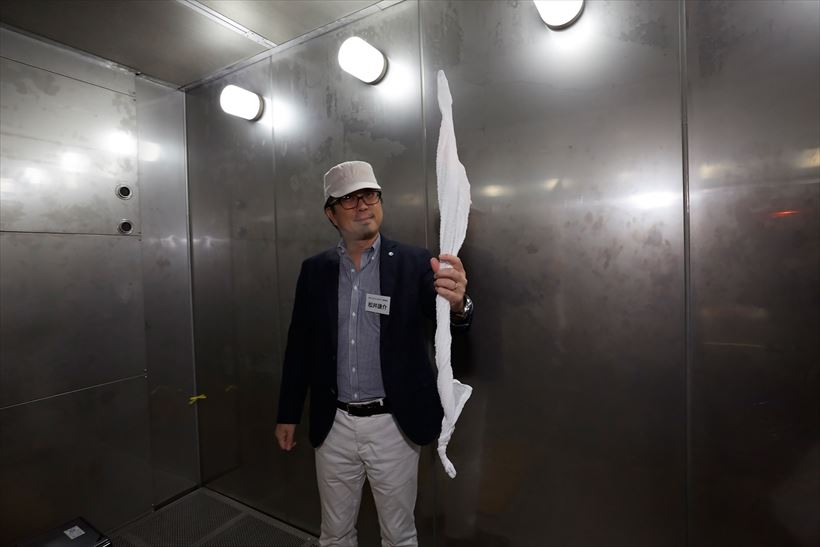
今回は、-20℃での石油ファンヒーターの着火試験が行われました。通常の環境では40秒で着火する同社のファンヒーターですが、気温-20℃の状態だとどうなるのでしょうか?
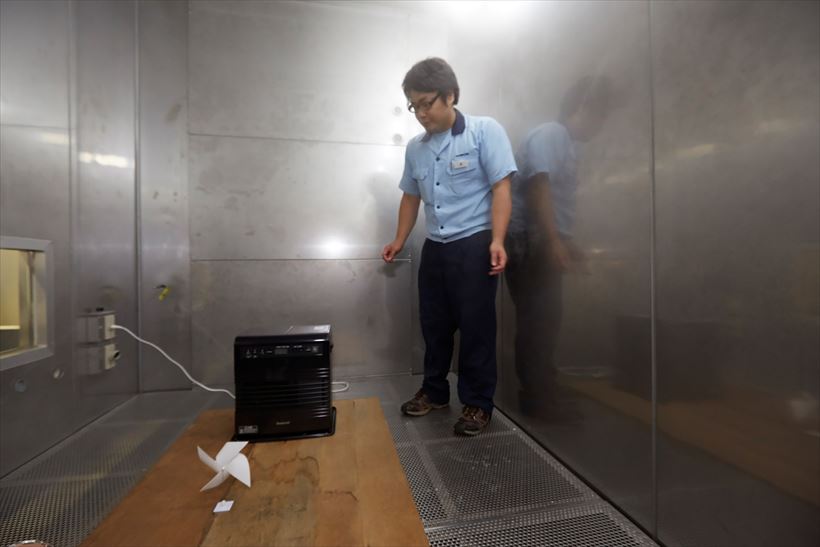

ちなみにJIS規格(日本工業規格)では、石油ファンヒーターは-20℃の環境でも正常に点火して、モーターが動かなくてはならないという規定があるとか。また、同条件で電気関係の動作もクリアしなければならないそうです。
続いて「環境試験室」を見学しました。ここでは、実際の住宅の一室を再現。中には8畳と6畳の木造の部屋があり、暖房時の室内温度分布の測定などを行います。例えば室外を-5℃、室内を5℃などに設定し、部屋が何分で暖まるか、温度分布はどうなるか、エアコンと兼用したらどうなるか、などをチェックします。
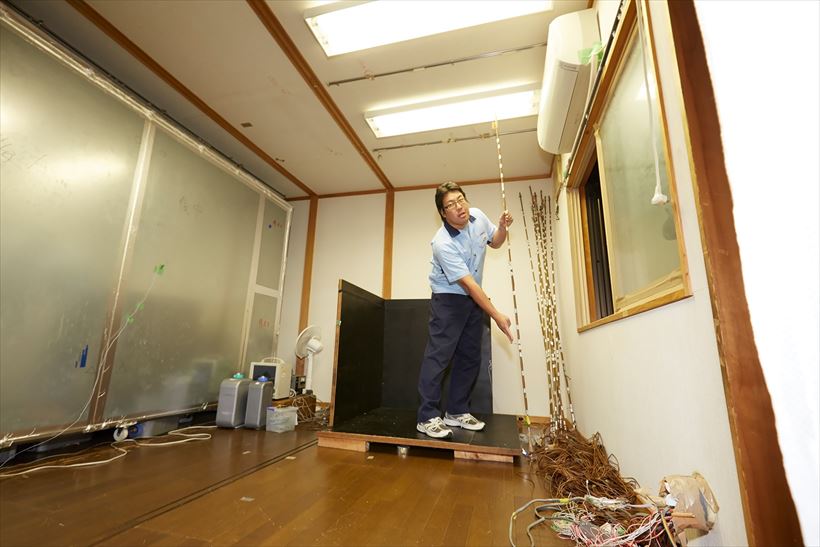
この日は室内に分厚い鉄板でできた部屋が作られていました。鉄板で密閉空間を作り、CO2濃度が上がったときに自動で消火するかのチェックを実施。海外への輸出にはこうした審査が不可欠。審査の基準は国ごとに違い、日本はCOの値に敏感ですが、フランスはCO2で、アメリカはNOX(窒素酸化物)で判断するという違いがあるそうです。
反射音のまったくない「無響室」で純粋な「運転音」のみを計測・算出
「無響室」では、運転音の試験を行います。今回は「静音性」を売りにする加湿器について、そのdB(デシベル)値を測定していました。
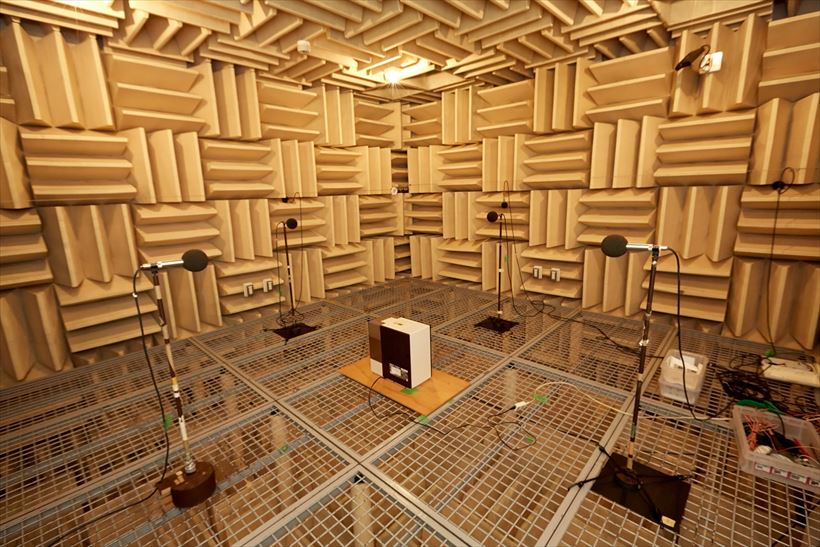
室内には壁や天井、金網の下の床部分にまで、くさび形の吸音体を設置。この吸音体は低い周波数帯まで吸収でき、高い吸音性能を発揮します。部屋の真ん中に同社の加湿器が設置され、その周りに4台のマイクが置かれています。
これだけ高い吸音設備を施していても、マイクにはノイズが入ります。その正体は、屋外から室内に入り込む自動車などの音。何も音を立てなくても、これだけで13dBの音量になるそうです(これを「暗騒音」といいます)。ちなみに休日は静かなので、暗騒音は5dBに。深夜はもっと静かになるとのこと。
騒音のチェックは室外に設置した騒音計で行います。ここで計測した音量から暗騒音の補正を行って、加湿器の運転時の音量を割り出します。これがカタログに載っている「運転音」の値です。
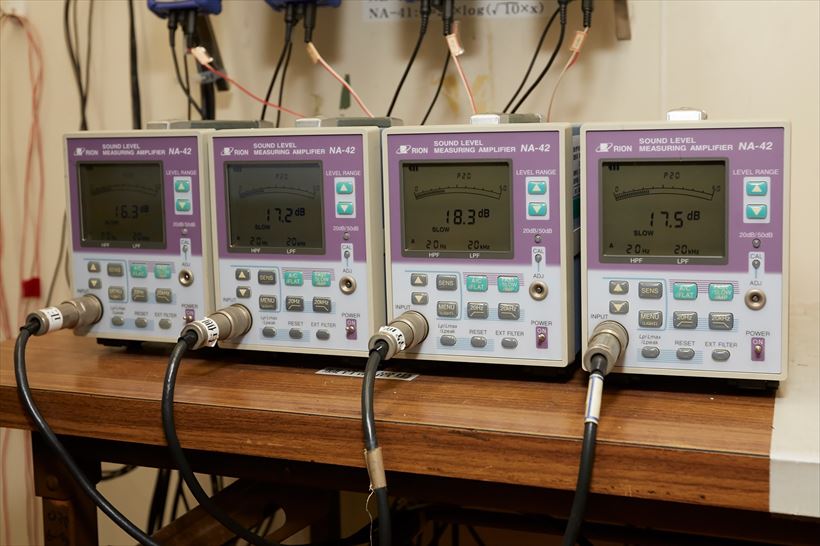
各モニターには16.3dB~18.3dBと表示されています。これを暗騒音補正すると約13dBとなり、同製品の最小運転音のカタログ値と一致。人が耳で聞き取れる最小の音量は10dBだそうで、この加湿器がいかに高い静音性を持っているかがよくわかります。
ちなみに、同社の加湿器の最上位機種である「RXシリーズ」の運転音はターボモードで最大40dB。同社製品には、運転音に含まれる耳障りな周波数帯をカットする機構も施されており、実際の聴感はカタログでの数値より静かだといいます。
通年で生産する方式に働く人を大切にする姿勢を見た
ダイニチ工業では、北部工場を含む2つの工場で約500人が働いていますが、驚くのはそのほとんどが正規社員であること。パートや非正規の社員は数人しかいないのだそうです。
同社は、冬の季節商品である石油ファンヒーターや加湿器を1年通して生産しています。メーカーの多くは在庫を圧縮するため、「必要なとき必要なだけ作る」という生産管理方式を採用していますが、同社は「そのやり方だと、1年のある時期だけ、多くの人員と設備が必要になってしまうのが良くない」との考え方を取っています。生産台数を通年で平均して作れば、最も少ない人数と設備で年間需要を賄えるというわけです。また、これにより社員と協力工場に安定した仕事を生み出せるのもメリットだとか。
需要と価格がある程度安定していて、生産計画が組みやすい商品だからこそ可能な生産方式ですが、こんなところにも地域に根差し、働く人を大切にする同社の姿勢がよく表れています。
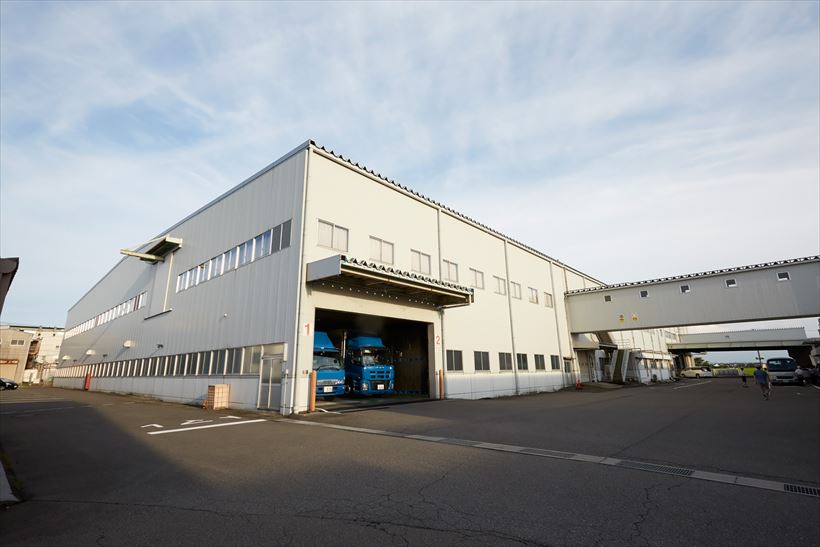
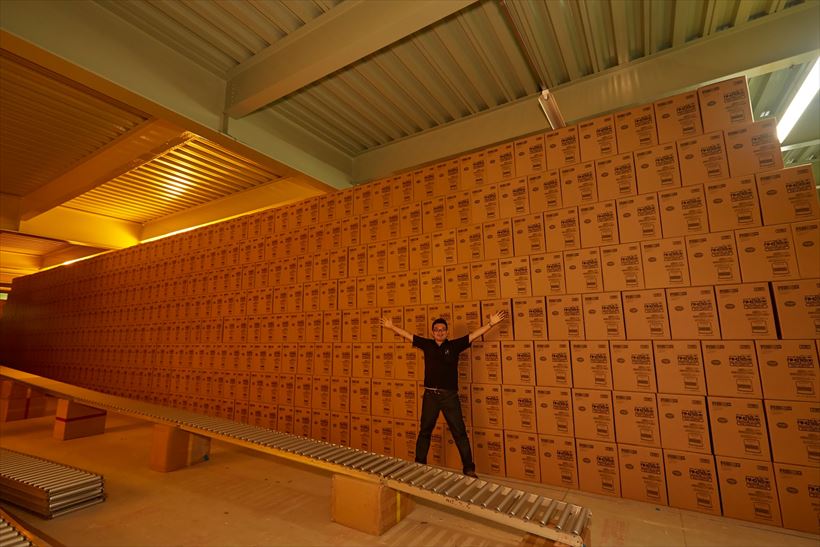
こうして見ると、ダイニチ製品のひとつひとつが、徹底した自社生産体制と厳しい品質管理によって完成しているのがわかりますね。今回の取材を通し、改めて同社製品への信頼感が増した印象です。「次の展開も考えている」という同社が、果たして今後どんな新商品をユーザーに届けてくれるのか。今後も楽しみに見守っていきましょう。
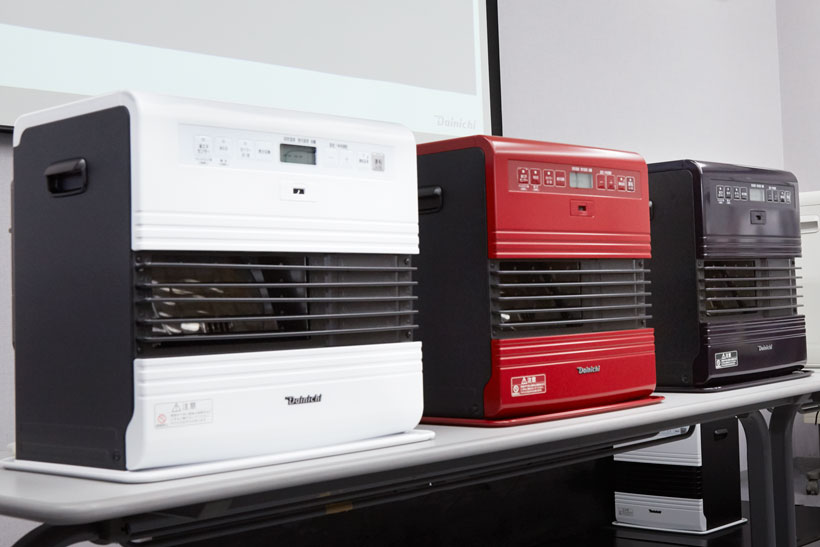