みなさんは「リトレッドタイヤ」ってご存知ですか? タイヤは使っているうちに摩耗し、スリップサインが出たら交換。そして廃棄されるというのが一般的ですよね。日本自動車タイヤ協会によれば、こうして生み出された廃タイヤは年間8300万本、廃車に伴う廃タイヤを含めると9700万本にも達するそうです。廃タイヤはチップにするなどしてリサイクル率が9割を超えている(出展:トーヨータイヤHP)と言われますが、新たな活用法として登場したのがリトレッドタイヤなのです。
※記事初出時、廃タイヤがすべてそのまま捨てられているという誤解を招く、というご意見をいただき、リサイクル率に関する一文を追記しました(2018年8月27日)
名前の由来は次のとおり。タイヤが路面に設置する面を“トレッド(Tread)”と呼びますが、これに“リ(Re)”を付けたもの。つまり、タイヤとしての機能を復元して再利用(リユース)するタイヤのことなのです。そのため、別名「更生タイヤ」とも呼ばれています。
リトレッドタイヤを早くから利用していたのは飛行機です。飛行機が着陸する際の速度は270km/h近いと言われ、数十トンもの機体をタイヤが一手に受け止めて停止させます。このとき、タイヤは機体の速度に一致するまでスリップすることとなり、摩擦によって白煙が上がるわけです。
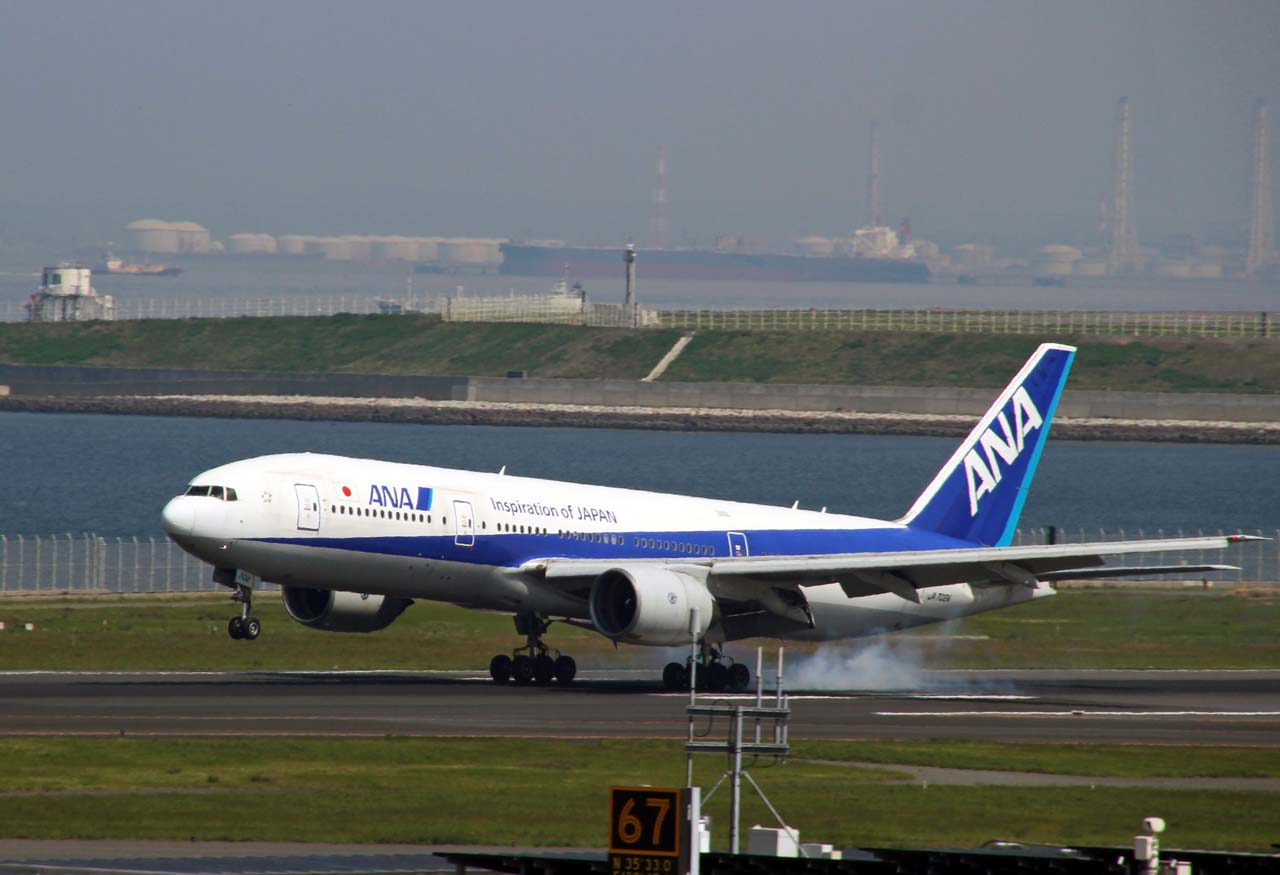
当然ながらこのとき、タイヤは激しく摩耗しますが、その耐用回数は約500回! とはいえ、いずれは耐用回数に到達します。かといって、そのたびにタイヤを廃棄していたのでは環境にも悪影響を与えることになります。そこで、交換時期がきたらリトレッドタイヤとして再利用することが考えられたわけです。
ではリトレッドタイヤはどうやって作られるのでしょうか。そんな疑問を持っていた矢先、日本ミシュランタイヤのトラックやバスなど商用車向けリトレッドタイヤを製造している現場を見学できる貴重な機会を得ました。場所は新潟県糸魚川市。ここでは日本ミシュランタイヤの顧客が使用済みとしたタイヤを回収して、リトレッドタイヤとして再利用しています。これによって新品を新たに購入するよりもコストも下がって環境にも優しい、そんなリユースの流れを作り出そうと取り組んでいるのがこの工場なのです。
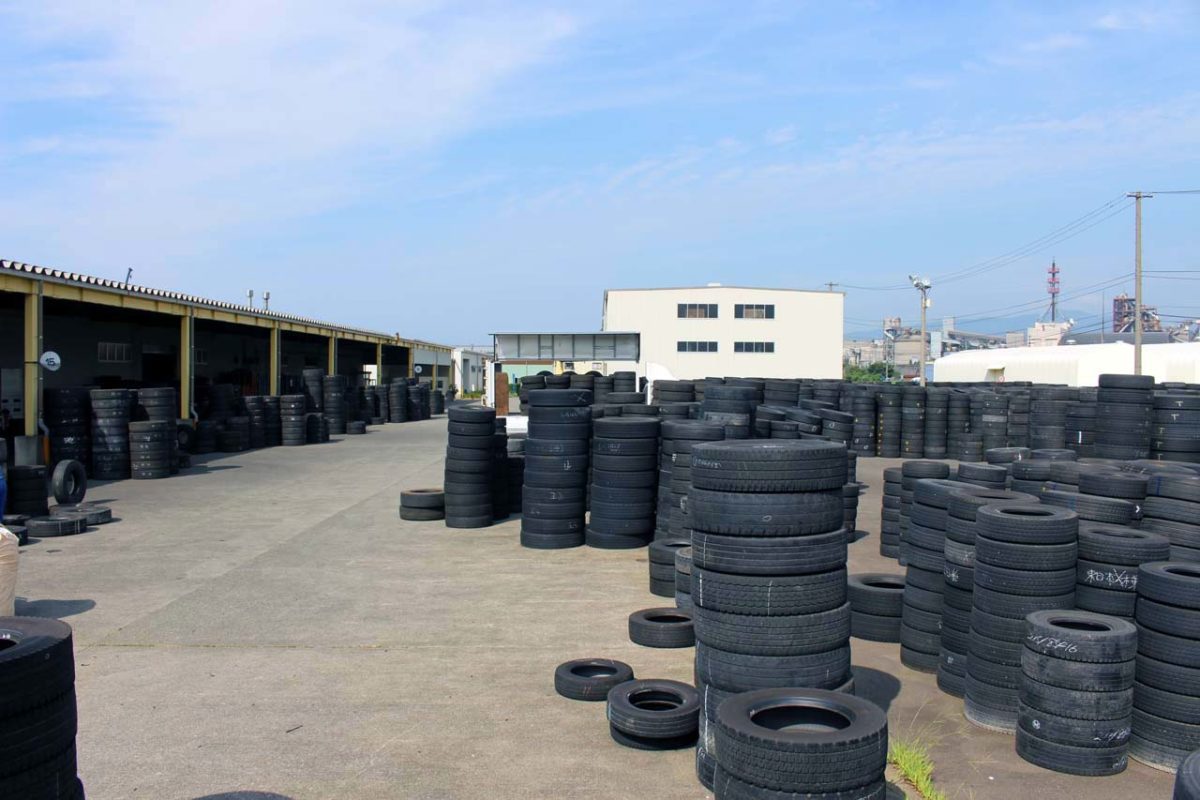
タイヤを再利用するうえで日本ミシュランタイヤが柱としているのが「ミシュラン3R」コンセプトです。「Reduce(リデュース)」「Reuse(リユース)」「Recycle(リサイクル)」の頭文字を取ったもので、「リデュース」はロングライフ性能の向上でタイヤの負担を軽減し、「リユース」で摩耗したタイヤの溝を掘り直して寿命を延ばしつつ安全性を向上させます。さらに「リサイクル」となるのがタイヤにトレッドを貼り直して再利用する(リトレッド)となるわけです。
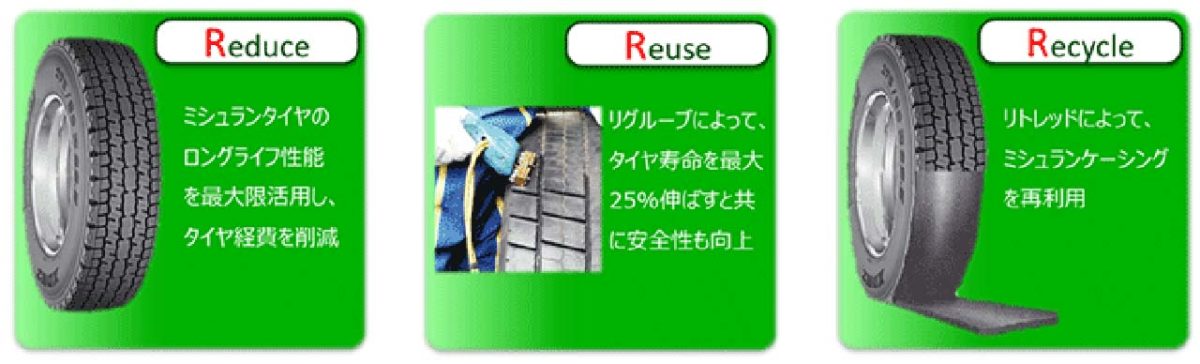
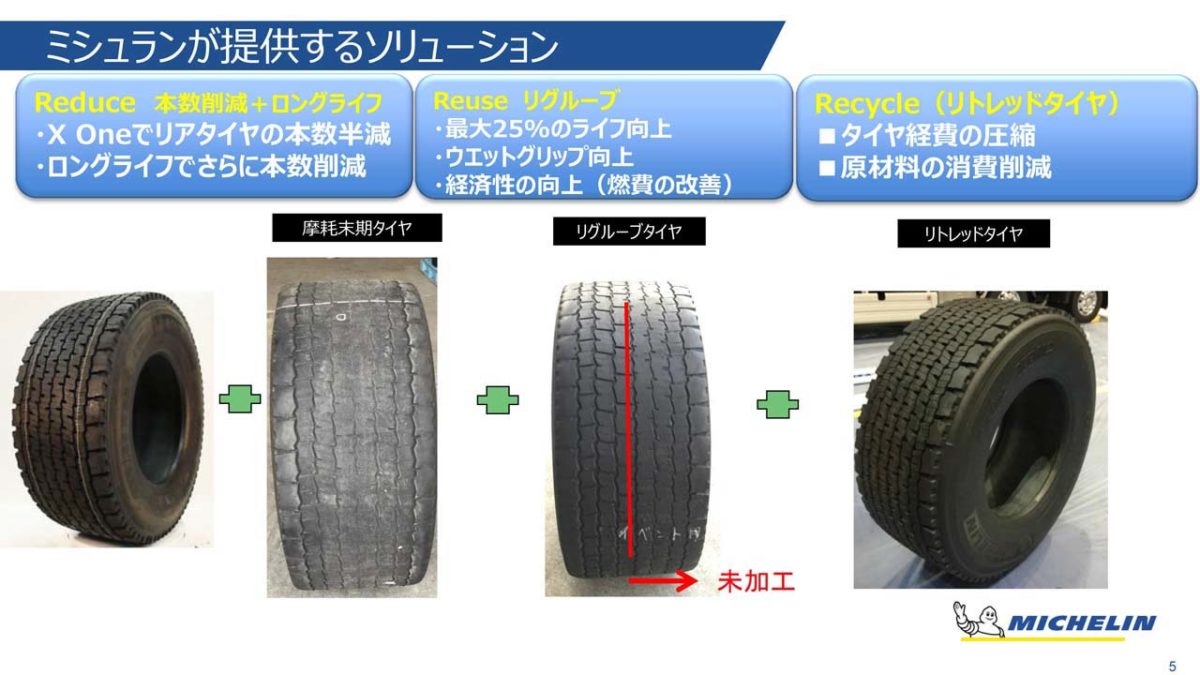
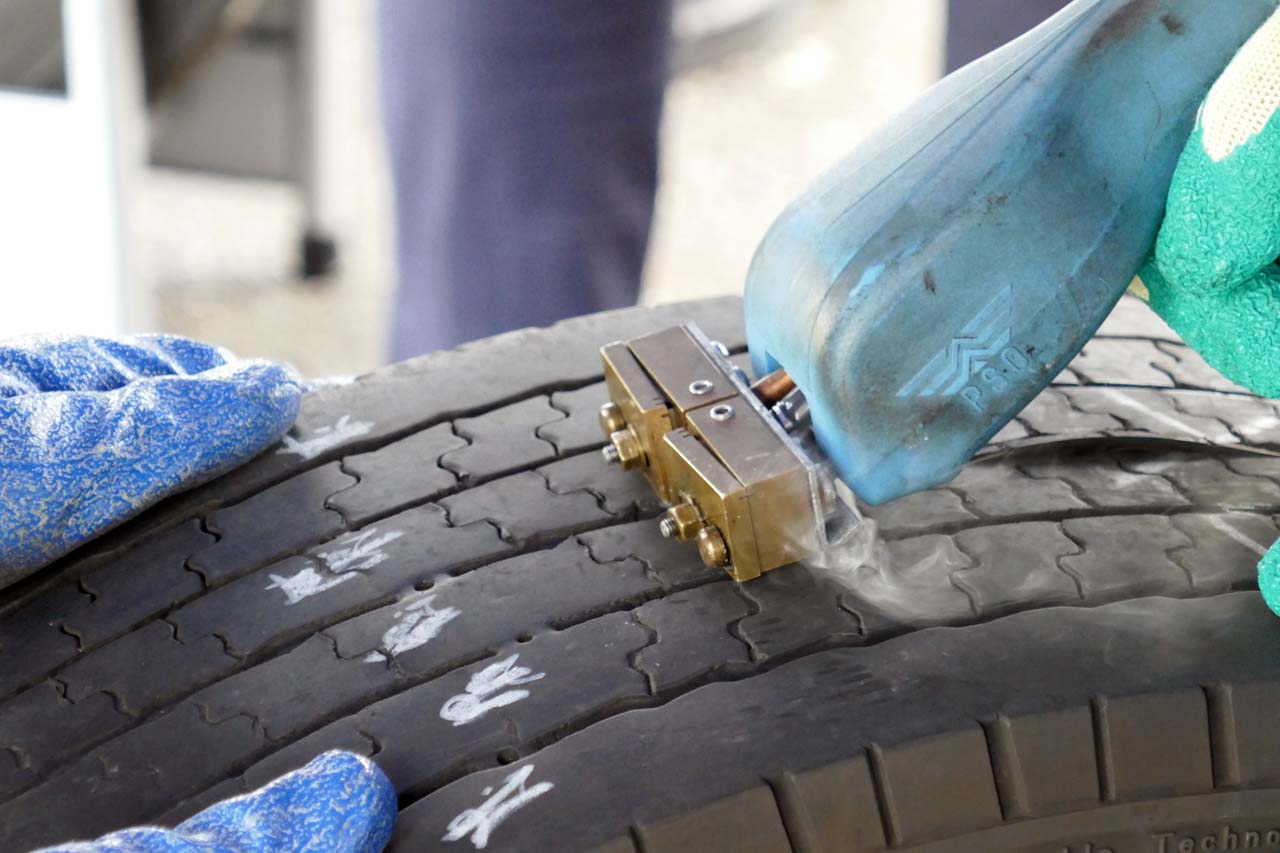
日本ミシュランタイヤが商用車向けに提供しているタイヤは、あらかじめこの再利用を前提とした造りとなっており、そのためトレッド面は摩耗したトレッド面を削れるだけの厚みが与えられている構造となっています。日本ミシュランタイヤのリトレッドタイヤはこの段階からスタートしているのです。
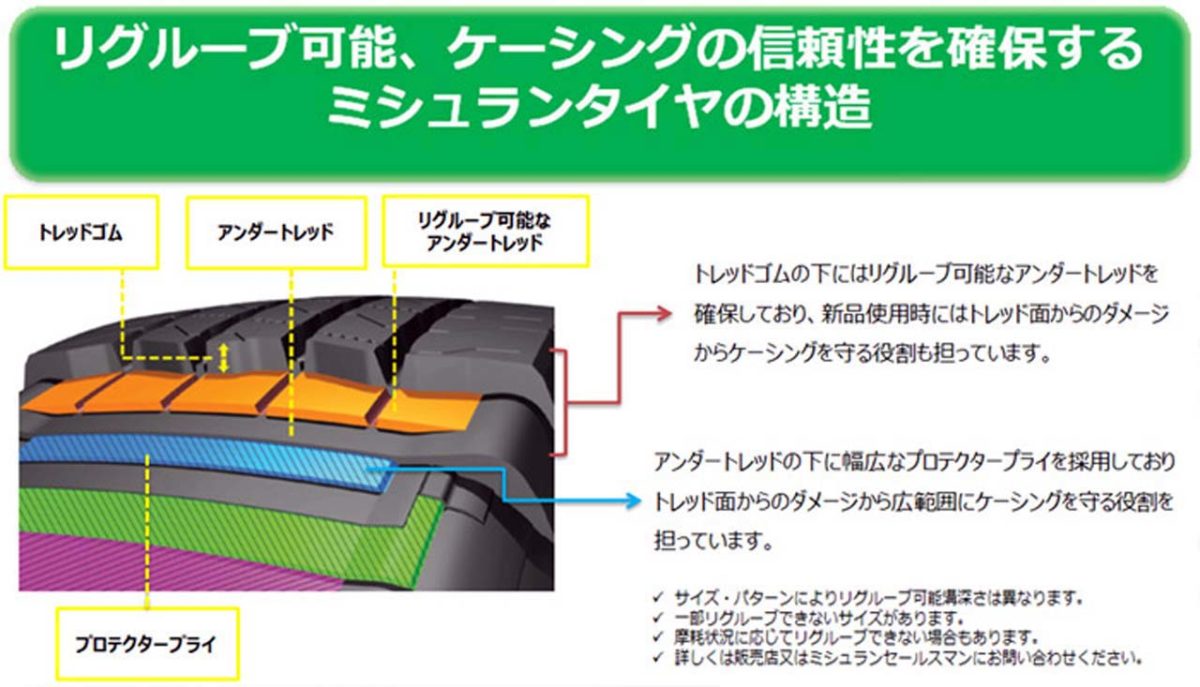
リトレッドタイヤはいかにしてできる? 生産工程をチェック【動画アリ】
工場を訪れてまず目にするのが山となった使用済みタイヤです。そのタイヤはまずしっかりと洗浄され、そのうえで超音波ウルトラソニックを使うシアログラフィ検査機にかけて部材の剥離がないかをチェック。さらにこの検査機によって通ったものをベテランの検査員が目と触診でもう一度チェックします。以前はこの目視だけだったとのことですが、シアログラフィの導入により「検索漏れは大幅に減った」(日本ミシュラン)と言います。
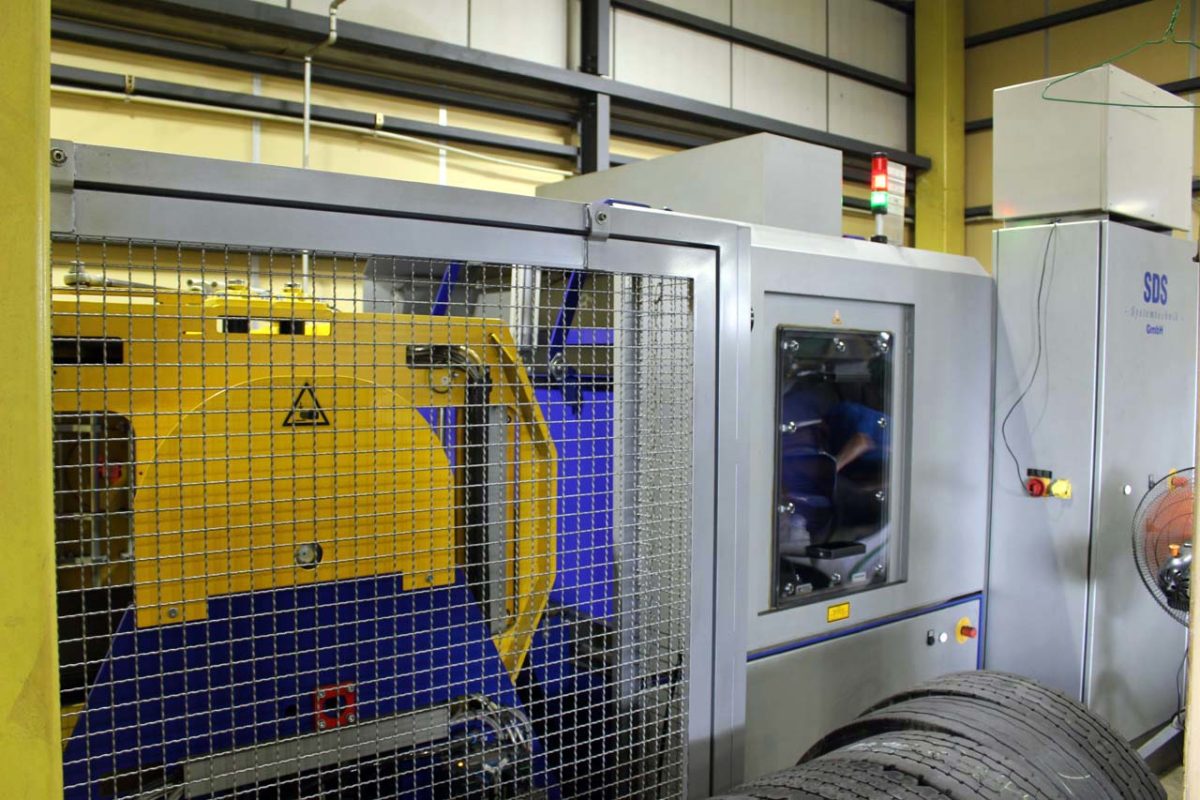
意外だったのは工程のなかで想像以上に人の手が介在していたことでした。工場のなかには工程ごとに必ずと言っていいほど担当者が割り振られ、相当な暑さ(この日は外気温が32度にもなっていた)のなか、黙々と作業が進められていたのです。ここまで人の手を経ていた理由について日本ミシュランは、「コストはかかるものの、日本ミシュランタイヤでは多品種少量生産を基本としており、その目的を達成するには人手を介在するほうが効率が良い」とのことでした。
検査工程を終えるとタイヤは次に「バフがけ」の工程に入ります。ここでタイヤはトレッド面をサイズ/パターンに応じて設定値まで削り、続いて損傷部分を整えるスカイプ工程へと移されます。貫通した傷があった場合は、それを埋めたり、パッチを貼って修理も実施。そして、削ったゴム面が酸化しないように加硫用セメントを塗られると、トレッドを貼り付けるケーシングの下準備が整うわけです。
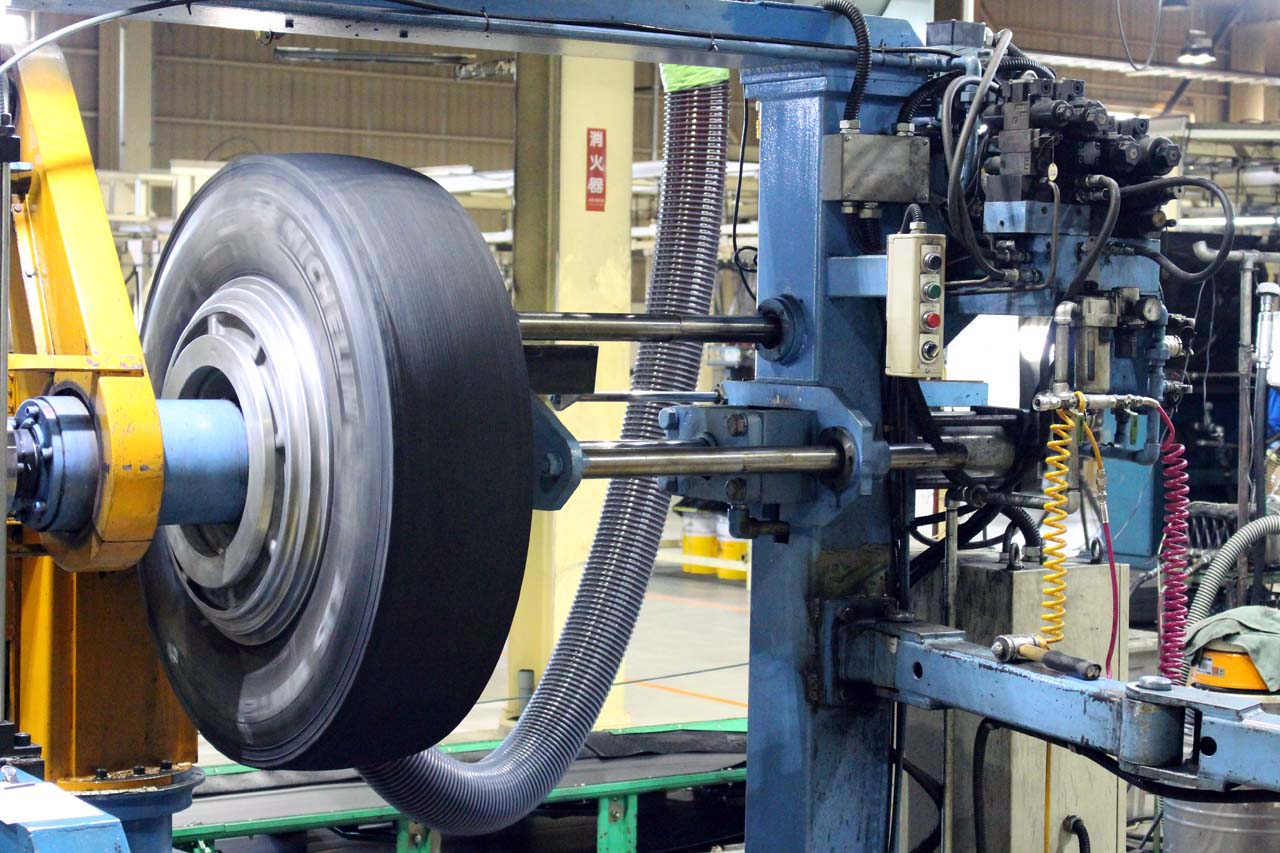
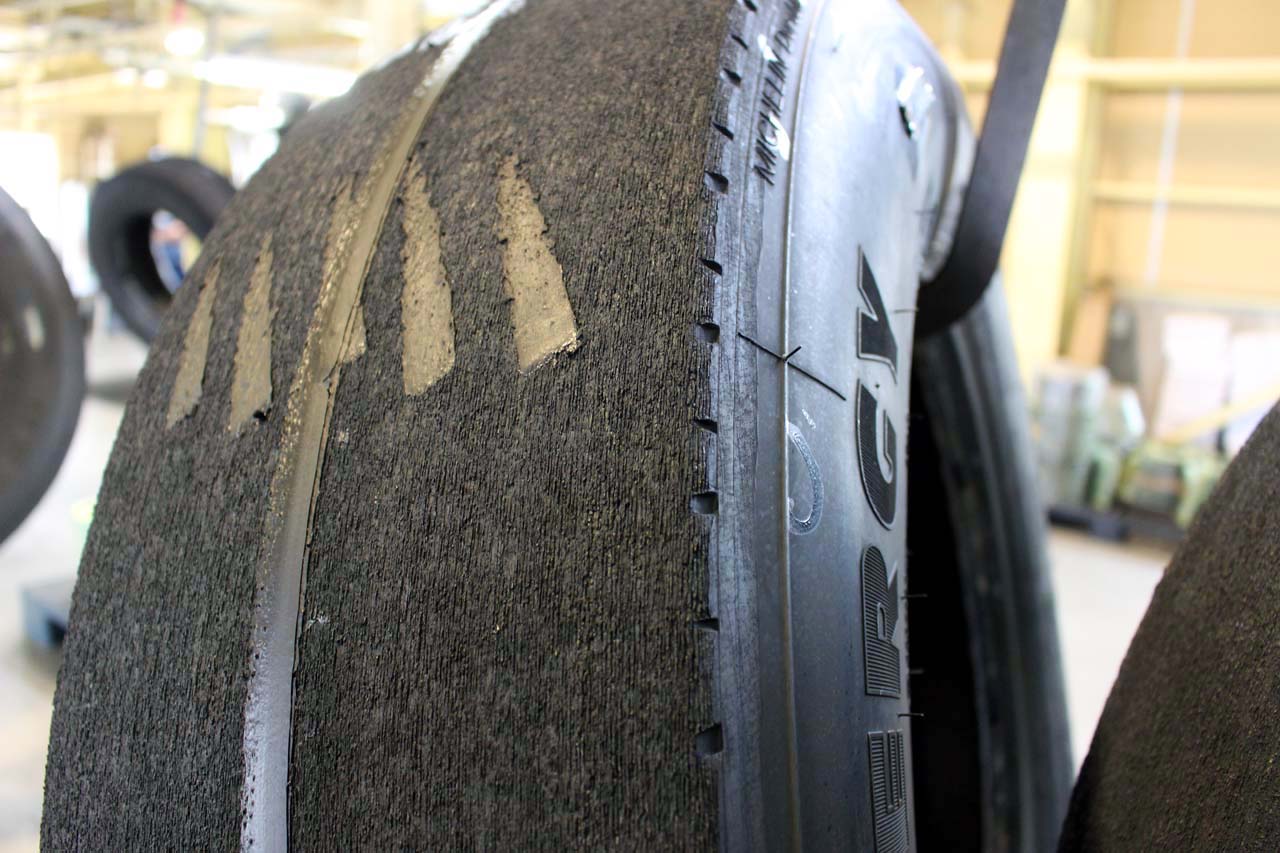
ここからはいよいよトレッド面の貼り付けとなります。このトレッド面はあらかじめパターンが付いており、溶剤を塗布したうえでこれをケーシングに巻き付けていきます。ここで求められるのは継ぎ目をブロック形状に合わせる高度な技術。作業ではトレッド面とケーシングと一体化するためのテーピングも同時に行われていましたが、作業を終えたタイヤを見ると合わせ目が寸分の狂いもなく貼り付けられ、ホチキスでしっかりと固定されていたのです。これには驚きました。
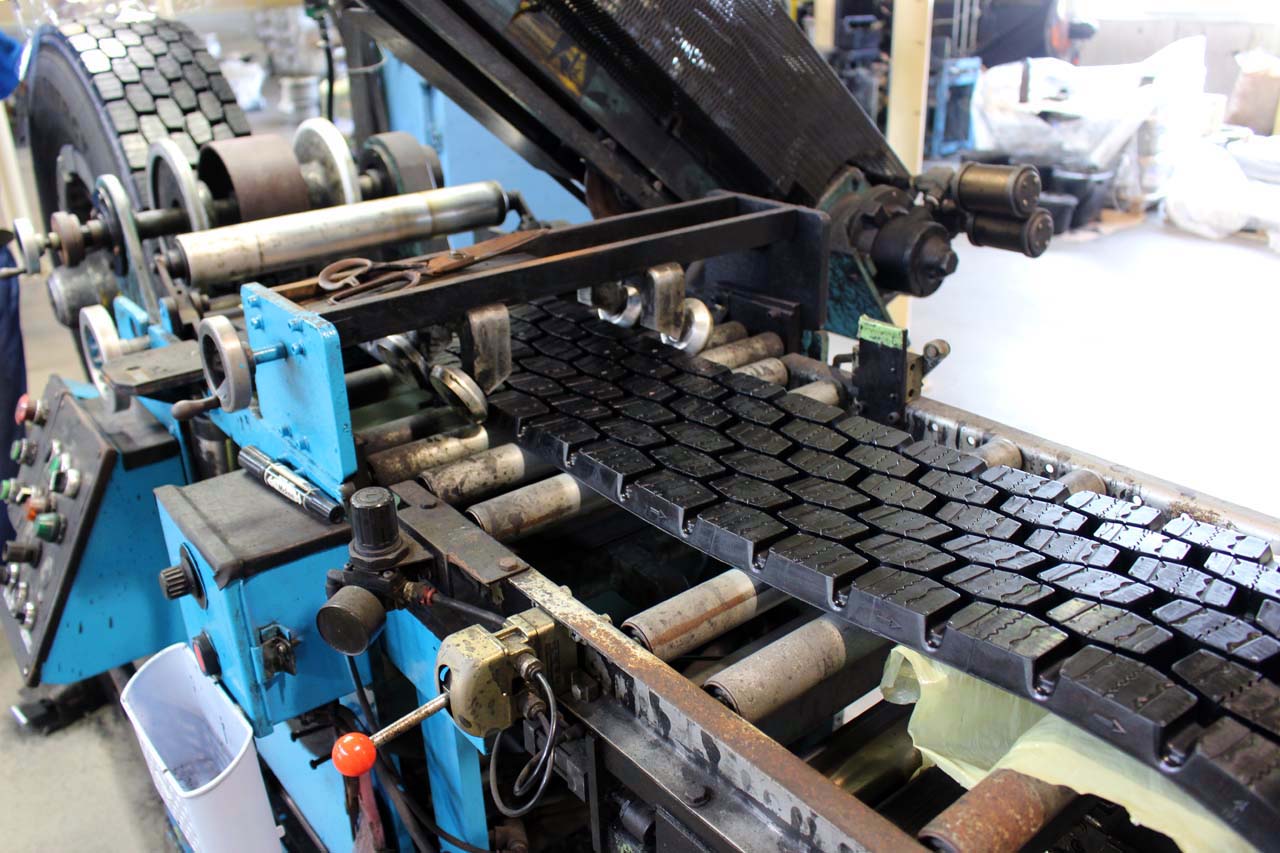
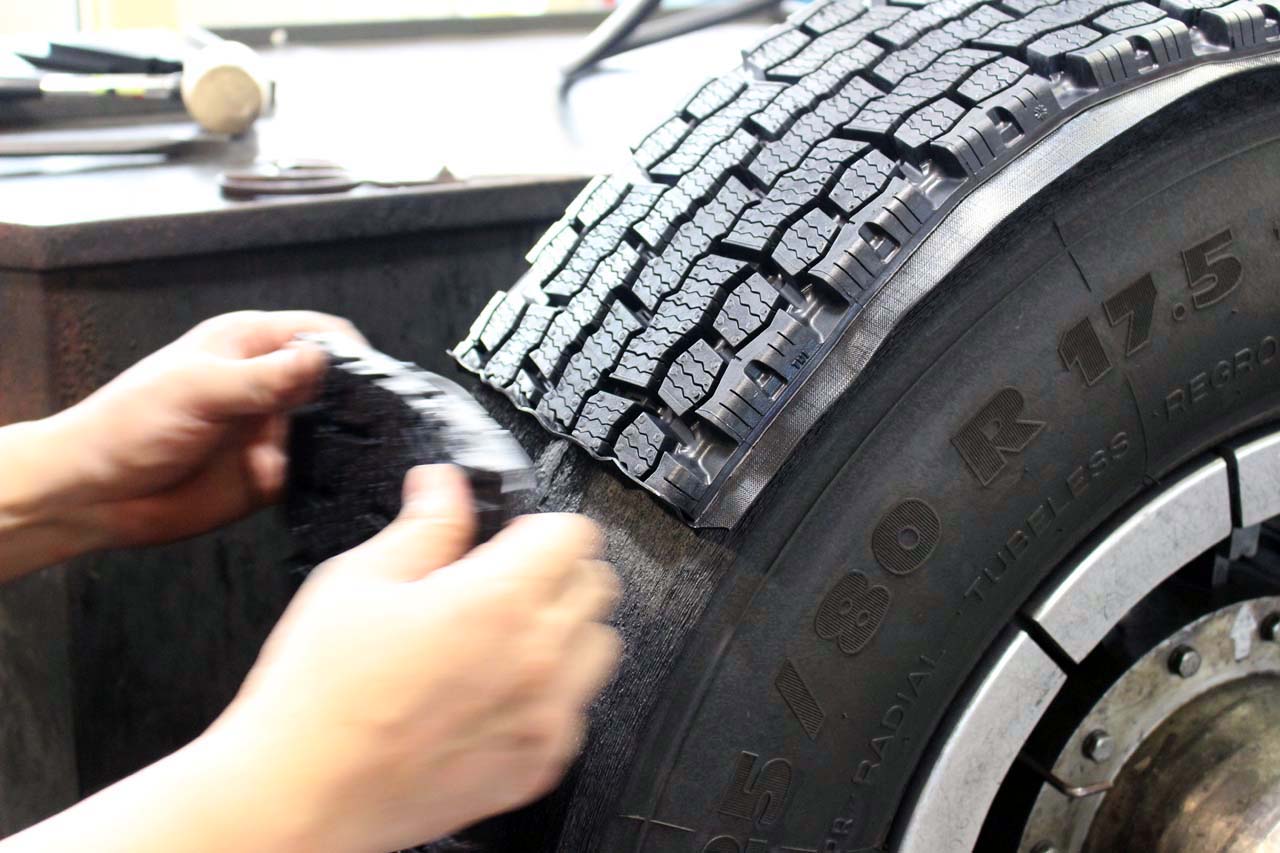
<動画でもチェック!>
そして、タイヤに熱を加えてケーシングと一体化させる最終工程へと移ります。ここで成形作業を終えたタイヤはエンベロープと呼ばれるゴム袋で包まれ、包んだあとは不要な空気を抜いていよいよ加硫機のなかに入れられて熱が加えられます。数時間後、加硫を終えたタイヤはエンベロープが外され、もう一度機械を用いて実際の走行状態と同レベルの圧力をかけて耐久性をチェック。目視でも検索を終えたタイヤは温かいうちに専用塗料を塗られてリトレッドタイヤは完成となるわけです。
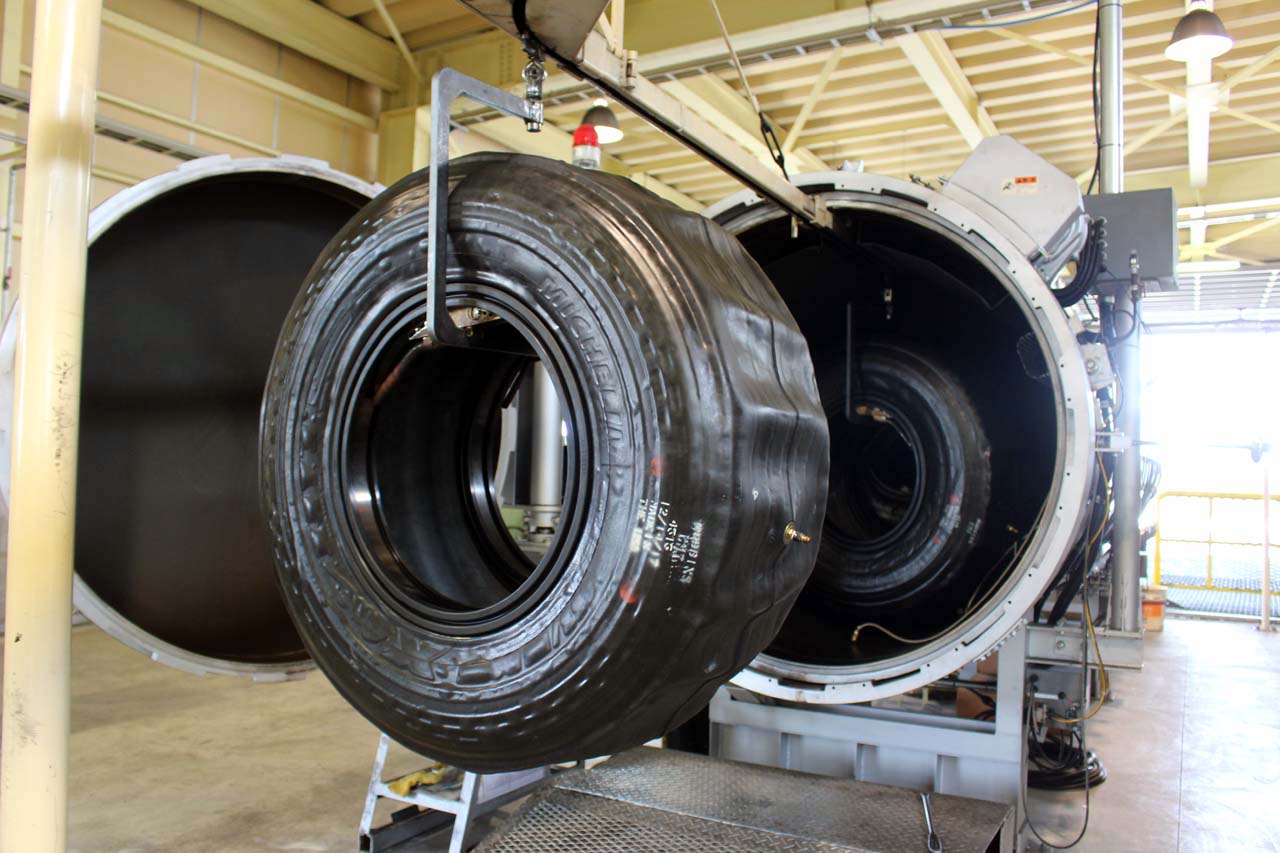
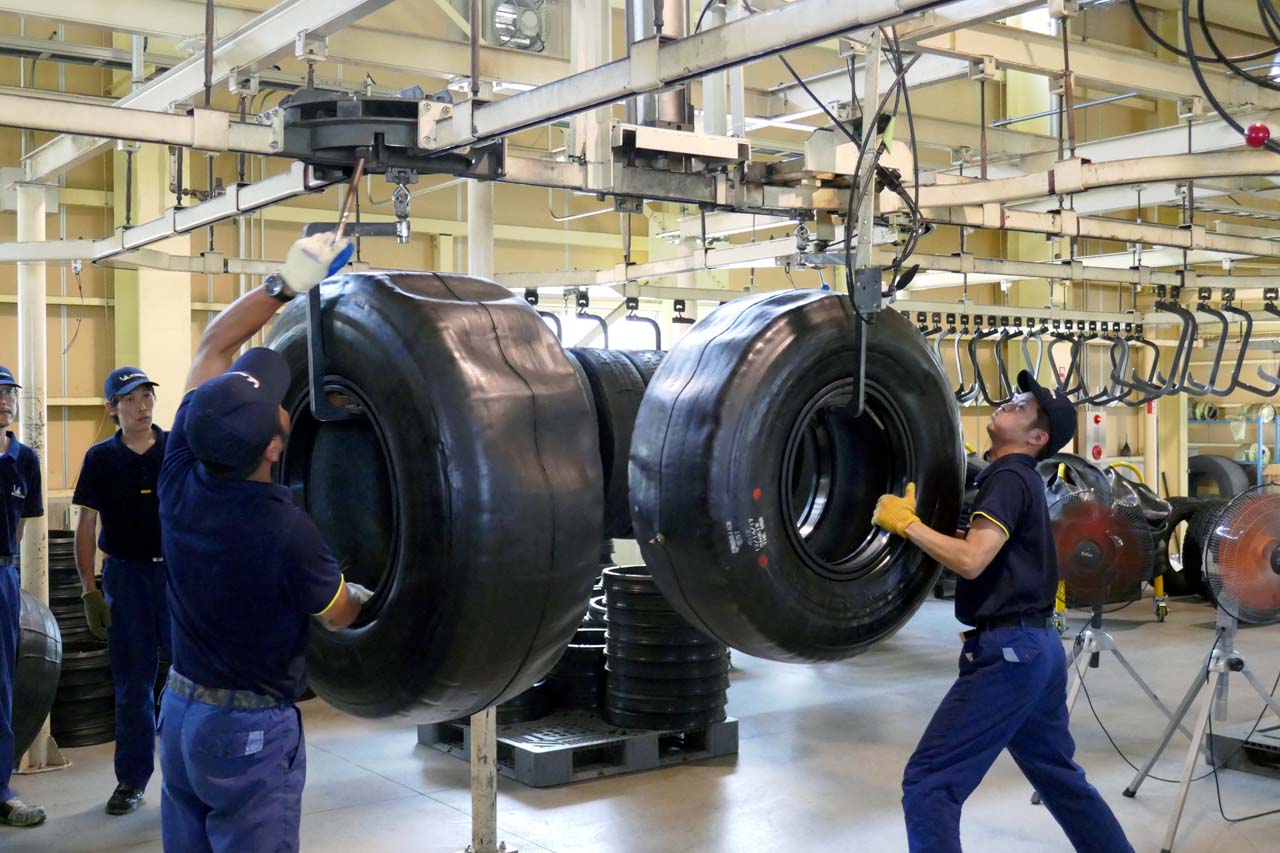
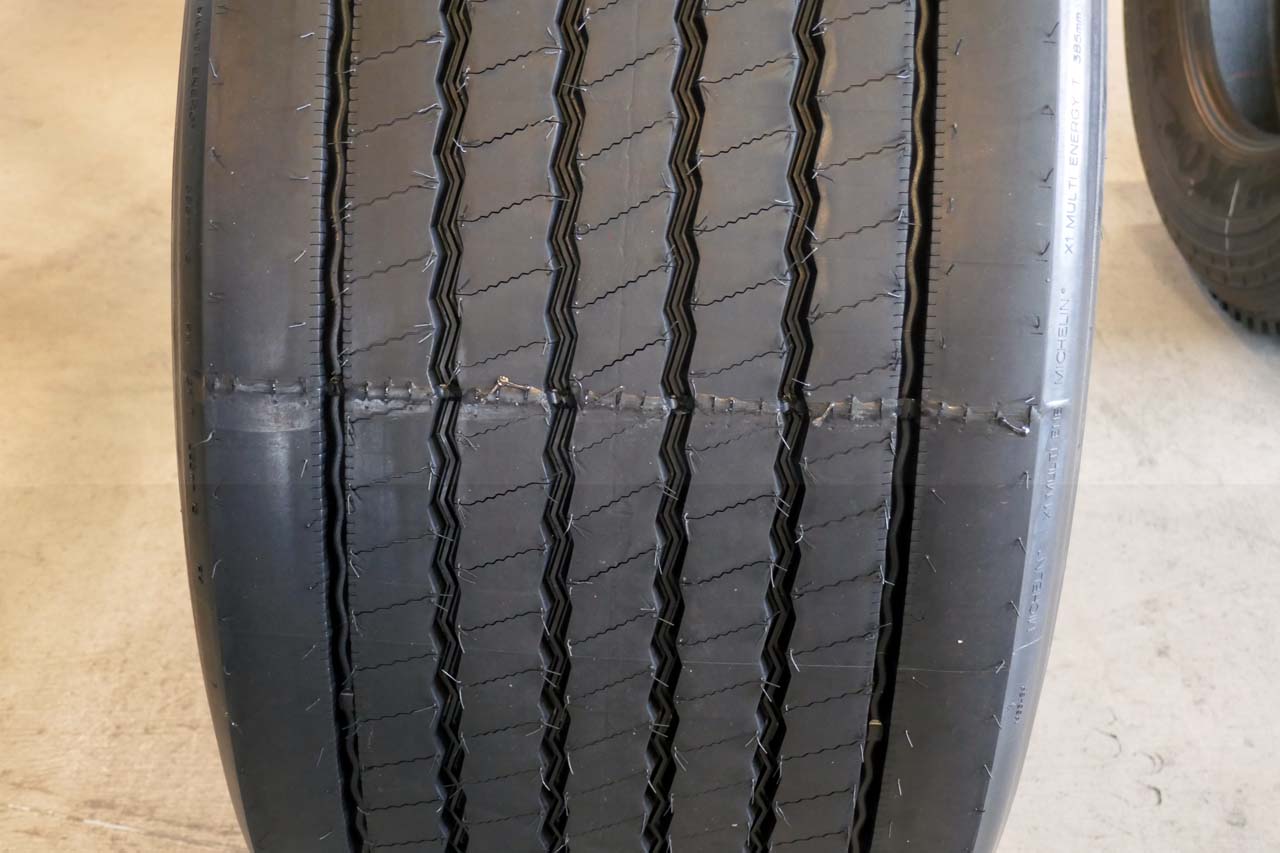
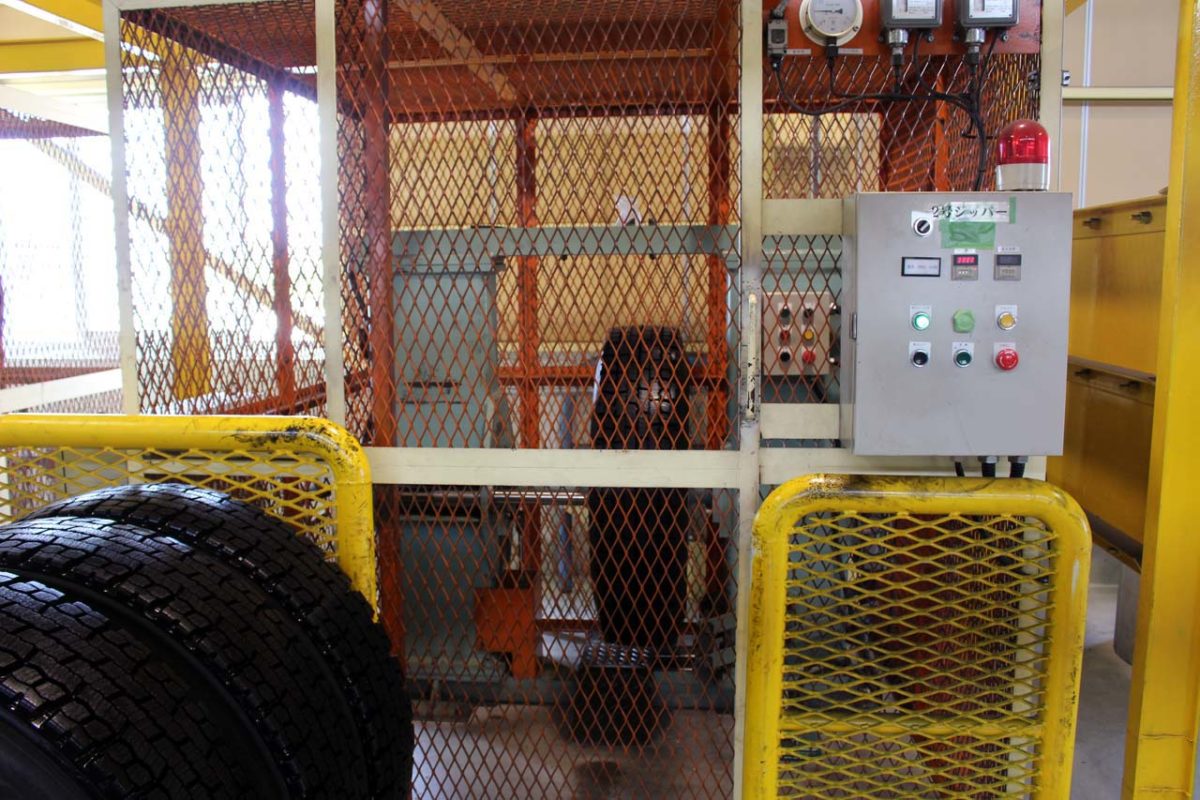
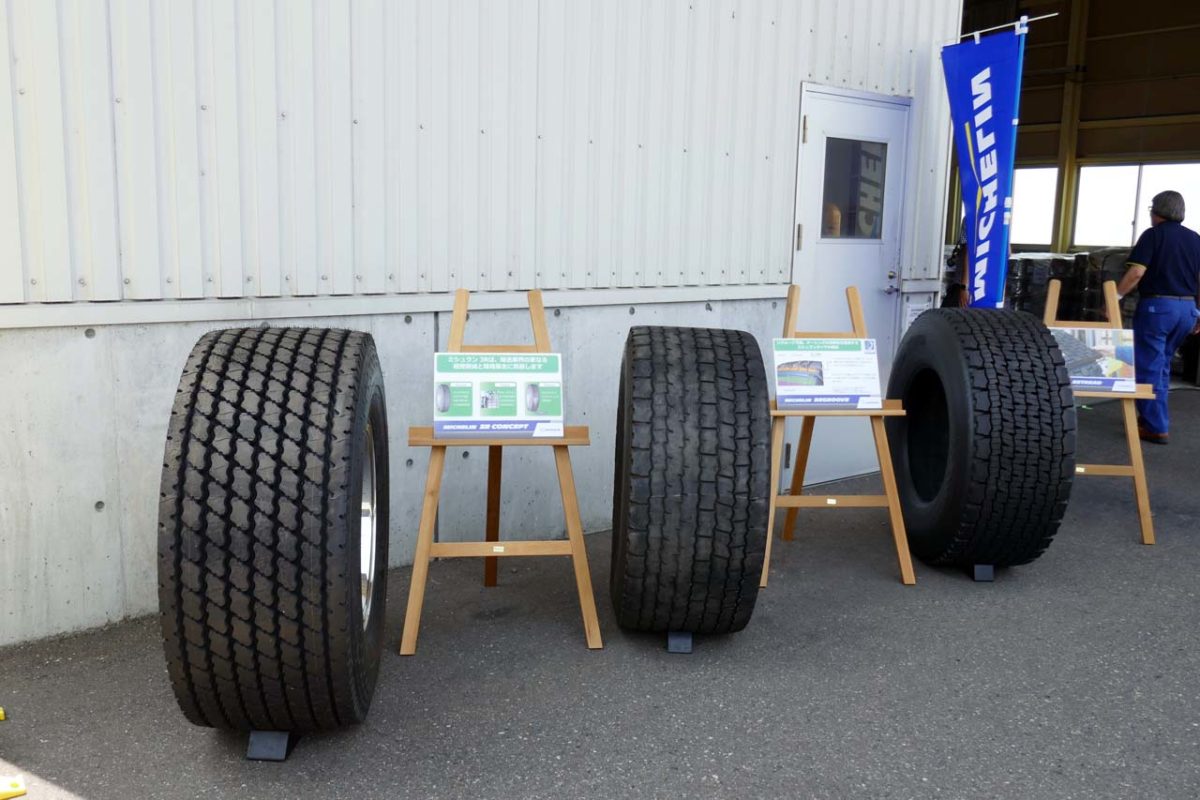
<動画でもチェック!>
ところでこの方法は「コールド(プレキュア)方式」と呼ばれるもので、“多品種少量生産”に向いているとされます。たとえば多くのパターンに対応するのに有利とされます。一方、ケーシングにパターンがついていないトレッド面を貼り付けて金型に入れてパターンを付けるのが「ホット(リ・モールド)方式」です。生産効率が高いのはこちらの方式ですが、あくまで同一のパターンであることが前提となります。日本ミシュランタイヤによれば、海外では一部で「ホット(リ・モールド)方式」で生産している工場もあるが、大半は日本と同じ方式で対応しているとのことでした。
なお、日本ミシュランタイヤは、今年10月よりトラック・バス向けワイドシングルタイヤ「MICHELIN X One(ミシュラン エックスワン)」のリトレッドタイヤ2種を発売すると発表しました。1つはあらゆる天候の路面で優れたグリップを発揮する「MICHELIN X One XDN 2 リトレッド」で、もう1つはトレーラー用「MICHELIN X One MULTI ENERGY T リトレッド」。
もともと「MICHELIN X One」は、トラックの後輪に装着されている2本(ダブルタイヤ)を1本にするというコンセプトで開発されたタイヤで、1車軸当たり約100kgの軽量化を達成することができ、車両の輸送効率向上と環境負荷低減の貢献に寄与するとのことでした。日本ミシュランでは「X One」のリトレッド化を実現することで、ユーザーの選択肢を広げていく考えです。