工場の生産ラインを効率化・省力化しながらコストダウンと生産力を同時にアップする。製造業にとって業績を左右する重要なポイントだ。そのため、経営者および経営幹部が様々なデータを分析した後に経営判断し、長い時間と多大なコストをかけて生産ラインを見直してようやく実現する、というのが一般的。しかし、それをわずか4人の社員がたった数日で、しかも数万円のコストで成し遂げたとしたら――。
舞台は、施設用照明器具や防災用照明器具などを製造販売するパナソニック・エレクトリックワークス社ライティング事業部の新潟工場。ものづくり革新センター生産技術開発部工法開発課の徳吉潤成主任技師は、2014年に横浜で開催された「からくり改善くふう展」(日本プラントメンテナンス協会主催)に先輩に誘われて視察に行った。トヨタやホンダ、マツダなど日本を代表する自動車メーカーを中心に100社以上が参加しているイベントで、パナソニックグループからは家電事業を手掛けるアプライアンス社が家電メーカーとしては唯一、2013年から参加している。その名のとおり、電気やエアーなどの動力を使わず、江戸時代の「からくり人形」のように単純な仕組みを用いて工場の作業効率や生産効率を改善している取り組みを紹介するものだが、そこで衝撃を受け、自分も取り組んでみたいと思いつつも、直後に他への出向の辞令が下りたことで、思いは一時中断する。
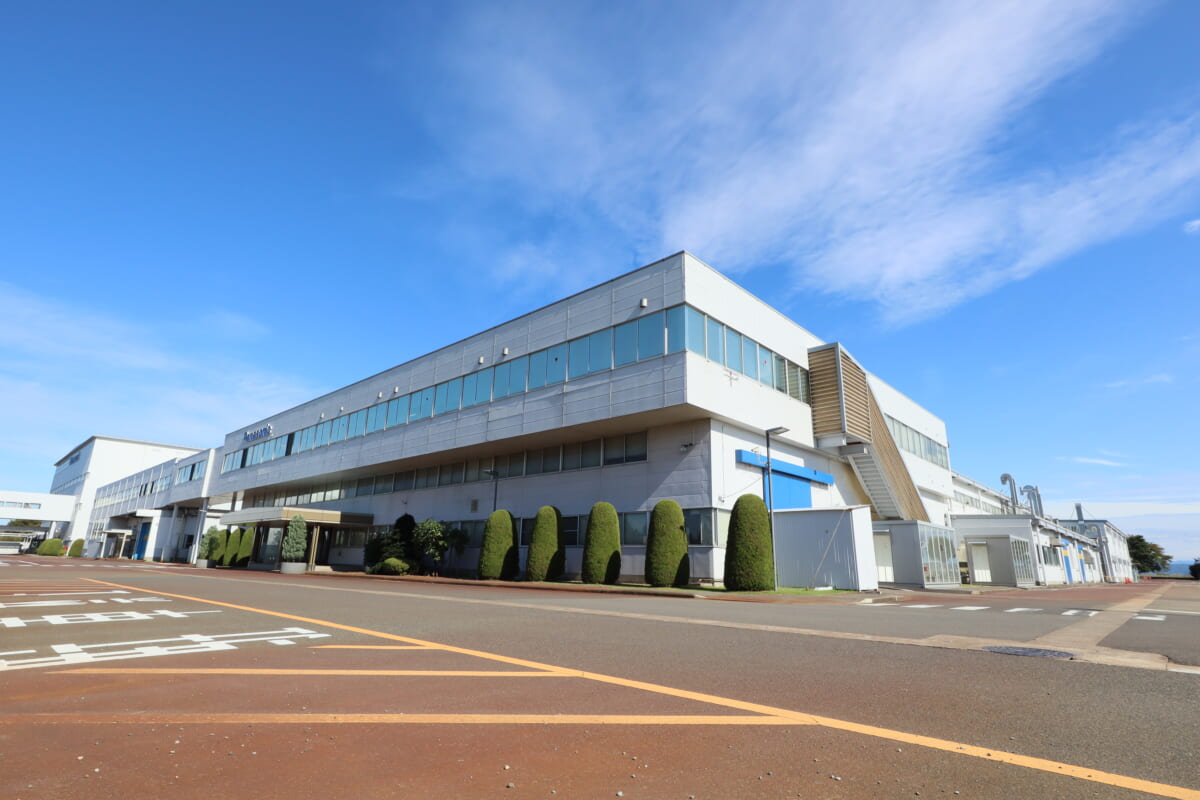
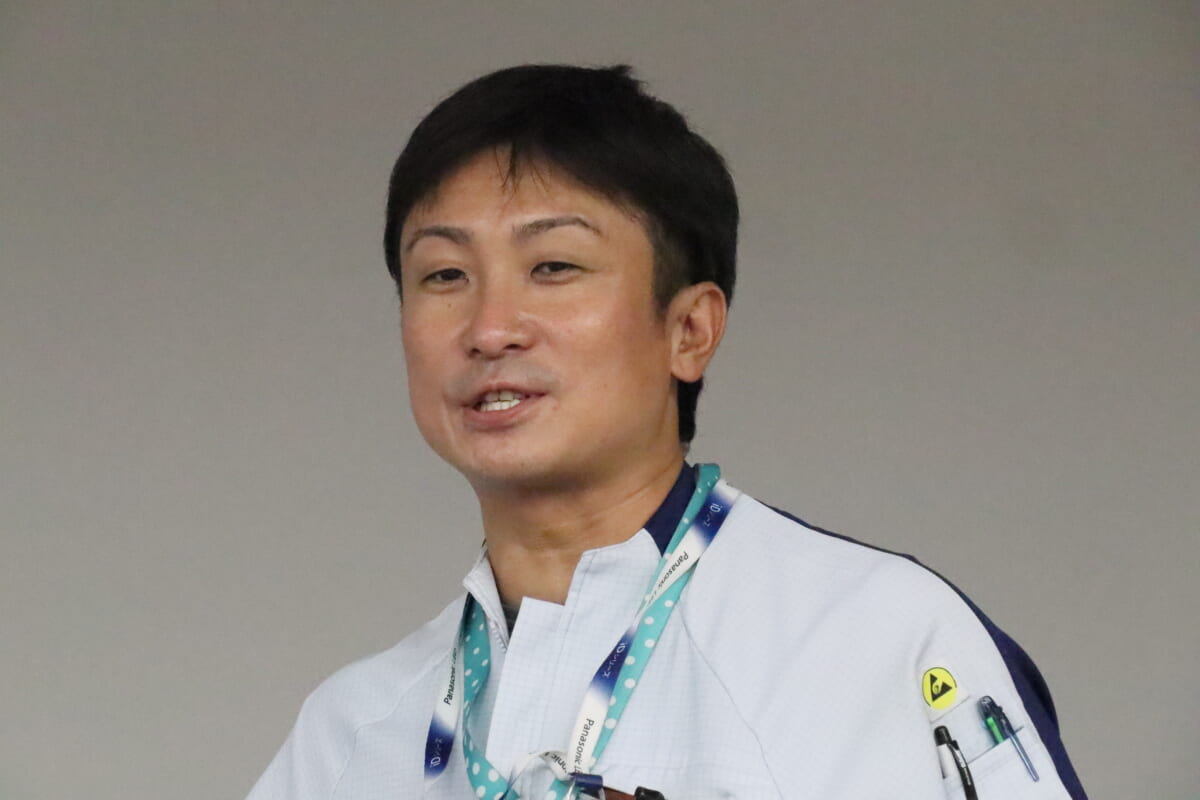
人が機械に働かされている、機械のお守りをしているという危機感
転機は2017年。出向先から新潟工場に復帰した時、製造ラインの職長からある困りごとの相談を受ける。「現場を改善したい。ラインのハイテク化が進んでいるが、現状、ハイテク設備に関わるスタッフたちの労力を、機器のお守りのためだけに浪費しているように思える。一方で、パート従業員が増えている中で、ハイテク化した設備をコントロールできる教育を施すのは難しい。製造業として、製品にもっと気持ちを込めて製造できるような環境を今一度構築したい」と。
有名な映画のように、人間が機械にただ働かされているようにはなりたくない。自動設備の監視のためだけに従業員を張り付けたくない。人間らしい工夫により、働く従業員の困りごとを解決したり、作業しやすい環境を整えたい。職長のそんな意向を受けて工場内を回ってみると、ラインスタッフたちの小さな、しかし、深刻な不満・悩みが見えてきた。冒頭述べたように、製造ラインは入念な設計と多大な費用で構築されており、実際の運用後に生じた小さな不具合を直すだけでも時間とコストがかかる。よって、人間が機械に合わせるということが往々にして行われる。そして、きつい労働に音を上げて人材がどんどん流出する。
「電力やエアーを使わずにローコストで安全な装置を迅速に製作して、作業スタッフを少しでもラクにさせたいと思った」。そこで思い浮かんだのが3年前の、からくり改善くふう展で見たからくり装置の数々。徳吉氏は早速、越後大郷からくり館の日吉館長に会いに行き、江戸時代のからくり人形の内部を見せてもらい、その構造を学んだ。
部品はすべてホームセンターで購入
そうして出来上がったのが、作品名「どんだけ~1コウ(号)」。非常用照明の完成品を梱包した箱を、コンテナにまとめて積み込むまでの一時的なストック場所に導入した装置だ。ふざけたネーミングだが、現場の困り事を短期間、かつローコストで解決した優れた仕組みで、パナソニック社内のからくりコンテストで優秀賞、日本プラントメンテナンス協会(JIPM)からくり改善くふう展で協会特別賞を受賞している。
具体的な仕組みはこうだ。従来、箱詰めされた完成品は、機械で自動的にテープ止めされ、ベルトコンベアとローラーで一時保管場所にストックされる。一時保管場所にある程度の数がストックされたところで、作業員がコンテナに載せ替えて出荷場所まで移動するのだが、この一時保管が問題だった。ローラーで滑ってきた箱の向きが揃わず、縦向きになることで定数通りにストックできなかったり、溢れて箱が床に落ちてしまうことが頻発した。そのため、箱の射出口に作業員を1人配置し、排出された箱の向きを揃えるという作業が発生した。完成した箱が出てくるのは10秒に1個。そのために作業員を1人貼り付けるのである。人件費の無駄もさることながら、「楽な作業でいいよね」と他の作業員に揶揄される係員の精神的なキツさも問題になっていた。暇な仕事は思いのほか精神的に圧迫するのである。
初期に開発した「どんだけ~1コウ(号)」。スタートのコンベアの押し出す力だけで箱が整列して2列にストックされる
「どんだけ~1コウ(号)」は、箱の射出口に設置することで、自動的に箱の向きを整え、1列に7個をきっちりとストックする。1列目がいっぱいになると自動的に2列目にストックし始める。動力は一切使っておらず、最初に箱がベルトコンベアから押し出される勢いのみで自動的に滑り落ちていく。使っている部材は、すべてホームセンターで購入したもので、製作費は約4万6000円。製作期間はわずか5日間だという。
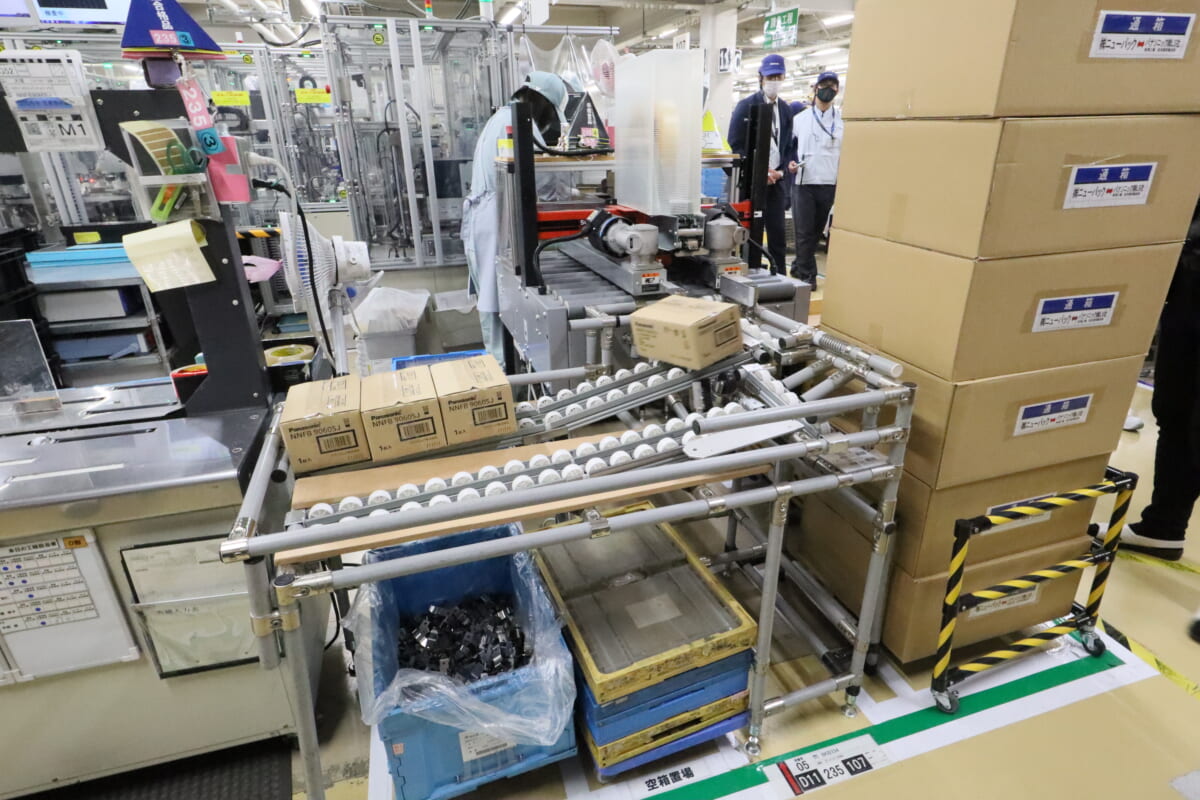
「同様のものを自動設備として製作すると部品だけで150万円、設計費などを入れると300万円ほどかかる。電力などの動力を使うと、万一の事故に備えて安全装置を導入する必要があるため、それだけでコストが嵩むし、申請から承認を得て完成するまで半年はかかる。10秒に1個排出される箱をただ黙って見ているだけの辛い仕事をさらに半年続けさせるのは忍びなかった」と徳吉氏は当時を振り返る。
「どんだけ~1コウ(号)」の導入によりイニシャルコストが抑えられたが、専門の作業員が不要となり、箱が貯まる間は別の作業ができるため作業性が向上したことで年間870万円ほどの生産性のアップも図れている。
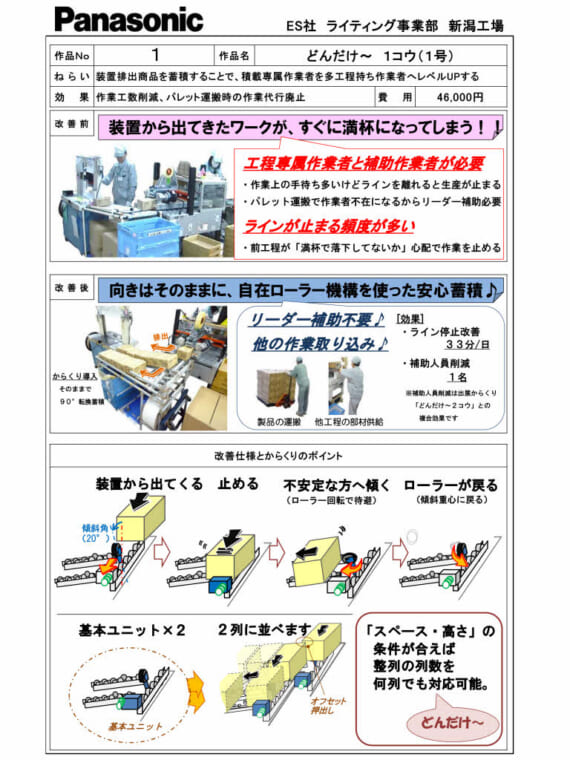
「こんなもの役に立つのか」「仕事中に遊んでいる」
導入コストが低く、導入期間が短く、それでいて生産性が向上と大きな効果を出す。良いこと尽くめのように思えるが、当初はこの活動に対して、周囲の理解はなかなか得られなかった。倉庫の片隅で、ホームセンターから購入してきた安価なパイプなどを、ああでもないこうでもないとチャカチャカ組み立てている姿が遊んでいるように見られたのである。「年下の後輩にさえ、“こんなもん約立つのか!?”“仕事中に遊んでいる”と大きな声で嫌味を言われる状態でした」。そのため、当初は同じ部署だった徳吉氏の先輩である梨本賢一氏と田辺英明氏、後輩の黒澤真一朗氏の4人で同好会的にスタート。就業時間外に集まって機構の研究・開発に勤しんでいた。
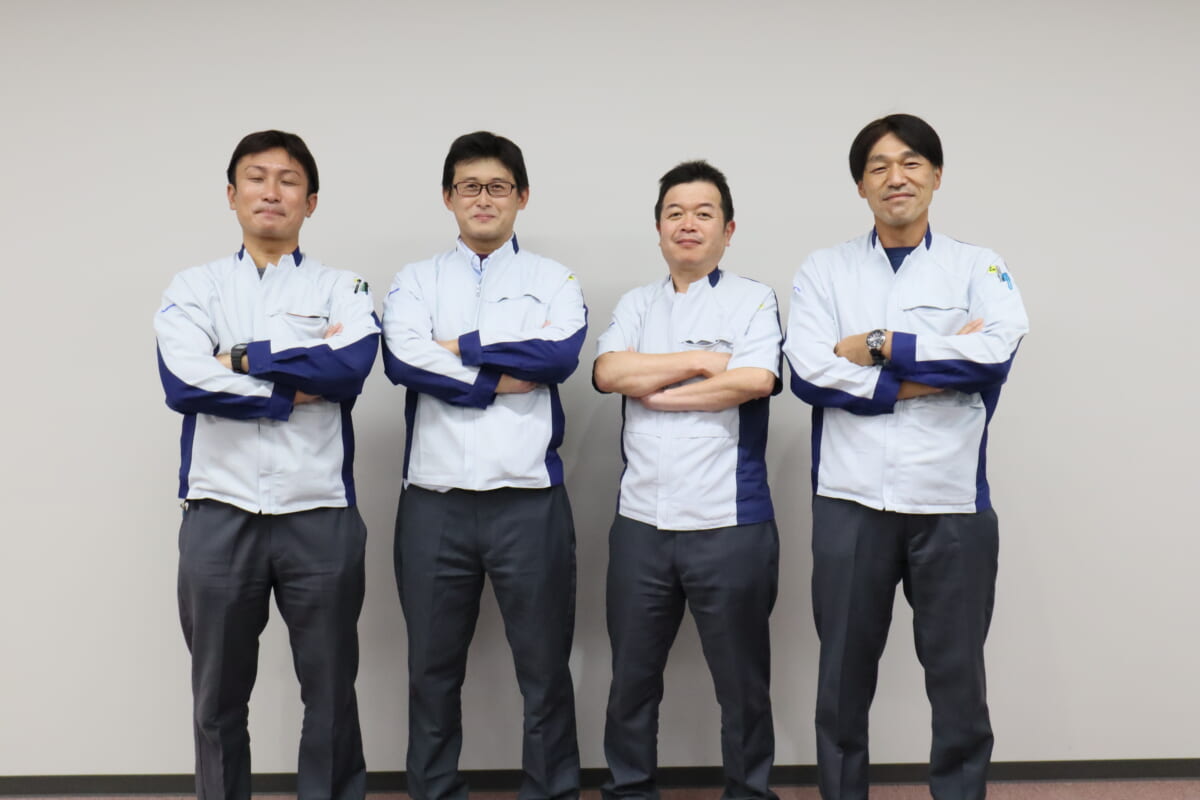
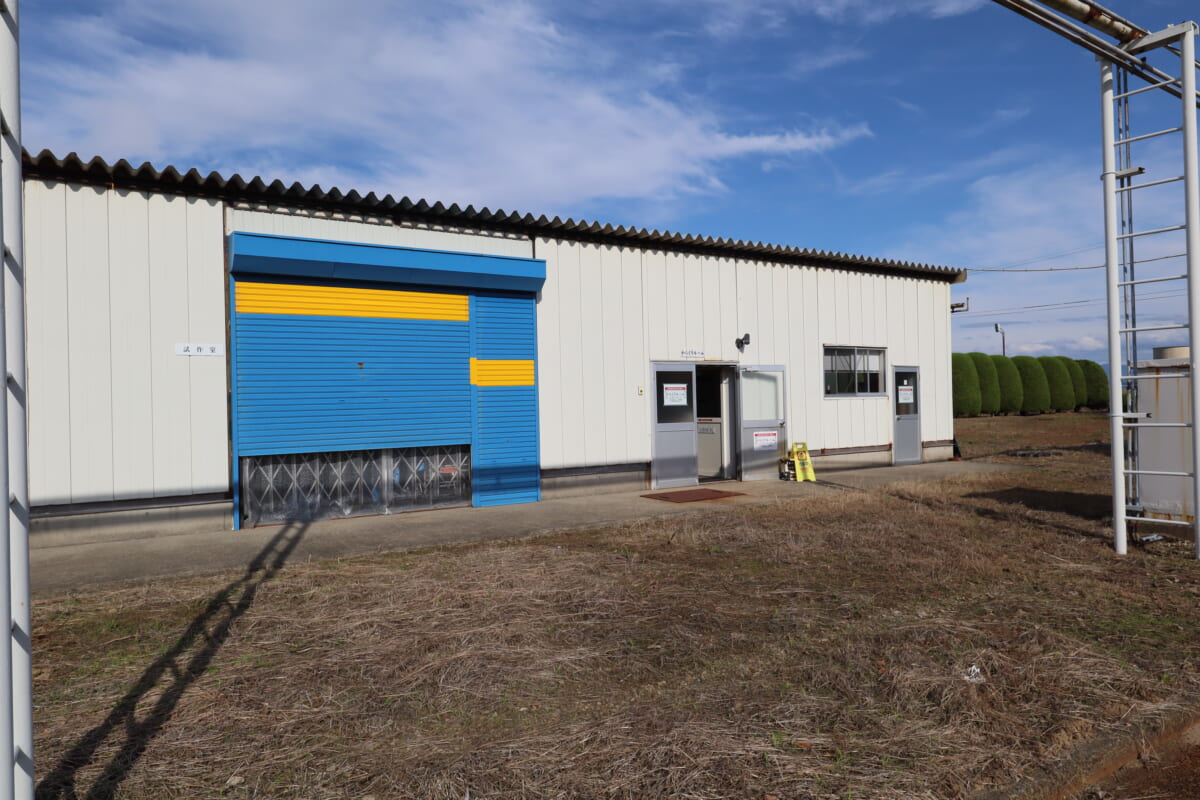
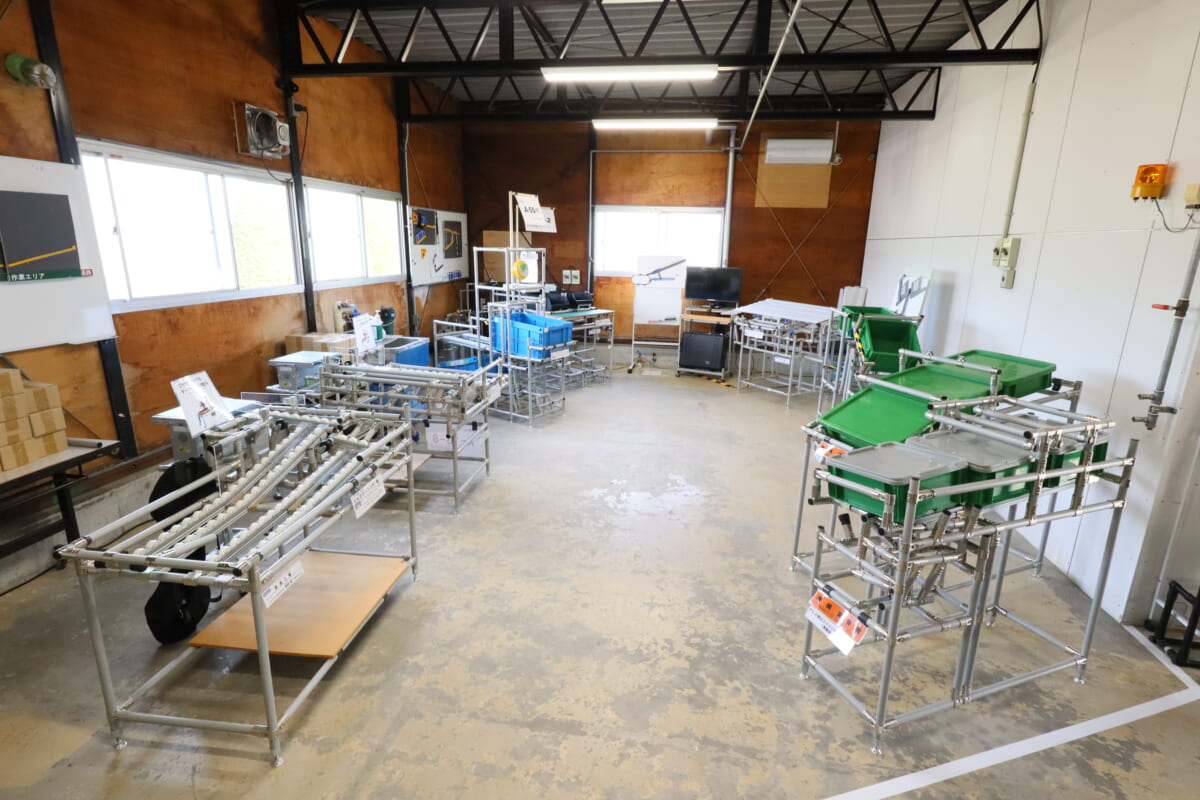
しかし、「どんだけ~1コウ(号)」が潮目を変える。その実績を見た工場長が業務として認め、就業時間内の作業を認めてくれたのである。「現場からも高く評価されました」と徳吉氏。「ラインの女性リーダーから、“それまでは完成品の射出口に誰か1人が待っていないとラインが止まってしまって非効率だったけど、どんだけ~1コウの導入で流れがスムーズになり、人員も3人から2人に減らせました。このからくりは私の中で最優秀賞です”との言葉をもらったことで、自分の活動は現場に役に立っていることが分かりました。それまでの苦労や周りの厳しい視線が一気に吹っ飛び、俄然やる気がでてきました」。
そうして次に出来たのが「どんだけ~2コウ(号)」。目的は1コウと同じだが、1コウが小型の梱包箱1種類のサイズにしか対応していないため、導入できるのは特定の製造ラインだけだった。そこで2コウでは、切り替えスイッチや機構を組み直すことなく、大中小の異なる3サイズの箱に自動的に対応できる仕組みとした。小サイズの箱は4つが溜まったら鹿威し(ししおどし)のように自動的に下に落ち、大中サイズの箱は3つ溜まると自動的に落ちる。センサー類は一切使っておらず、箱がレール上のレバーを押すことでロックが外れて箱の自重で台が傾くという単純な機構だ。なお、1コウ、2コウともに、ストック場所は無限に増やすことが可能だ。
「どんだけ~2コウ(号)」は異なるサイズの箱にも対応できる
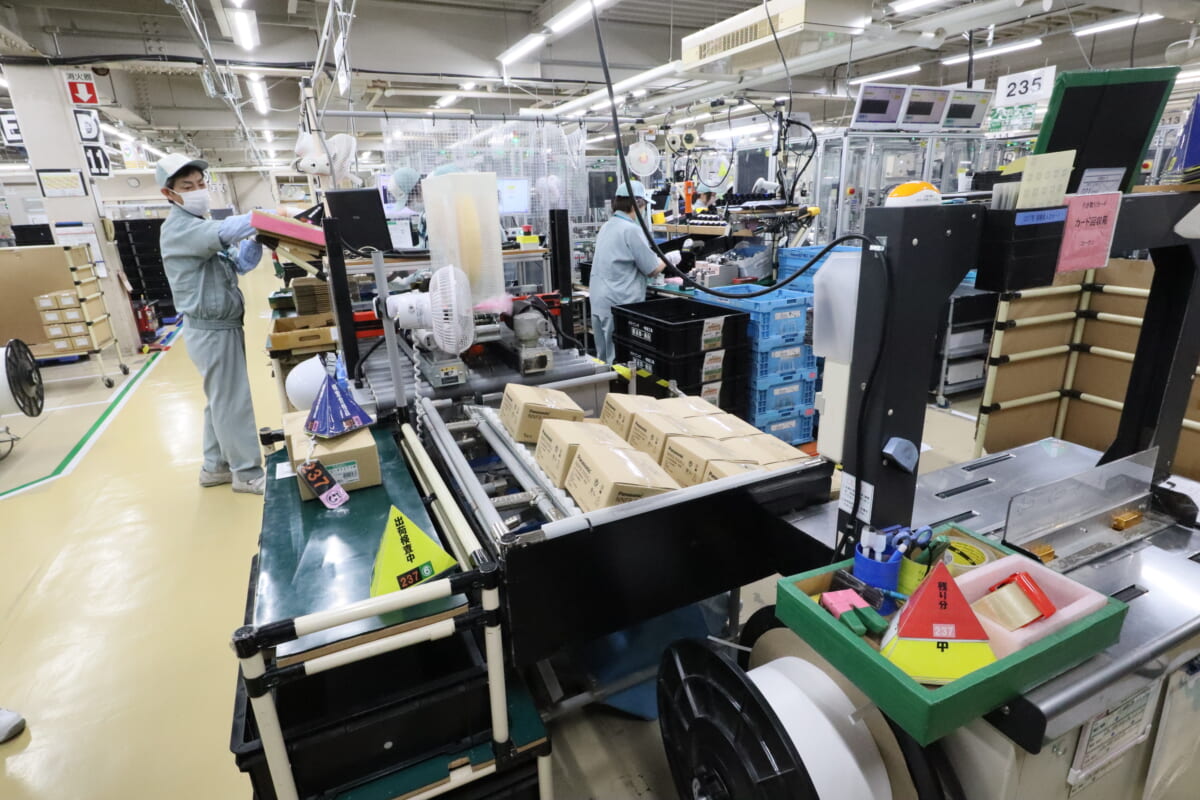
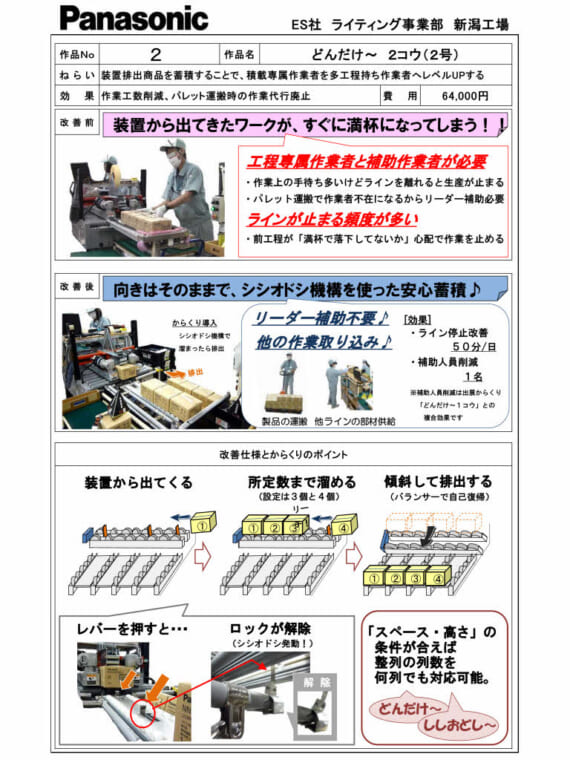
目が回り、腰を痛めてすぐに人が辞める職場
4番目に製作した「シャカの手リリース+オプション」は、現場作業員の健康改善にまで取り組んだという点で、さらに貢献度が高いからくりだ。
避難誘導灯パネルを組み立てる工程において、作業員は前方から供給されるパーツボックスからパネル部品を取り出した後に180度振り返り、背後の作業台で組み立てる、という作業をしていた。1日あたり2000回以上も体を反転し続けるため、目が回ったり腰を痛めたりと、体調不良を訴えて退職する人が後を絶たない作業だった。パーツボックスの供給と空箱の回収は人力で行うのだが、空箱を人の手で上から下におろす労力も合わさり、1カ月の間に数人が辞めていくというのだから、かなり過酷な作業だったことが分かる。
そこでまず、パーツボックスを2箱供給できる台を作り、1つのボックスが空になったら足元のレバーを踏むことで空のボックスが自動的に下に落ち、2つめのボックスが手前に滑ってくる機構の「シャカの手リリース」を製作。これにより、ボックス交換の労力と時間が削減できた。さらに、作業者の背後にあった作業台をからくりの上に取り付けることで振り返り動作がなくなり、体の負担が大幅に削減する。ただ、導入してみて分かったことだが、ボックス供給のレールは、ボックスが手前に滑るよう緩やかな傾斜をつけているのだが、その勢いでパーツがボックスの前方に偏り、重圧がかかって1枚1枚が取り出しにくくなり、作業員が手を痛めてしまう。これを改善するため、ボックスを手前に引くと自動的にボックスが水平に持ち上がり、中のパーツが取り出しやすくなるようにした。それが「+オプション」。導入してからも、作業員の声を聞いてすぐに改良できるのが“からくり機構”の良いところだ。
「シャカの手リリース+オプション」は、空箱の排出と部品の供給を一度に行うことで労力と作業時間を削減し、手前に作業台を設けることで作業員の身体的負担を軽減した
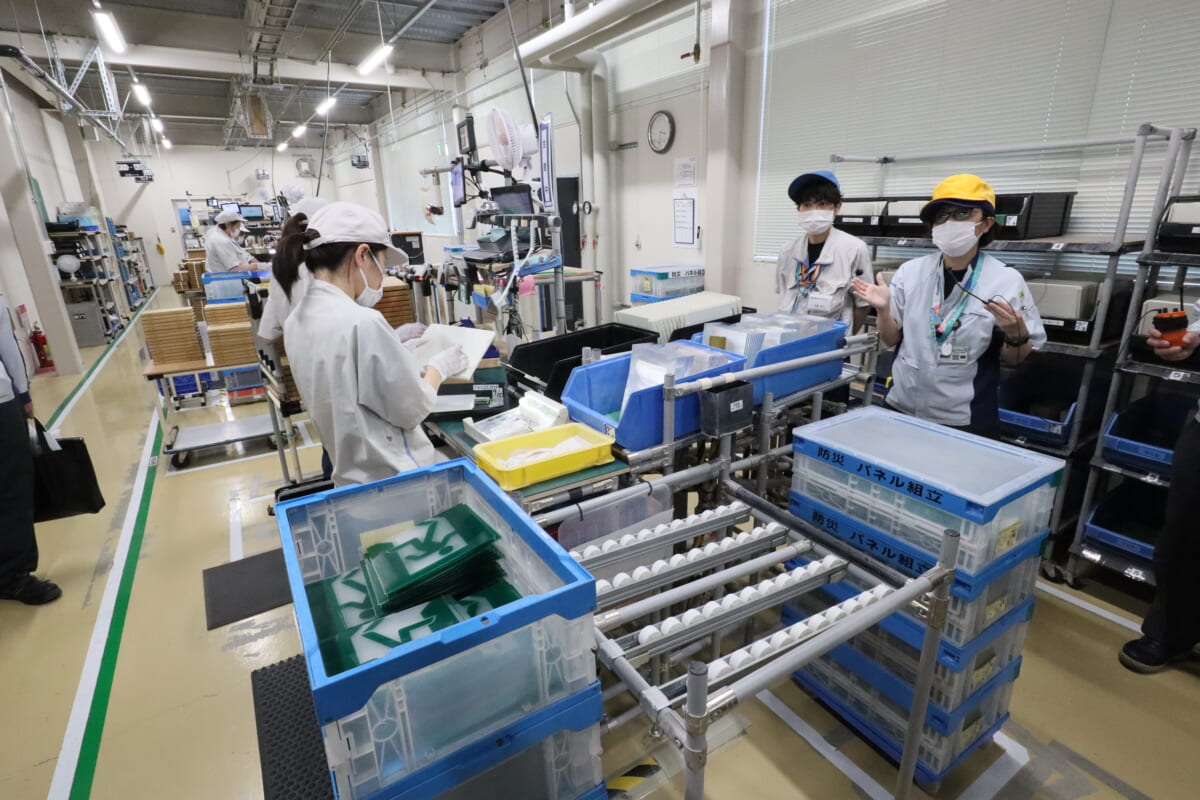
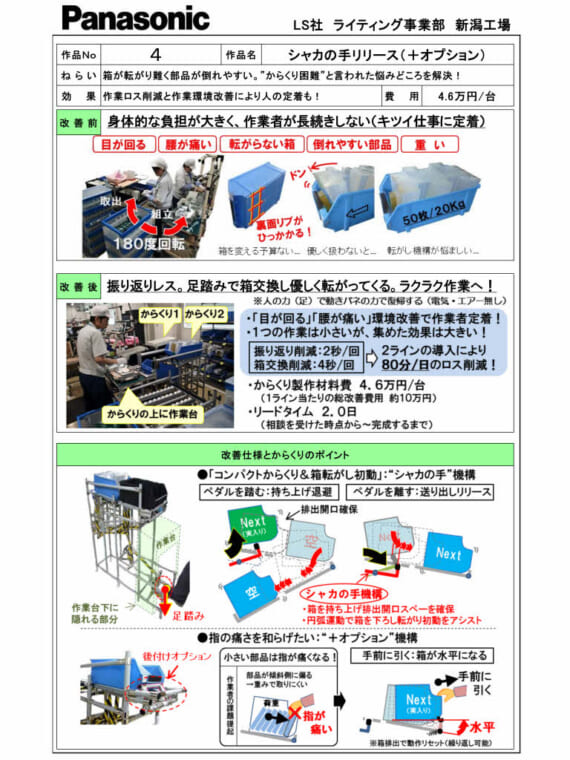
「シャカの手リリース+オプション」の製作費は約4万6000円。製作日数は、現場から改善を相談されてからわずか2日。ボックス交換作業の効率化と振り返り動作の削減により生産性が向上し、導入効果は年間約250万円にのぼる。対費用効果もさることながら、この人手不足の折、離職率の高い作業の改善は企業にとって大きな貢献となる。
また、LEDベースライトのカバーを自動製造ラインに供給する工程において、人手で直接ラインに供給すると、タイミングが合わずにロスが発生した問題を解決するべく導入した「からくりインバーター」は、費用換算で年間873万円の生産性アップ。しかも、当初は2000万円かけて自動化設備の導入が検討されていたところに、わずか12万円の製作費で大幅な改善効果を生んだということで、2020年のJIMPからくり改善くふう展でアイディア賞を受賞している。
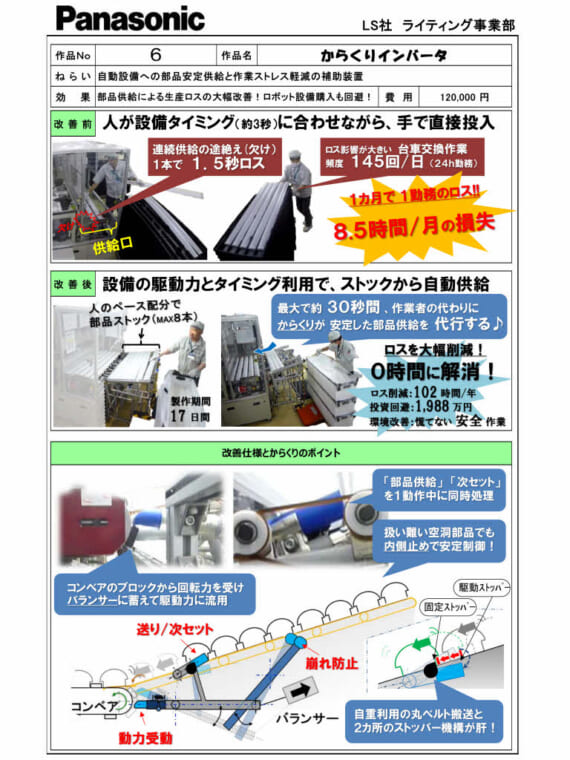
徳吉氏ら4人が製作したからくり機構は現在までに7種10台におよび、2600万円におよぶ高性能生産設備の導入を回避し、人材の有効利用と生産性の向上で2014万円もの費用効果を叩き出している。たった約67万円の製作費でだ。しかもそれらの機構が最短2日、最長でも17日と短納期で製作されており、短期間での課題改善が図れている。
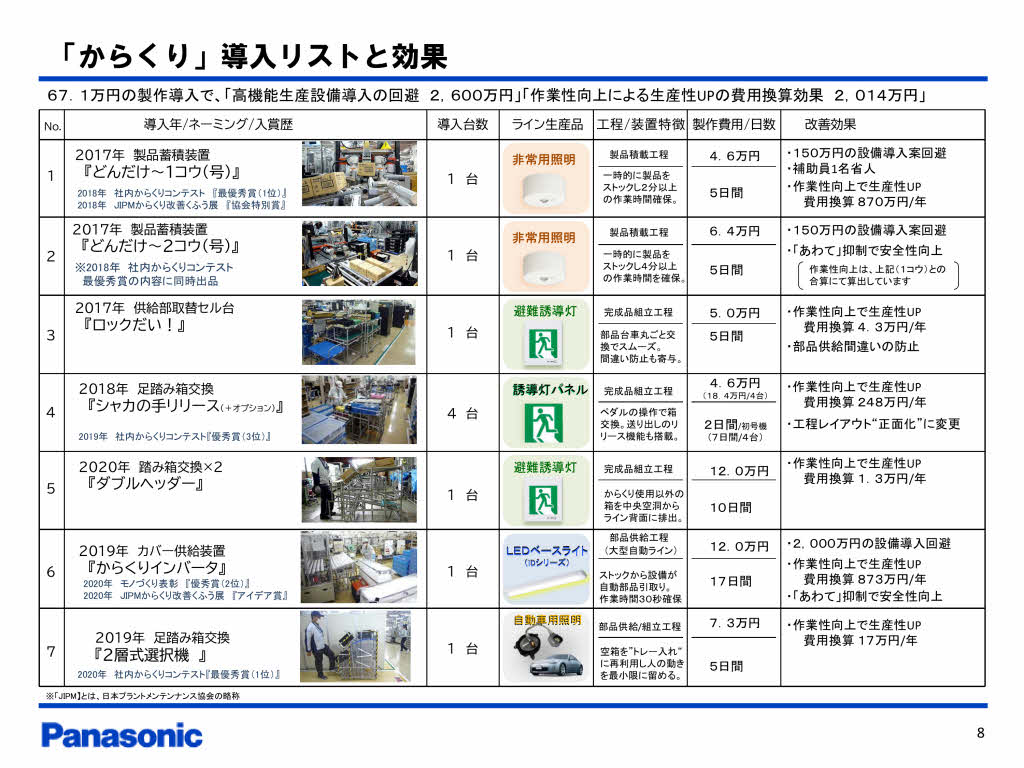
“からくり”は人と機械をつなぐ
からくり機構は部品供給や完成品の一時ストックといった、自動化するまでもない、または工場スペースの都合上、自動機械を導入するのが難しい箇所で使われている。電気やエアーを使った複雑な自動システムは、なんらかのトラブルが起きるとライン全体に影響を与えるため、エンジニアが夜中でも叩き起こされて修理・調整に向かわねばならない。実際、徳吉氏も自動化装置のトラブルで夜中に呼び出しを受けたことがあるという。しかし、からくり機構は従来は人力で行っていた作業箇所に差し込んでいるだけなので、トラブルが発生したらそのまま外し、また人力に戻せばよいだけ。そもそも、からくり機構はどれも単純な仕組みで出来ており、ホームセンターで手に入る頑丈な建設部材を利用しているため、これまでに故障などの大きなトラブル自体が発生していないという。
「従来は、機械による完全自動化か人間による手作業かの二者択一でした。そこに新たに“からくり”という半自動化の仕組みを加えることで現場作業のバリエーションが広がりました。からくりは決してハイテクを否定するものではなく、ハイテクと人間をつなげる役目を担うのです」(徳吉氏)。ハイテクがカバーしきれない人間の動きを補助し、作業員の負担を軽減しながら生産性を上げる優れた仕組みと言えよう。
新潟工場では今年から、徳吉氏ら4人が中心となって他工場の従業員を対象にからくり研修をスタートしている。というのも、からくりは、ライン特有の困りごと・課題を解決するもので、同じサイズ・同じ仕組みのものがそのまま他工場のラインに導入できるわけではないからだ。「唯一無二のものなので設計図すらない」(徳吉氏)ほどユニークなものなので、各工場の担当者にからくりの基本構造と動きを理解してもらい、それぞれの工場でぞれぞれのラインにあったからくり機構を創造し、労働環境の改善や生産性の向上を図ってほしいとの願いから始めたものである。ゆくゆくはパナソニックグループ全体に研修を広げ、からくり自体もパナソニック全社に広げていきたい考えだ。