新潟県に本社を構える「ダイニチ工業」といえば、家庭用石油ファンヒーターのメーカー別販売台数シェアで9年連続1位、および3年連続で加湿器のメーカー別販売数量・金額シェア1位を誇る会社。もちろん、売れている製品だけあり、安全性や品質の高さは折り紙付きです。その理由の一つが、同社がこだわる「地元生産」によるもの。最近の多くの家電製品は海外で製造されていますが、ダイニチ工業の製品は本社のある新潟での生産にこだわっているのです。せっかく日本に工場があるならば、ぜひ「日本一」を生み出す現場を見てみたい!
さらに、同社は社員定着率の高さ(離職率はなんと1%台)、障害者雇用などが評価され「日本でいちばん大切にしたい会社大賞」実行委員長賞を受賞した、いわゆる「ホワイト企業」としても有名。そんな企業の工場の中身はいったいどうなっているのか? 大人も興味津々の工場見学をさせてもらいました。
一般的なイメージを覆す明るくてキレイな工場
工場に入ってすぐに感じたのは「広くてキレイ」ということ。私の場合、工場といえば、暗くて油でベトついた機械がひしめき合っているイメージを持っていましたが、意外なほど清潔感と開放感があります。もちろん大型機械が大量に設置されているのですが、機械はもちろん床までピカピカ。ホコリ一つ落ちていません。
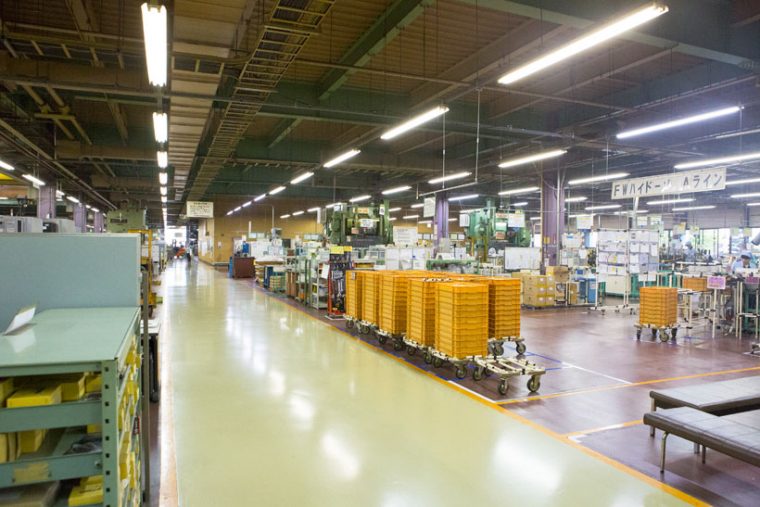
工場の入り口に入ってすぐは、女性たちが手作業で細かなパーツの組み立てをしていました。こちらは、同社のファンヒーターの心臓部ともいえる「気化器」の組み立て作業。この小さな気化器だけでも50近いパーツから出来上がっています。ちなみに、工場のラインで働くのはパートではなく、すべてが正社員。離職率が低いために習熟度が高く、ロボットではできない細かな作業を任せられているのだとか。
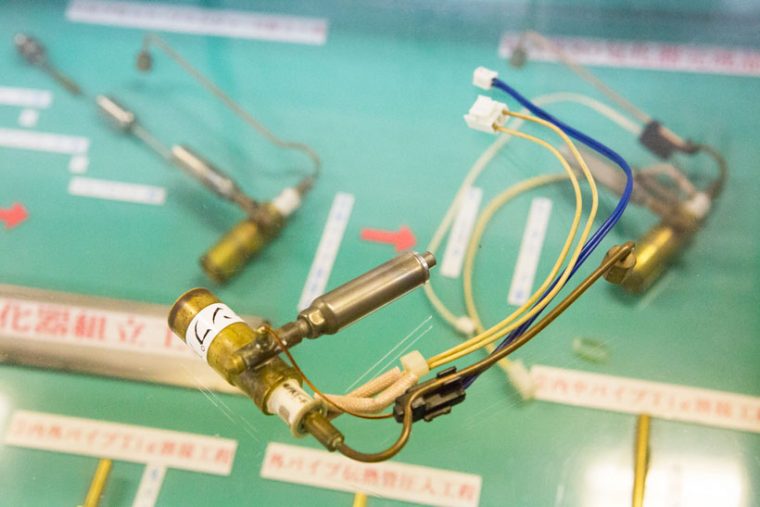
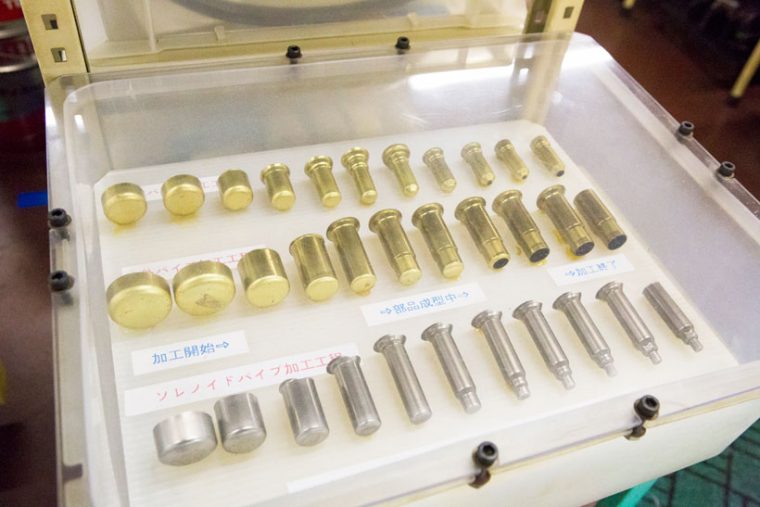
自社一貫生産を実現すべく幅広い技術を網羅
工場といえば「プレス機」。プレス機は、強い力で金属の板に圧力をかけて、さまざまな形に加工する機械です。最大の特徴は「金型」を取り換えることで、作る形を変えられること。じつは、多くの工場はこの「金型」を外注していますが、ダイニチ工業は金型から自社開発しています。
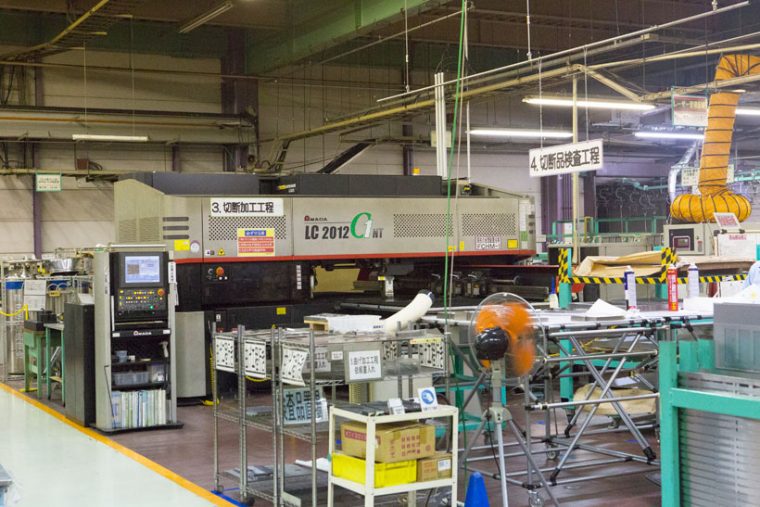
さらに、この工場の凄いところは、この「金型」の交換を10分以内でできること。金属を思った形に加工するには、複数のプレス機を使って段階的に金属を変形させる必要があります。ところが、それぞれのプレス機の金型は、ひとつでも数トンもの重さがあるうえ、金型を変更したあとに調整を行う必要もあります。このため、急に生産する製品を変更しようとしても、金型の交換だけで通常は1時間近くかかるのだそうです。ところが、この工場ではシステムの改良と作業訓練などにより、この金型交換の時間をなんと10分以内に短縮したそう。
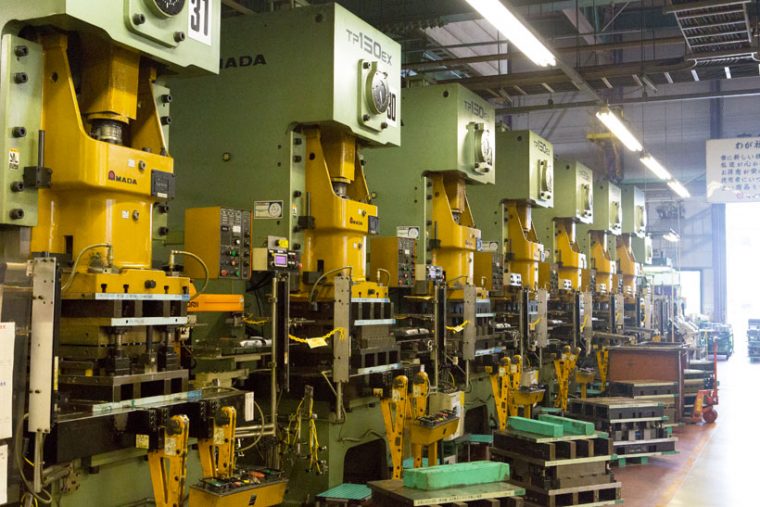
実はこれ、同社独自の「ハイドーゾ生産方式」を実現させるために必要な速度なのです。「ハイドーゾ生産方式」とは、倉庫の在庫が足りない場合に、すぐに工場でプレス塗装から組み立てまでを行うシステムのこと。ダイニチ工業では、なんと朝に量販店から「在庫がない」と連絡が入れば、夕方には「はい、どうぞ!」と製品が出来上がるのだとか。巨大な工場にもかかわらず、驚くべき機動力です。
ロボット導入は人件費のためではなく「人の負担を減らす」ため
また、工場内で目についたのは、さまざまなロボットたち。面白いのが、これらのロボットが「人件費削減」などのために導入されたわけではないこと。重要な作業は、あくまでも熟練した社員が行い、ロボットは単純に速度を求められる作業や、人にとって重労働となる作業を請け負っているのです。なかには、発砲スチロールをダンボールに入れるだけのロボットもいました。これくらいは人間がやるのが普通なのでは……と思いますが、この作業は腰を伸ばしたり、かがめたりといった姿勢が必要なため、意外にツライ作業だったのだとか。とはいえ、この機械1台導入するだけで、いったいいくらかかったのか……さすがは人を大切にする企業ですね。
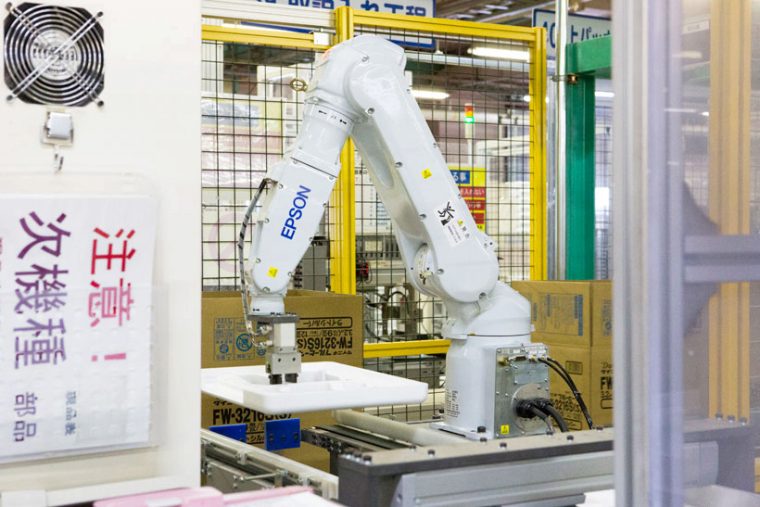
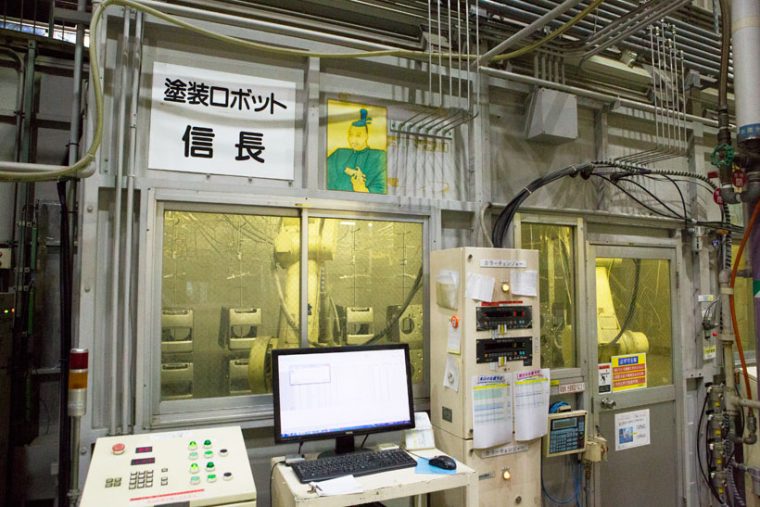
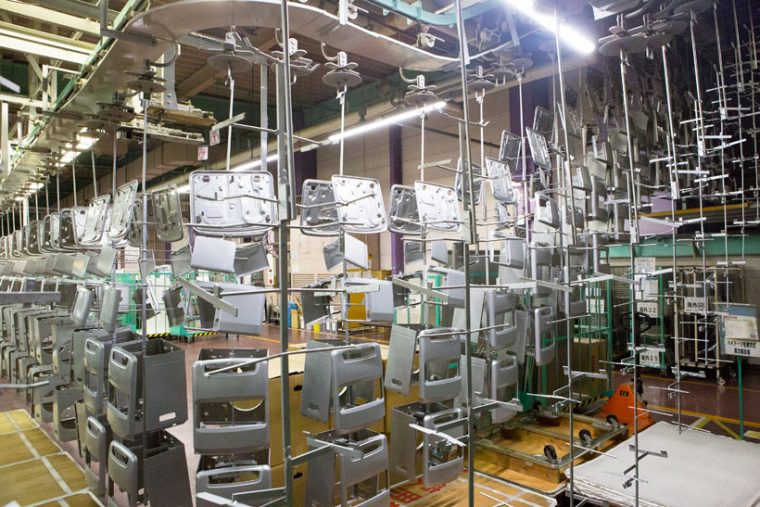
一体は一作業のみ! 驚きの効率を生むロボットの使い方
ところで、製品の開発から自社で行うダイニチ工業。じつは、工場のロボットも、多くが自分たちで改良、メンテナンスをしているそう。なんと、なかには自分たちで作った機械も存在します。

また「一体のロボットに一つの作業」を割り当てるのもダイニチ工業ならでは。たとえば、前述した「発砲スチロールをダンボールに入れる」ロボットは、本来ならば「ダンボールを組み立てて、発泡スチロールを入れる」など、複数の動きを複雑にこなせる性能があります。ところが、あえてひとつの作業に特化させることで、ロボット製造元さえも驚くレベルの作業効率を実現しているそう。また、一体のロボットに一つの作業しかさせないことで、ロボットに問題が起きても修理がしやすいなどのメリットもあるそうです。う~ん、どこまでも合理的!
石油ファンヒーターは全製品が燃焼テストされていた!
石油ファンヒーターは、燃えやすい「燃料」をタンクに保存するため、安全性の高さも重要です。このため、工場内ではさまざまな製品チェックも行われていました。たとえば、給油タンクは、タンクに圧力をかけて「漏れ」がないかテストする「油漏れ検査」専用の大きな機械も導入されています。
また、驚くのは組み立て途中の製品すべてに燃料を入れ、すべてに「燃焼検査」をしていたこと。数台に一台だけを検査する「抜き打ち検査」ではなく、全製品がテストされているのです。
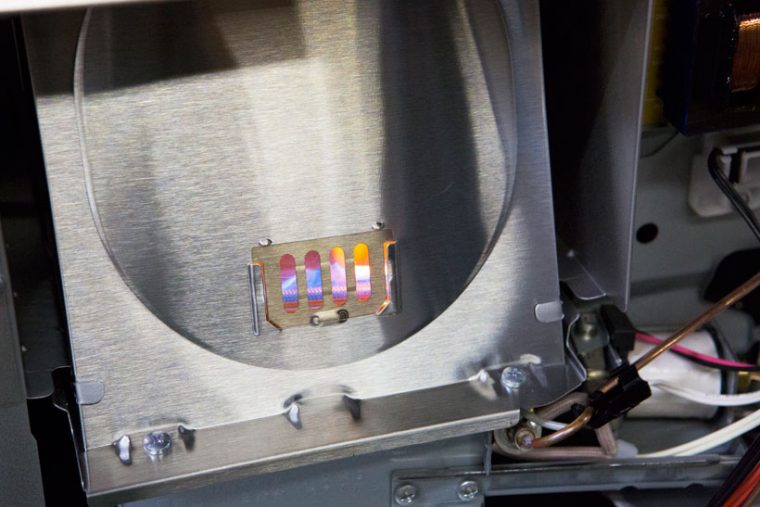
【ダイニチの最新ファンヒーターの関連動画はコチラ】
https://youtu.be/krSGJdUOnD0
なんだこの製品の山は!? 欠品ナシを実現する巨大倉庫
工場見学のあとは、ダイニチ工業の倉庫も見学させてもらいました。じつは、ダイニチ工業は一年中工場が稼働しています。このため、夏や秋にもどんどん在庫を生産し、冬に一気に販売。このため、非常に多くの製品が倉庫に積まれているのです。
実際に倉庫を見せてもらうと、あまりの製品量にただただ圧倒。まるでエジプトのピラミッドのようにダンボールが積み上げられています。しかし、同社によると「8月のピーク時を過ぎているので(※取材時は10月)、すき間がありますね。この倉庫にある製品は今38万台くらいでしょうか……ピーク時なら50万台ほどになるのですが」とのことでした。
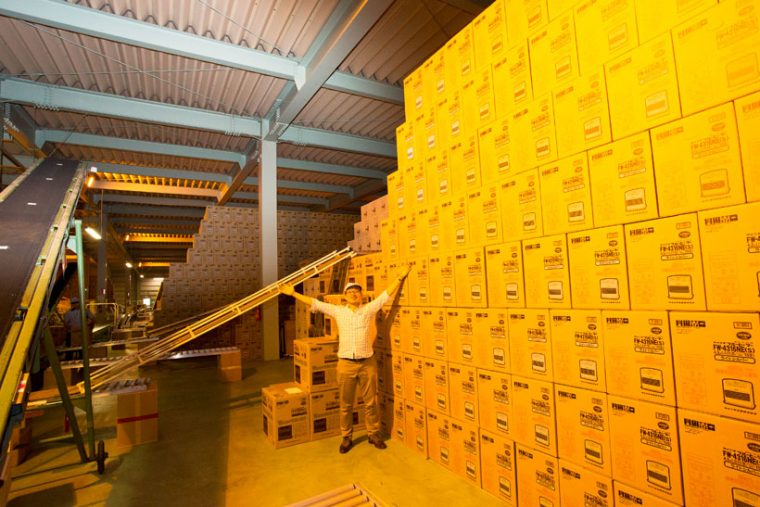
今回の見学で感じたのは、工場の居心地よさや、ロボット導入による単純重労働の排除など、とにかく社員が働きやすい環境が整っていること。それぞれが気持ちよく働ける環境だからこそ、安定して高品質な製品が作れるのだと実感しました。また、工程ごとに行われる、きめ細かな安全性チェックの厳重さも見逃せません。石油ファンヒーターは、室内に可燃物をもちこむ製品だけに、この安心感はうれしいものです。
そして、「ハイドーゾ生産方式」と、巨大倉庫による「欠品を作らない」という意気込みにも驚かされました。今回の見学で、ダイニチ工業が日本のシェアのトップを走る理由の一部を垣間見た気がします!
ダイニチ加湿器の情報はコチラ
ダイニチ石油ファンヒーターの情報はコチラ
ダイニチ工業 http://www.dainichi-net.co.jp/
撮影/中村介架