ドラゴンクエストのテーマ曲を奏でながら無人ロボットが工場内を走り回る。そんなユニークな環境下で生産が行われているのがパナソニック オートモーティブシステムズの松本工場(長野県松本市)です。同工場が目指すのは、“多品種少量生産”“変動生産”に追随できる生産基地の実現にあります。今回はそんな目標に向けて改革が進む同工場の生産現場を取材しました。
パナソニック オートモーティブシステムズ松本工場は操業50周年!
「パナソニック オートモーティブシステムズ(以下、PAS)」は、パナソニックグループにおいてカーナビゲーションなど車載機器事業の開発・生産することを役割としています。その松本工場の敷地面積は東京ドーム1.5個分に相当する6万9000m2で、建屋面積は2万7400m2。従業員数は社員が480名で、これにパートナー会社の派遣を含めると1300~1400人が働いているということです。
同工場が操業を開始したのは1974年のことで、当時の主力製品はカーラジオでした。それから今年でちょうど50周年を迎え、その間、生産品目はクルマの進化と共にカーオーディオやカーナビゲーション、ETCなどへと変化。現在は車内のエンタテイメントや車両側の様々な機能を一括してコントロールするIVI(in-vehicle infotainment)を主力とし、その実績は今や同工場で生産される製品の約半分を占めるそうです。
PASでは国内生産拠点として松本工場以外に5つの工場を持ちます。車載スイッチやセンサーなどの設計開発、製造を行う福井県敦賀市の「敦賀工場」と、車載カメラやETC車載器の量産開発と製造を行う福島県白河市の「白河工場」も、松本工場と同様、2024年に50周年を迎えました。
松本工場を含むこれら3つの工場は、それぞれの生産品目において主力として位置付けられ、最先端のモノづくりを実践。海外10か所にある生産拠点のマザー工場としての役割も担っているということです。なお、松本工場では、これまでカーナビゲーションも生産していましたが、IVIの生産拡大に伴い、カーナビゲーションは2024年4月、新たに生産拠点となる松阪工場(三重県松阪市)へと移管。PASの事業拡大に貢献している状況にあります。
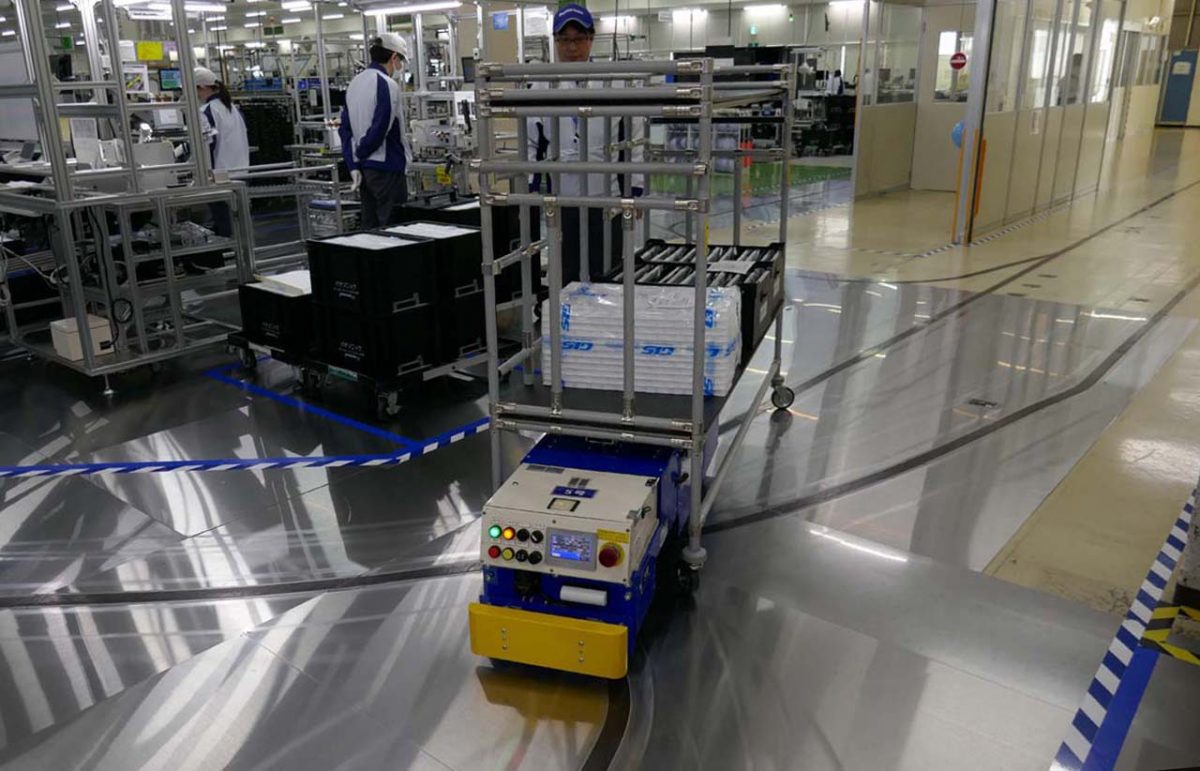
この日、挨拶に立ったPASインフォテイメントシステムズ事業部 松本工場の粟澤学工場長は、世界的に進む“SDV(Software Defined Vehicle)”への対応に言及し、「自動車産業は100年に一度という大変革期を迎え、クルマはソフトウェアのアップデートで機能がバーションアップされる時代を迎えています。そこでは走る、曲がる、止まるといった基本性能だけでなく、移動空間の快適性が求められており、それに合わせて車載コクピット領域に異業種からも多くの企業が参入し、競争が激化している状況」との認識を示しました。
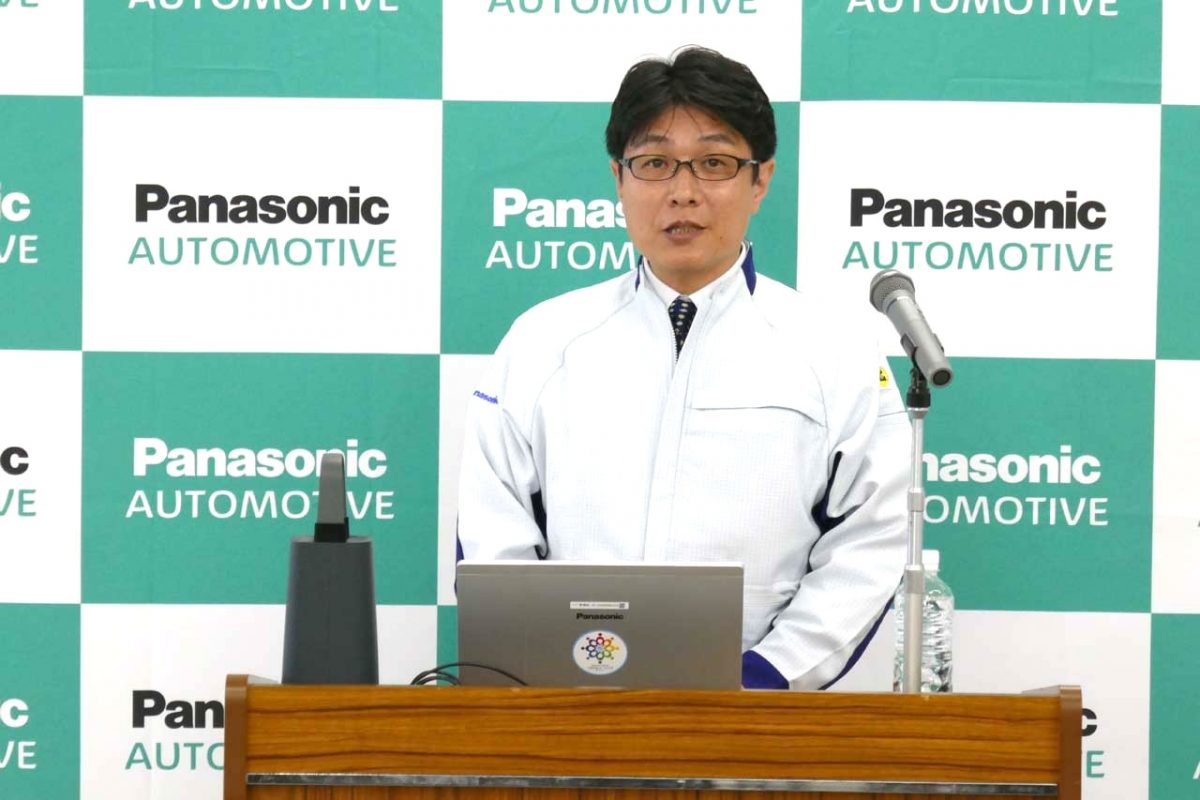
さらに、そうした中にあっても「松本工場は世界ナンバーワンのシェアを持つディスプレイオーディオと、世界2位のシェアを持つIVIを生産しています」として、同工場での事業が順調に展開されていることに粟澤氏は胸を張りました。
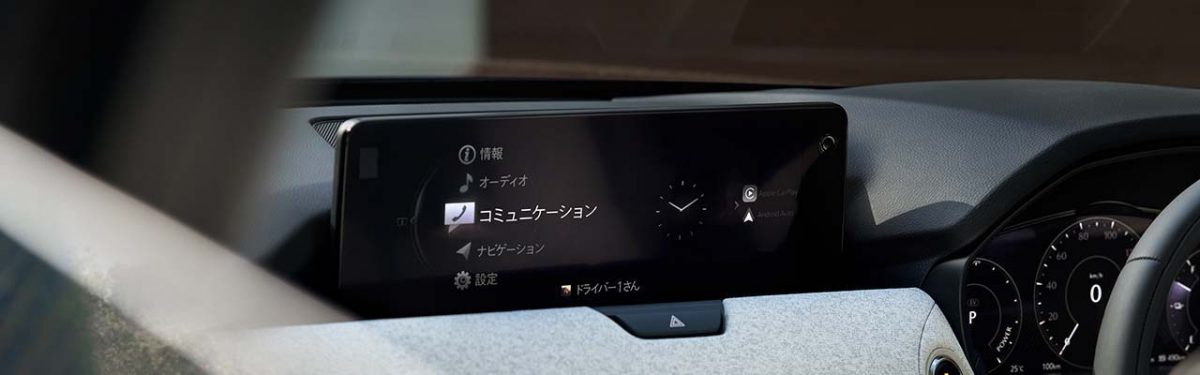
では、その成果の背景にはどういった要因があるのでしょうか。それは松本工場が目指す、「多品種少量、変動生産に追随できる業界ナンバーワンのモノづくりイノベーター」としての取り組みにありました。
粟澤氏は「消費者ニーズは多様化しており、一つの車種でもディスプレイのサイズが違っていることも少なくありません」と述べました。実際、某カーメーカー向けのIVIシステムの例では、一つのシリーズで500種類以上の多品種少量生産に対応する必要があったそうです。
その結果、松本工場で生産しているIVIでは、品番がおよそ700機種にもおよび、生産ロットでは100台以下が生産台数の7割。これによる松本工場の月間の機種切り替え数は、3000回以上に達しました。これはPASが展開するほかの工場と比べても、もっとも多い数字。しかしそのニーズは、すでに従来の生産方法では対応しきれない状況になっていました。
とはいえ、普通に考えれば、この多品種少量生産は稼働率の低下に伴ってコストアップにもつながる危険性もはらみます。大量量産こそが低価格を実現する重要な要素である、というのがこれまでの常識だったからです。
この点について粟沢工場長は、「我々はこうした状況を(逆に)ビジネスチャンスとして捉え、変種変量生産にジャストインタイムで対応する追従力を高め、高効率生産を実現していく」と語りました。ここに同事業部がグローバルでトップランナーにつながる秘密が隠されていたというわけです。
生産現場での“見える化”が重要
では具体的にどのような取り組みをしているのでしょうか。松本工場でまず実践されているのが生産現場での“見える化”です。
この実現のために採用したのがタイムスタンプの活用。粟澤氏は「リードタイム(発注から納品まですべての工程にかかる時間)やサイクルタイム(商品の製造にかかる時間)、中間在庫などの見える化につながり、どこがボトルネックになっているのかを把握しやすくなります。これをもとに、リードタイム削減に向けた取り組みを行っていく」というわけです。
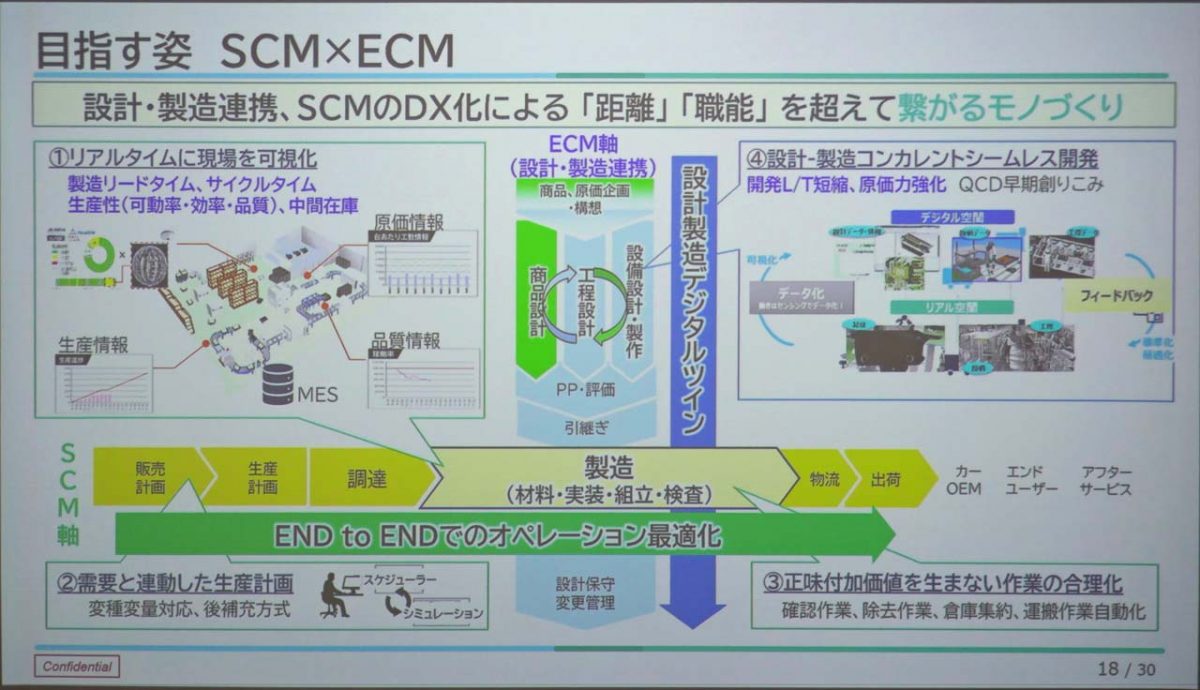
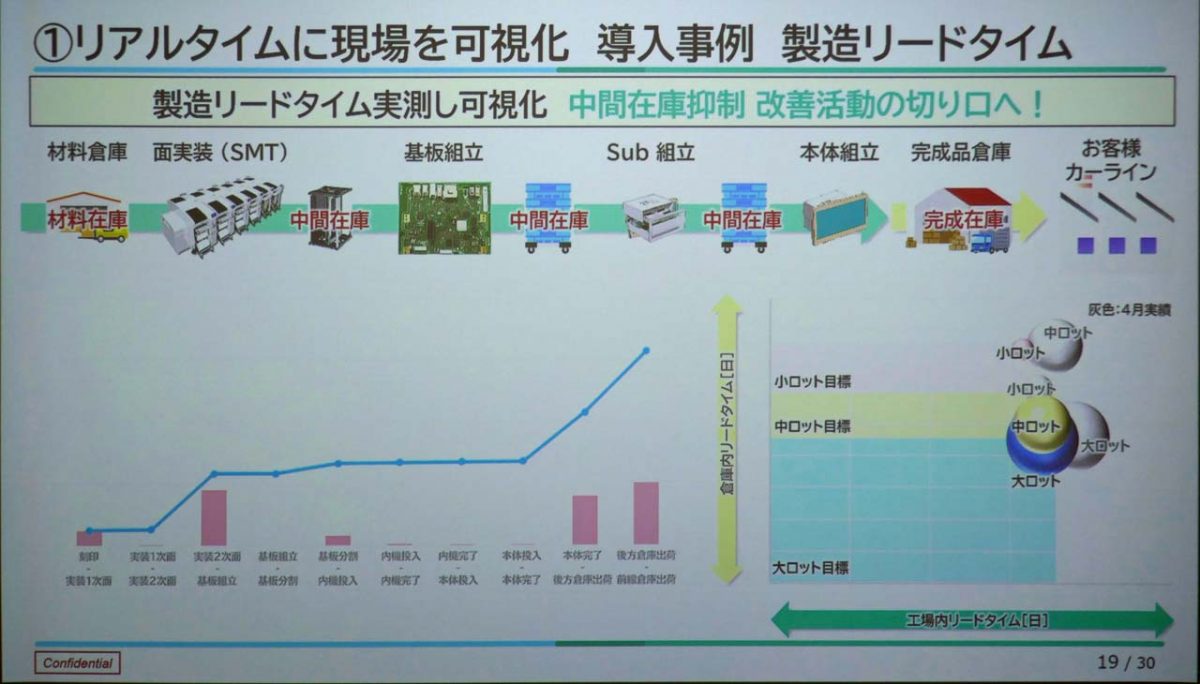
また、2023年から導入した「後補充生産方式」も重要な役割を果たしています。これは、完成品倉庫の販売実績をもとに毎日8日先の1日分の生産計画を確定させるもので、急な減産があっても柔軟に生産調整ができるメリットがあります。一方で「生産開始まで15日かかっていたのが、材料の在庫次第ではあるが8日に短縮できる。この方式は顧客にとってもメリットが生まれる」(粟澤工場長)ということでした。
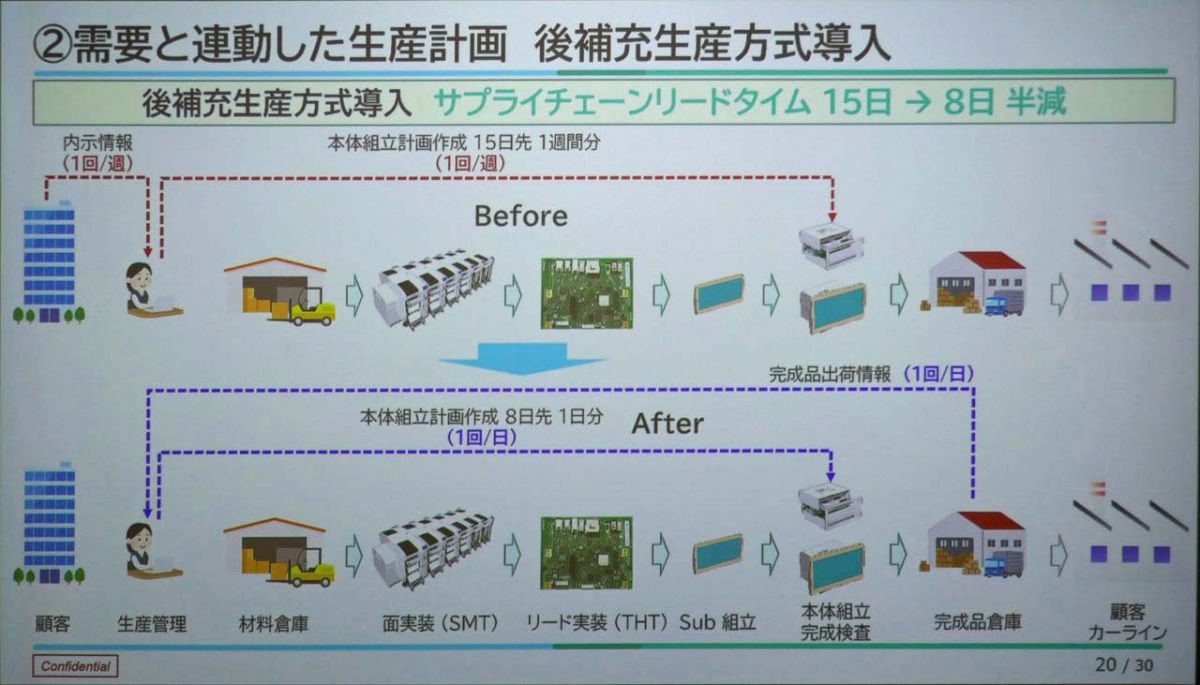
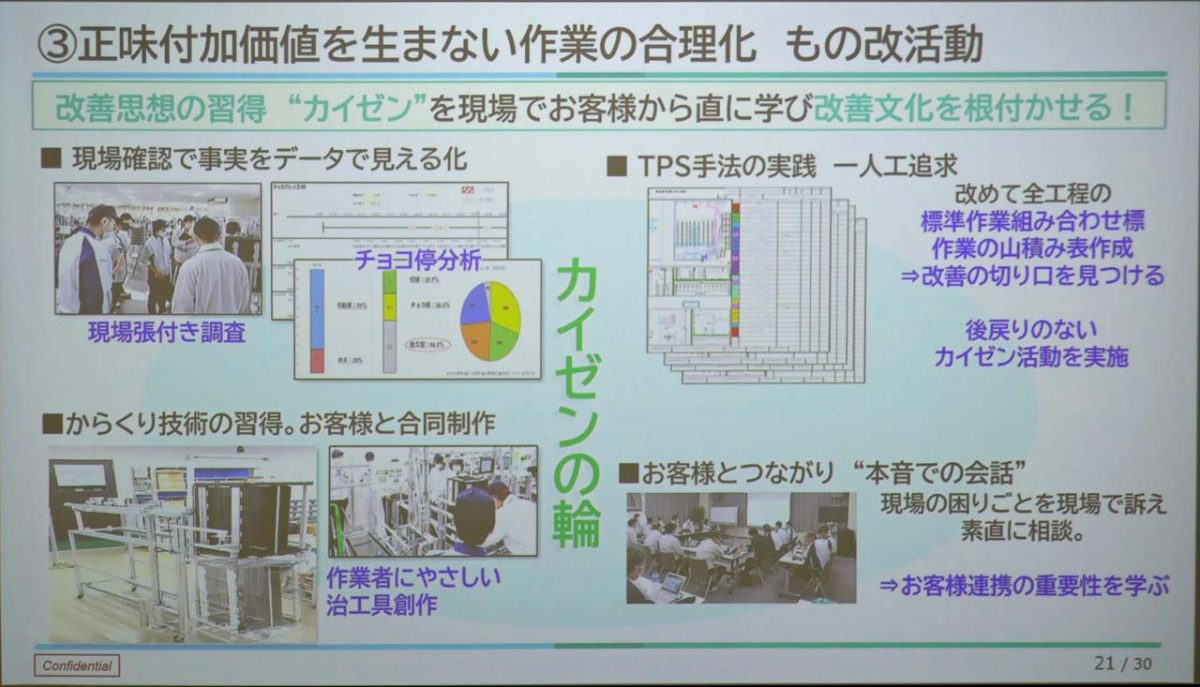
また、工場としては社会貢献の意味から、脱炭素化への取り組みを積極的に進めることが欠かせません。松本工場では毎年3%ずつ省エネ率を高める活動を行うと共に、2050年までに再生エネルギー率100%も目指すとのこと。すでにカーポートの屋根に太陽光パネルを組み込む活動を2024年7月から開始し、さらには2024年2月からはオフサイトPPA(Power Purchase Agreement)による電力供給をスタート。2025年度にはオンサイトPPA導入計画も進行中とのことでした。
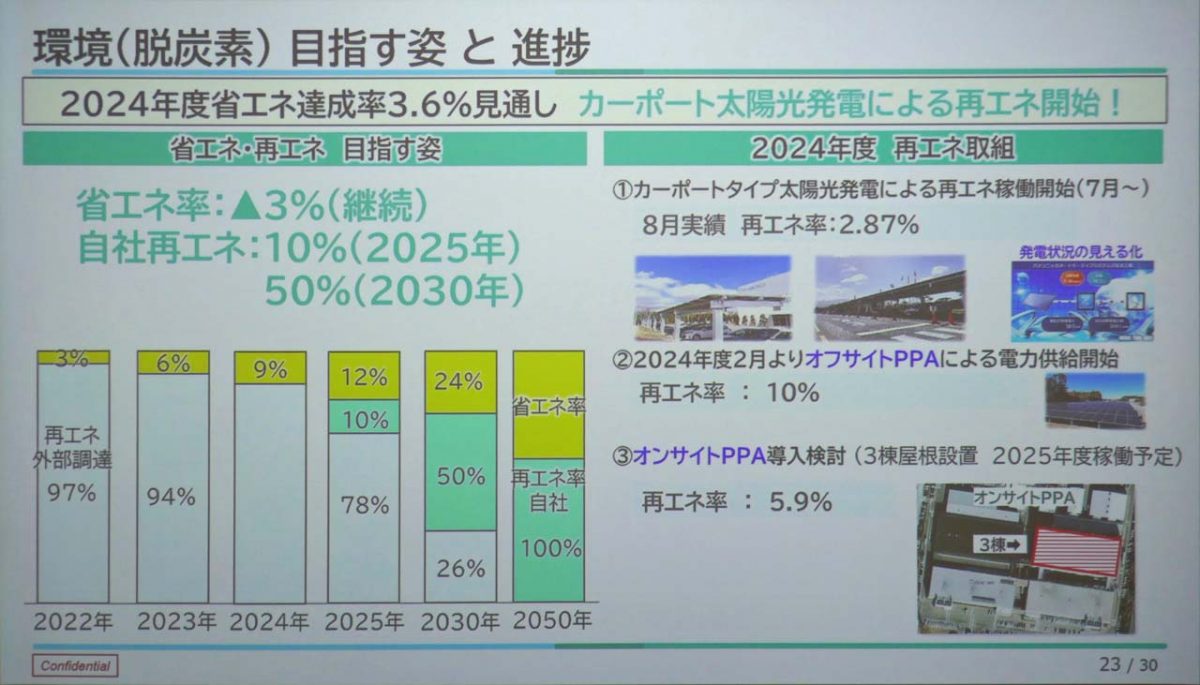
パナソニック オートモーティブシステムズ松本工場。実際の作業工程の一部がコチラ↓
「モノを作る前に人を作る」で土台づくり
そして、松本工場で特に重視しているのが、社員一人ひとりによる「土台づくり」への取り組みです。その中核となるのが「ひと繋がり改善活動」で、ここでは「大部屋、小部屋」と呼ぶ仕組みを導入。オフィス内の大部屋はガラス張りで外から見えるようにした上で、社員が誰でも入れるような環境とし、さらに小部屋では現場の困りごとを拾い出して全員で課題を解決。互いに助け合う風土を作り上げようというわけです。これによって、緊急事態の発生や、自然災害による被害に対しても独断即決ができる環境づくりにつながったのです。
この根底には、パナソニックの創業者である松下幸之助氏の「モノを作る前に人を作る」という言葉が息づいているとのこと。粟澤氏は「こうした中で一人ひとりが活躍できるような経営を実践し、イキイキワクワクできる松本工場を作り、それが日本のモノづくりへの貢献につながるよう心がけて参りたい」として、この日の説明を締めくくりました。
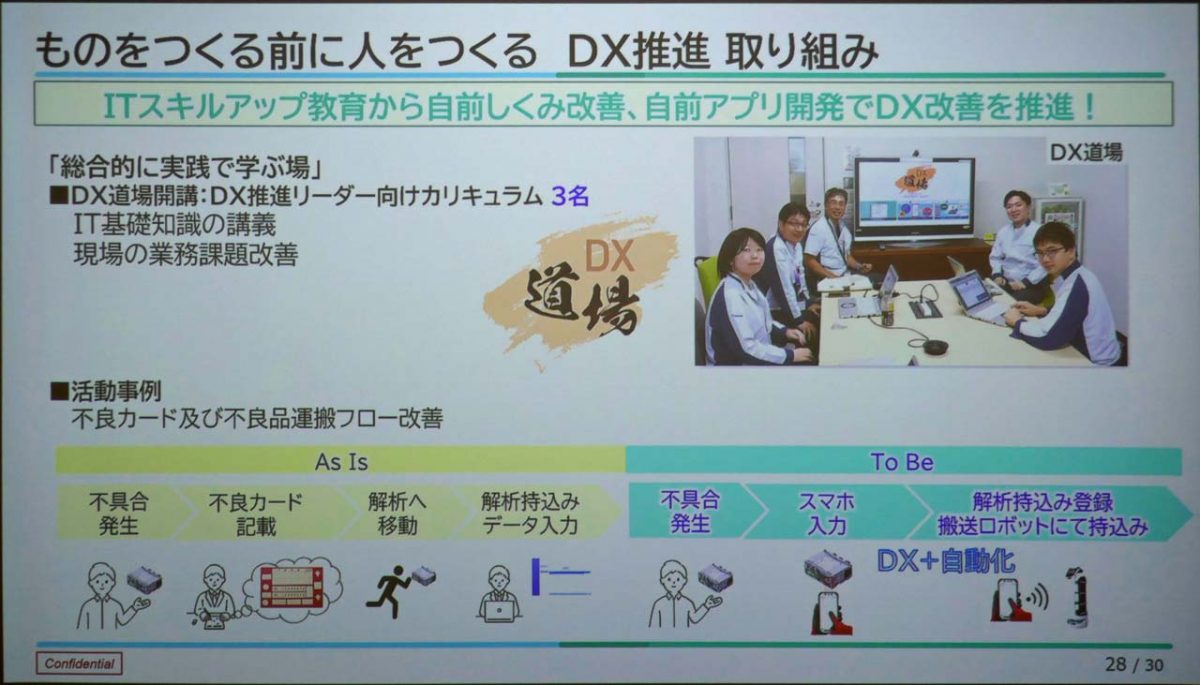
【フォトギャラリー(画像をタップすると閲覧できます)】